[Image above] The progression of flash sintering on a lanthana–zirconia bilayer in an 800°C furnace with 300 V/cm field applied and current limited to 100 mA/mm2. Credit: Jalali and Raj, Journal of the American Ceramic Society
There is no question that ceramic processing must become more energy efficient to lower costs and reduce carbon emissions. Such efficiency is particularly critical for fabricating high-temperature ceramics, a process where sintering temperatures can exceed 1,700°C. Beyond the energy required to achieve these temperatures, the time required to heat and cool the ceramic products is expensive and can lead to grain growth, which can diminish performance.
Flash sintering may provide a solution to these issues for some producers. In flash sintering, parts are still heated, albeit to lower temperatures, and high voltages are applied across the part. A current through the part is the result, which can be observed by electroluminescence (the flash effect). Under these conditions, sintering occurs in a matter of seconds or minutes, whereas traditional sintering methods can take hours.
Not only is flash sintering energy and time efficient, it can also produce parts that are high density (low porosity) while retaining small grains. For example, the images below show high purity aluminas that were sintered by pressureless sintering at 1,650°C (left), flash sintering at 1,300°C (middle), and high-pressure sintering at 1,400°C (right). Though the high-pressure sintered material had higher density than the flash-sintered sample (99.9% versus 97.9%), the flash-sintered sample had higher hardness (20.4 GPa versus 19.3 GPa).
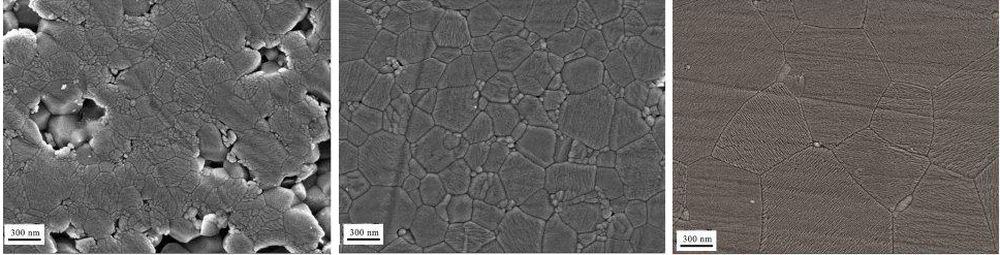
Credit: Yang et al., Journal of the American Ceramic Society
While the results of flash sintering are impressive, the mechanisms and forces are still not well understood. Four recent articles published in ACerS journals characterize and quantify atomic-level phenomena contributing to the flash sintering of oxide ceramics, namely alumina and zirconia-based oxides.
In these articles, the authors identify five stages of the flash process: heat-up, induction, flash, steady-state, and cool-down.
- During heat-up, the sample is brought to the ultimate furnace temperature without applied voltage.
- Induction is the period between application of the voltage field and the initiation of the flash current. When the sample is sufficiently conductive, the flash current initiates.
- During the flash, which occurs on timescales from less than one second to a few seconds, current rises until it reaches or exceeds a preset limit.
- Once flash occurs, the applied voltage is reduced to maintain the current at steady state.
- The final stage is cool-down, where the applied field is shut off and the sample is returned to room temperature via furnace cooling or more rapid methods.
Most researchers focus on doing measurements and modeling during the flash and steady-state phases, though some interesting results have arisen from studying the heat-up, induction, and cool-down stages.
For example, processes such as solid-state reactions of raw materials and the initial stages of sintering have been observed during heat-up. It is believed that atomic level changes occur during induction, which improve conductivity of the ceramic. Structure coarsening and precipitation of undesirable phases have been observed with slow cooling.
During the flash phase, processes occur at highly accelerated rates. For example, Yang et al. observed densification changing from about 60% to more than 90% in approximately 0.5 seconds, while Jalali and Raj measured diffusion coefficients nearly several orders of magnitude greater than that measured during sintering at similar temperatures. Furthermore, activation energies calculated for changes during flash sintering were substantially lower than similar changes for traditional sintering methods.
These studies sought to explain the underlying reasons for these observations and measurements. An obvious possibility is the formation of liquid materials within the flash zone. After all, Joule heating does lead to dramatic increases in temperature. However, the maximum temperatures measured by pyrometer or calculated from black-body radiation models fell below the melting points of pure alumina or yttria-stabilized zirconia, though one open-access study by Aoki et al. showed temperatures above the eutectic point for alumina-gallium aluminate mixtures.
While full conversion of the ceramic to liquid is unlikely, Jalali and Raj point out that increases in the free volume of 3–4% account for similarly high diffusion rates in metals. They cited their and other experiments showing a similar 3–4% volume expansion during flash sintering. They posit a “flash plasma” with spatially dispersed increase in entropy.
Yang et al. discussed contributions from oxygen vacancies and other point defects toward high rates of densification. Using energy dispersive spectroscopy, they determined that alumina lost oxygen atoms during flash sintering, which supports their hypothesis. They further compared activation energies during the flash and during steady-state phases to clarify diffusion mechanisms. Their analysis points to the likelihood that during the flash phase, columbic effects along with very high temperatures lead to grain-boundary diffusion, which drives sintering, while lattice diffusion drives densification during the steady-state phase.
While flash sintering shows great promise for improving both properties and processing of sintered ceramics, studies such as these ones help ceramic scientists understand the underlying mechanisms. With this information, ceramic engineers can design and tailor materials and manufacturing approaches to yield products with structures engineered to meet rigorous application performance requirements.
For more information, links to the four ACerS journal articles are below.
Jalali and Raj, “Reactive flash sintering in a bilayer of zirconia and lanthana: Measurement of the diffusion coefficient in real time,” Journal of the American Ceramic Society. https://doi.org/10.1111/jace.18804
Yang et al., “Flash sintering of ultra-high pure alumina ceramics with fine microstructure.” Journal of the American Ceramic Society. https://doi.org/10.1111/jace.18554
Yang et al. “Densification behaviors of Al2O3 ceramics during flash sintering,” International Journal of Applied Ceramic Technology. https://doi.org/10.1111/ijac.14205
Aoki, Masuda, and Yoshida, “Formation of Al2O3–GdAlO3 eutectic ceramics with a fine anisotropic structure in a flash event,” Journal of the American Ceramic Society. https://doi.org/10.1111/jace.19012
Author
Jonathon Foreman
CTT Categories
- Basic Science
- Manufacturing