[Image above] Eugene A. Cernan driving the Lunar Roving Vehicle on the moon during the Apollo 17 mission. Fifty years since the Apollo program, dust mitigation remains an issue for NASA. Credit: Kevin Gill, Flickr (CC BY 2.0); original photo available at this link
I do not often drive on gravel roads, but a recent trip to Iowa quickly reminded me how bumpy, noisy—and dusty—the ride is. The dust was just a minor annoyance that a trip to the car wash resolved. But for lunar landers and rovers, a quick rinse at the auto spa is not an option. And this continuous piling up of lunar dust can have severe consequences.
“We learned from Apollo that lunar dust can be less than 20 microns (about 0.00078 inches) in size. The dust is very fine, abrasive, and sharp, like tiny pieces of glass, making it more of a dangerous threat than just a simple nuisance,” says Sharon Miller, principal investigator of the passive dust shedding material program at NASA Glenn, in a NASA blog post.
In addition to clogging equipment and tearing spacesuits, the electrostatic properties of lunar dust also interfered with survey instruments. Even 50 years after the Apollo program, dust remains a challenge to lunar surface missions, as well as missions to Mars and other celestial bodies.
To keep dust from collecting on equipment, researchers to date have focused on active mitigation strategies, such as magnetic wands and electrodynamic dust screens. But these methods require either additional structures or the adoption of new materials, which can add time, complexity, and cost to a mission.
Instead, dust mitigation can take place passively by modifying the equipment’s surface to prevent adhesion of particulates. For example, engineering the surface to be hydrophobic, or water repellant, can reduce the possibility of adhesion, not only for dust but for pathogens as well.
Laser ablation, which removes material from a solid surface by irradiating it with a laser beam, is one way that researchers can engineer a surface to be hydrophobic. Numerous studies using this technique have shown that laser pulse duration and wavelength can drastically affect the laser ablation mechanisms.
In a recent open-access study, researchers from the University of Nebraska-Lincoln and NASA Langley Research Center attempted to induce hydrophobicity on the surface of two ceramic materials, boron carbide (B4C) and molybdenum aluminum boride (MoAlB), using a novel laser ablative patterning process. These ceramics were selected due to their importance in potential long-term lunar surface activity.
Their laser ablative patterning process involved a picosecond-pulsed ytterbium fiber laser with a wavelength of 1,030 nm. The laser had an average pulse duration of 2 picoseconds, a nominal output power of 50 W, and a 100 kHz repetition rate. Patterning took place at room temperature in air.
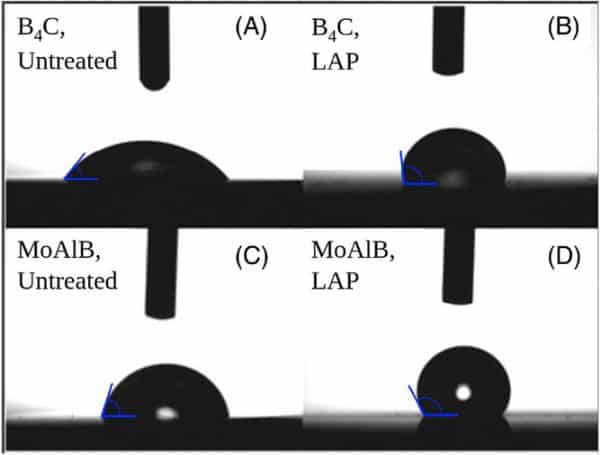
Photos showing the contact angle of a water drop (5 μL) on B4C and MoAlB. Contact angles were measured to be (A) 61° for untreated B4C, (B) 96° for patterned B4C, (C) 79° for untreated MoAlB, and (D) 131° for patterned MoAlB. Credit: Ruiz et al., Journal of the American Ceramic Society (CC BY 4.0)
After patterning, the surfaces of both B4C and MoAlB transitioned from being hydrophilic (contact angle <90°) to hydrophobic (contact angle >90°). This transition had a marked effect on dust adhesion, with both the patterned B4C and MoAlB samples exhibiting effectively reduced dust adhesion.
However, the only slightly hydrophobic B4C most effectively reduced adhesion of fine dusts (≤5 μm), while the near superhydrophobic MoAlB effectively reduced adhesion of all lunar dusts (up to 32 μm).
“These initial tests suggest a correlation between surface treatment and particulate adhesion, which was also observed in polymer samples in the literature,” the researchers write. “The correlation will be further studied by our team to interpret the electrostatic interaction mechanisms between the hydrophobic ceramic surfaces and lunar dust simulant.”
To learn more about lunar dust mitigation research, listen to the Ceramic Tech Chat podcast episode with co-author Valerie Wiesner, research materials engineer in the Advanced Materials and Processing Branch at NASA Langley Research Center.
The open-access paper, published in Journal of the American Ceramic Society, is “Laser ablative patterning of B4C and MoAlB ceramics for hydrophobic surfaces” (DOI: 10.1111/jace.19283).
Author
Lisa McDonald
CTT Categories
- Aeronautics & Space