[Image above] Practices that are commonly perceived as sustainable may not provide the desired benefits within every individual or group’s workflow. Credit: Mikhail Nilov, Pexels
As someone who is part of the aerial dance community, I greatly appreciate the emphasis that my teachers place on listening to your body. Just because stretching is generally good practice for athletes, after an injury, forcing certain poses can exacerbate the damage and make it take longer to heal.
This same advice applies to the field of sustainable manufacturing. Just because certain practices are generally considered beneficial, their adoption can negatively impact production if the practices are implemented poorly or not a good fit for that company.
The importance of critically evaluating perceived green technologies before adoption is demonstrated in a recent open-access paper. The authors come from the Technical University of Darmstadt, and the study follows a “Letter to the editor” that the authors published in the September 2023 Bulletin on evidence-based sustainable development.
In the Letter, the authors argued for conducting sustainability assessments during the early stages of materials/product development. Identifying potential negative environmental impacts at the start would help alleviate the need for difficult process modifications during later developmental stages.
Their new paper demonstrates the types of impacts that may be caught during early assessments. Specifically, they showed that microwave-sourced heating, which generally is believed to consume less energy than conventional heating sources, may actually consume more energy in certain cases.
This study’s specific case was the synthesis of (La0.9Ca0.1)2Ni0.75Cu0.25O4±x, or LCNC, a promising oxygen transport membrane material. The authors previously published an open-access paper that identified factors impacting sustainability when producing LCNC through a Pechini-based sol-gel process. The new study focused on the factor of electricity consumption.
The authors compared the electricity consumption and environmental impacts from three production setups:
- The original Pechini-based sol-gel process.
- Reference process: same as original setup but with a reduction in calcination time (from 10 hours to 2 hours).
- Modified process: same as reference setup, but the heating sources were changed from a hot plate (for gelation) and electric resistance heating furnace (for pre-calcination and calcination) to a microwave-heating-sourced furnace.
While each setup resulted in the production of LCNC membranes with comparable functionalities, the reference process consumed 6 kWh less electricity than the original production setup. However, the modified process consumed more electricity than the reference process, by more than 65% for primary LCNC and more than 90% for secondary LCNC.
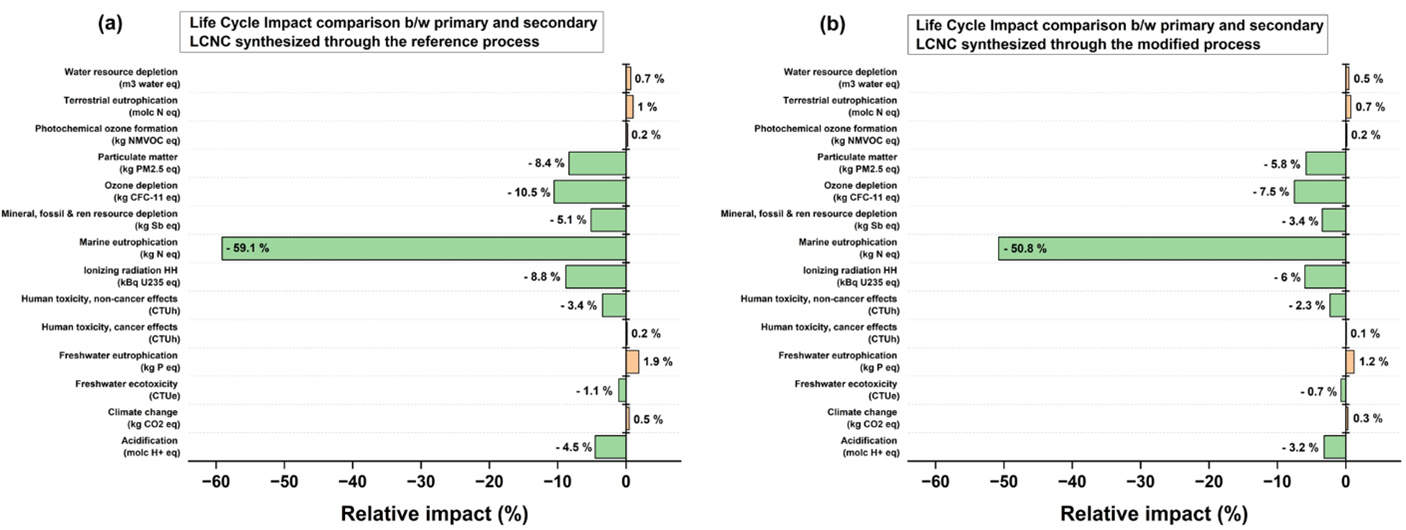
Life cycle impact comparison between the primary and secondary LCNC synthesized through (a) reference process and (b) modified process. Credit: Kundu et al., Open Ceramics (CC BY-NC-ND 4.0)
Why did the microwave-sourced heating process consume vastly more electricity than the conventionally heated process in this case? In an email, first author and TU Darmstadt graduate student Rishabh Kundu explains that this increased consumption appears to be due to energy losses in the furnace.
“The energy consumption of the furnace used for the study can be measured in two ways: through an energy meter plugged into the socket powering the furnace, or by mathematically integrating the power against time graph obtained through the software used to control the furnace,” he says.
He explains that the latter method does not account for any energy losses and simply states the magnetron power with respect to time. It also does not account for energy consumed by other nondetachable components, such as the ventilation system software controller. As such, if energy consumption is reported using this method, microwave-sourced heating appears more sustainable than the reference process.
However, the first method accounts for all kinds of energy losses, including from the magnetron, and energy consumed by all the components because it records the actual energy consumption. Using this method resulted in the conclusion that the microwave-sourced heating process was less energy efficient for this specific case study.
Kundu suggests that engineering magnetron efficiency in the microwave setup may reduce electricity consumption, but this hypothesis requires further investigation.
So, “while methods for pursuing sustainable materials development are generally broadly applicable, this study reemphasizes the need for manufacturers to evaluate the impact that comes from using each method within their specific context—not everything appearing green may be genuine,” Kundu says.
The open-access paper, published in Open Ceramics, is “All that seems green might be a smokescreen – a case study on microwave-integrated process development of oxygen transport membrane material” (DOI: 10.1016/j.oceram.2023.100534).
Author
Lisa McDonald
CTT Categories
- Education
- Environment