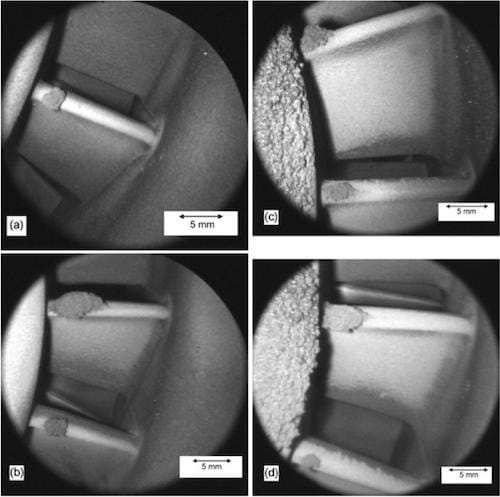
Volcanic ash deposits in a turbojet. (a) Fine particle size, minimal deposits.; (b) Medium particle size, lumps of deposit on blades and combustion chamber wall; (c) Medium particle size, deposit covers more than 50% of combustion chamber wall; (d) Coarse particle size, deposition of leading edges of blades and combustion chamber wall deposits greater than 1 mm. Credit: Clyne, et al.; AEM, Wiley.
We sure do love to fly. According to United States Bureau of Transportation statistics, more than 642 million passengers boarded aircraft in the US in 2012 and more than 170 million flew internationally in 2012. Interestingly, international air travel is trending upwards while domestic air travel is just starting to rebound from a five-year downward trend that coincided with the US recession.
The beating heart of an airplane is its engines and, like human hearts, bad things happen if they get clogged. Volcanic ash is to jet engines what saturated fat is to a heart. Like bad fats, the best remedy is to avoid volcanic ash. Many will remember (some of you vividly, because you were stranded yourselves) the havoc that followed the eruption of Iceland’s Eyjafjallajökull volcano in 2010, with the closure of parts of European airspace for up to eight days. The closure rippled through the global air transportation system, causing the cancellation of almost half of all flights—a total of 108,000, affecting about 10 million passengers. The airline industry estimated the shutdown cost in the neighborhood of $200 million per day.
The concern was that the volcanic ash could melt inside the hot jet engines, vitrify on internal surfaces, and cause catastrophic engine failure. Volcanic ash is a mostly amorphous calcia-magnesia-alumina-silica composition already, and volcano ash plumes can linger in the atmosphere for days. Vitrified ash can plug cooling lines or deposit on turbine blade surfaces and nozzle guide vanes, all of which can lead to hot spots in the engine, overheating, and failure. Also, the oxide-based ash can react with yttria-stabilized zirconia protective coatings, causing it to destabilize and fail. Particle matter that enters the engine but does not deposit can cause serious erosion damage as it passes through.
One approach is to engineer better protective coatings. Another is to better understand what is happening in the engine and assess the risk of critical damage occurring. In a new paper in Advanced Engineering Materials, a University of Cambridge (UK) team led by professor T. William Clyne looked at the factors that contribute to volcanic ash sticking to surfaces of a turbine of a small turbojet engine, focusing on tow key parameters—gas (and particle) temperature and turbine surface temperature.
The group developed numerical models to describe particle motion and particle heating in the turbine, and tested their models by injecting actual volcanic ash from Iceland into a small jet engine. Four particle size distributions were studied. The glass transition temperature of the composition was 600–700°C, and the melting temperature of the residual crystalline mineral content was about 1,130°C.
The scientists found there is an interesting tradeoff between heat transfer effects and inertia effects. Small particles heat up faster, but are more likely to stay in the gas stream and exhaust with the gas. Larger particles, however, are slower to reach the glass transition temperature but tend to fall out of the gas stream and deposit on stationary surfaces in the turbojet. And, although they are “cooler,” they will impinge on surfaces that are much hotter than Tg, which will enhance the likelihood of their sticking.
It is not possible to control or plan for a volcanic eruption. However, one lesson from this study, the authors conclude, is that the risk presented by an ash plume depends on particle size distribution, the degree of particle amorphicity, and glass transition temperature. They suggest characterization of airborne ash “may be a useful practical measure.”
The paper is “Deposition of ingested volcanic ash on surfaces in the turbine of a small jet engine,” by Maya Shinozaki, Kevin A. Roberts, Bennie van de Goor, and T. William Clyne, Advanced Engineering Materials, (DOI: 10.1002/adem.201200357).
ACerS members may download one Wiley article per month for free by logging into the ACerS website and clicking on the Wiley Download Direct program.
Author
Eileen De Guire
CTT Categories
- Aeronautics & Space
- Thermal management
- Transportation