[Image above] Credit: SuperJet International; Flickr CC BY-SA 2.0
[Editor’s note: This report comes to us from Sanjay Sampath, PhD, Distinguished Professor and Director of the Center for Thermal Spray Research at Stony Brook University.]
by Sanjay Sampath
Researchers from Stony Brook University’s Center for Thermal Spray Research (CTSR) recently reported significant advancements in the development of durable thermal barrier coatings (TBCs). TBCs are critical materials used in hot sections of gas turbine engines, enabling improved efficiencies through higher turbine operating temperatures.
Yttria partially stabilized zirconia (YSZ) has been the workhorse material of present day TBCs. However, YSZ TBCs are limited in temperature capability (typically to <1200 °C) and rapidly degrade in the presence of molten silicate deposits (arising from ingested desert sand, volcanic ash, or coal ash).
There has been considerable research both within academia and industry to find suitable alternatives to YSZ that can simultaneously accommodate higher temperature operation and resistance to silicate attack. While several novel compositions have been identified as possible solutions, deploying them in service mandates successful implementation of the materials via processing.
A key challenge with implementing new low conductivity TBC ceramics is the relatively low intrinsic fracture toughness of advanced compositions compared to YSZ. For instance, gadolinium zirconate (GZO) offers low conductivity, sinter resistance, and ability to withstand molten silicate attack—in fact, GZO has already been implemented in aero engines.1
However, the fracture toughness of GZO is significantly lower than that of YSZ, with potential impact on the material’s durability. Of further importance is the material’s toughness sensitivity to defected microstructure, arising from both design requirements and processing (porous coatings substantially lower already low thermal conductivity and provide mechanical compliance).
In a series of publications that have recently appeared in the Journal of American Ceramic Society, the CTSR team has carefully examined the interplay among processing, fracture toughness, and durability of plasma sprayed TBCs. The fracture toughness of GZO and YSZ as a function of their process-dependent microstructure was obtained in collaboration with Oak Ridge National Laboratory using the double torsion technique.2
The results indicate both intrinsic and process-induced effects on material properties. Using this knowledge of toughness–microstructure–processing interplay, the team further developed multilayer strategies in which coating toughness was spatially engineered to target greater durability.
In the case of YSZ, a bilayer coating was fabricated, consisting of a tough interfacial layer to offer resistance to crack propagation and a porous second layer to reduce available elastic energy in the overall system. Under furnace cycling conditions, these coatings provided significantly enhanced durability compared to traditional porous TBCs.3 Such bi-layer TBCs also provide a balance of properties in terms of durability and low thermal conductivity.
Extending this concept, a three-layer coating was developed in which a GZO coat was applied on top of the bilayer YSZ system. Here, a dense vertically cracked form of GZO was sought to provide better erosion resistance as well as defense against calcium–magnesium–alumino–silicate deposits.
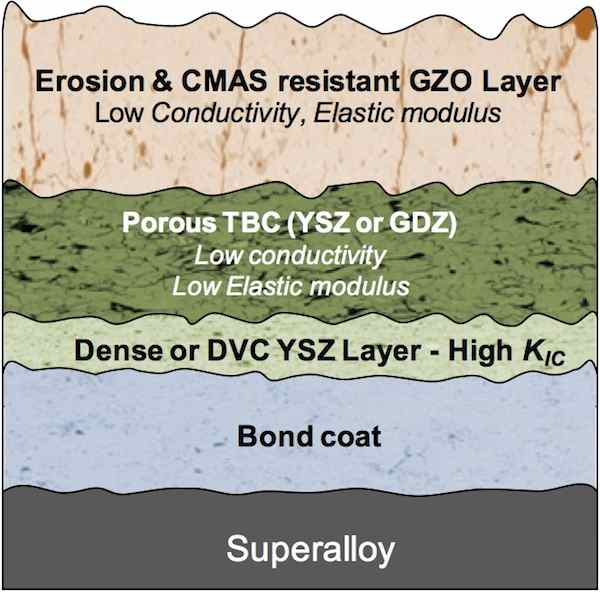
Schematic illustration of the multilayered multifunctional thermal barrier coatings. Credit: S. Sampath
Such property-optimized, three-layer coatings also showed excellent furnace cycle durability with initial results confirming the suitability of a GZO top coat in molten silicate-laden environments. Further, the team explored several configurations of the multimaterial coatings and rationalized their failure through available elastic energy formulations.
The results couple the interplay between available elastic energy to drive failure with the toughness of the material at failure location. These results provide a framework for process-enabled design of multimaterial, multilayer coatings.4 By taking advantage of process parametrics to design robust coatings, the concepts can be readily transitioned to manufacturing.
Discussions along these lines are underway with the Stony Brook Industrial Consortium for Thermal Spray Technology partners.
This work was supported by Department of Energy’s University Turbine Systems Research (UTSR) program, in conjunction with support from Stony Brook Consortium. Collaborative support from Oak Ridge National Laboratory, Siemens Energy, and Saint-Gobain are gratefully acknowledged.
References
- G. Dwivedi, Y. Tan, V. Viswanathan, and S. Sampath, “Process-property relationship for air plasma-sprayed gadolinium zirconate coatings,” Journal of Thermal Spray Technology, 24[3] 454-66 (2015).
- G. Dwivedi, V. Viswanathan, S. Sampath, A. Shyam, and E. Lara-Curzio, “Fracture toughness of plasma-sprayed thermal barrier ceramics: Influence of processing, microstructure, and thermal aging,” Journal of the American Ceramic Society, 97[9] 2736-44 (2014).
- V. Viswanathan, G. Dwivedi, and S. Sampath, “Engineered multilayer thermal barrier coatings for enhanced durability and functional performance,” Journal of the American Ceramic Society, 97[9] 2770-78 (2014).
- V. Viswanathan, G. Dwivedi, and S. Sampath, “Multilayer, multimaterial thermal barrier coating systems: Design, synthesis, and performance assessment,” Journal of the American Ceramic Society, doi:10.1111/jace.13563 (2015).
Contact:
Sanjay Sampath, Distinguished Professor and Director,
Center for Thermal Spray Research
Department of Materials Science and Engineering
Stony Brook University, NY 11790
sanjay.sampath@stonybrook.edu
Author
April Gocha
CTT Categories
- Aeronautics & Space
- Material Innovations
- Transportation