[Image above] “Honeycomb” monolith diesel exhaust filter on left compared to Empa’s ceramic foam substrate filter, right. Credit: Empa.
By this time next year, Europe will be enforcing a tough, new standard on exhaust emissions from trucks and busses. Starting in September 2014, all new passenger and many lighter-weight commercial vehicles in regions covered by the European Commission’s rules will be required to have “Euro 6”-certified engines, and, in response, vehicle manufacturers and various research groups have been accelerating their filtration R&D. Switzerland’s Empa is of the institutions focusing on this issue, and researchers there say they are excited about some unconventional restructuring of the main filter components—typically ceramic substrates—that they say will enable manufacturers to meet pollution goals.
Heretofore, the standard diesel emissions filter is an extruded honeycomb-structure ceramic (e.g., cordierite) substrate that has a light coating of a catalytic material, such as platinum or palladium, which allows it to convert NOx and CO in the exhaust and capture soot. The honeycomb monolith substrate can withstand the stresses of temperature cycling during normal use and also during “regenerative” cycles when collected particulates (soot) are removed.
The conventional approach to engineering these filters is to allow exhaust gasses to pass through relative easily while providing maximum exposure to the surfaces bearing the catalyst. Turbulence was a thing to be avoided.
However, one research group at Empa, its Internal Combustion Engines Laboratory, says there is a downside to the honeycomb monolith: The flow of the exhaust gasses is distributed unevenly. Most of the exhaust gasses pass through the center section of the filter, creating a high-temperature zone and leaving much of the outer regions of the honeycomb relatively unused. To compensate for the unused regions, Empa says the honeycomb filters have to be relatively long (besides adding general manufacturing costs, the extra length also means the use of extra expensive catalytic material).
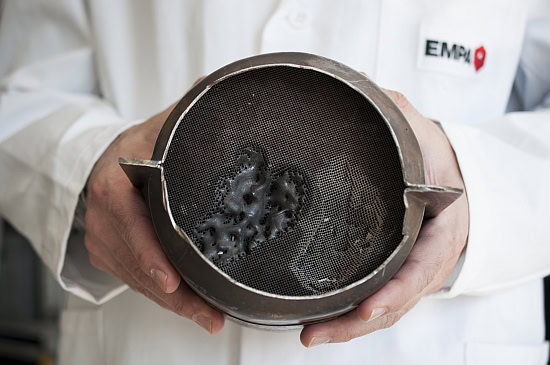
This honeycomb catalyst from a racing car was the trigger that gave the Empa researchers the idea of developing the Foamcat. A small area of the monolith has melted, but neighboring areas are almost unused, indicating that the exhaust gas flow is poorly distributed through the device. Credit: Empa.
Empa claims that the impetus for rethinking the filter design was the viewing of a diesel filter whose central section had partially melted (see photo). The researchers’ novel idea, which began to emerge a few years ago, was to embrace the turbulence of the exhaust and put it to use to distribute the gasses more evenly.
But, a rugged ceramic substrate to support the catalyst would still be needed, and the Internal Combustion Engines Lab turned to researchers in Empa’s High-Performance Ceramics Laboratory. Instead of relying on the straight-through openings of a honeycomb, the ceramics group began to tinker with a special catalyst-coated ceramic foam, which they subsequently named Foamcat. The structure of the foam would encourage the turbulence needed to more evenly distribute the exhaust through the filter.
To filter engineers, the Empa approach probably raises several questions, especially in regard to the mechanical strength of a ceramic foam and to the negative effects of the turbulence, i.e., loss of engine performance due to back pressures from the exhaust. In response, a news release from the institute says
[S]cientists succeeded in increasing the mechanical strength of the material many times over. Currently the research team is working to optimize the structure of the ceramic—the foam substrate has a greater air resistance than the monolith that results in a slight comparative increase in fuel consumption. Using sophisticated computer simulation techniques, the Empa team has developed foam structures which reduce the air resistance without affecting the necessary turbulence.
According to Empa, the bottom-line benefit is that the surface area of the Foamcat substrate is much more efficiently used than with a honeycomb monolith. It claims that the efficiency is improved so much that the Foamcat filter can match the performance of a honeycomb filter at half the length and only requires one third of the expensive catalysts.
Whether vehicle manufacturers ultimately embrace the ceramic foam design remains to be seen. The problem of the expense of noble metal catalysts is vexing to manufacturers and other groups have been trying to find substitutes such as acicular mullite.
Nevertheless, Empa says it has been partnering for over a year with catalyst-maker Umicore and diesel engine manufacturer Fiat Powertrain Technologies to do field tests with a Foamcat filters. It also says that Swiss electrical utility IWB has been testing a vehicle fitted with the Foamcat filter for 18 months.
The stakes are high. According to a document (pdf) on the Euro 6 standards prepared by Cummins, all NOx emissions will have to be 75 percent less and particulate matter will have to be 66-95 percent less than current “Euro 5” limits.
Author
Eileen De Guire
CTT Categories
- Environment
- Manufacturing
- Modeling & Simulation
- Transportation