[Image above] Credit: Purdue University/Raymond Hassan
The cost of solar power is slowly decreasing.
Data from the Solar Energy Industries Association indicates that the U.S. solar industry is growing exponentially. Earlier this year, Business Insider, citing a study by Lazard, reported that it costs around half as much to produce one megawatt-hour of electricity from solar power ($50) as it does to produce the same amount of electricity from coal in North America.
So why is solar only providing 1.3% of electricity generation in the U.S.?
The missing piece to that puzzle is in the cost of generation and storage of solar power. The 2017 Lazard Report states that energy storage technologies have yet to be cost-competitive in most applications, and that “alternative energy systems alone will not be capable of meeting the base-load generation needs of a developed economy for the foreseeable future.”
But researchers from Purdue University have already developed a way to reduce the cost and increase efficiency of generating electricity. Led by Reilly Professor of Materials Engineering Kenneth Sandhage, in collaboration with Georgia Institute of Technology, University of Wisconsin-Madison, and Oak Ridge National Laboratory, the team created a novel ceramic-metal composite material that could replace materials typically used in heat exchangers in solar power plants.
“Storing solar energy as heat can already be cheaper than storing energy via batteries, so the next step is reducing the cost of generating electricity from the sun’s heat with the added benefit of zero greenhouse gas emissions,” Sandhage explains in a Purdue news release.
Solar power plants generate electricity by collecting sunlight to produce heat that goes through a system, using a turbine engine that powers an electricity-producing generator. But in order to reduce the cost of generating electricity from solar power, the engine would have to produce more electricity for a given amount of heat, according to the release.
The amount of heat produced from a heat exchanger is limited to the materials it’s made from. They’re typically made of stainless steel or nickel alloys that cannot accommodate higher temperatures required to produce additional electricity at a specific heat level. But Sandhage and his team created plates out of a ceramic-metal composite of zirconium carbide and tungsten that include customized channels to facilitate improved heat exchange.
The research teams from ORNL and Wisconsin-Madison ran extensive tests for corrosion, increased temperature and pressure, and efficiency. For example, they found that the ZrC/W-based plates’ thermal conductivity tested two to three times higher than iron or nickel alloys at the same temperature, according to the abstract.
The Georgia Tech and Purdue teams conducted a cost analysis to determine that their ceramic-metal composite would be cheaper to produce at scale than stainless steel or nickel alloy-based heat exchangers.
The scientists have filed a patent and plan to continue their research. Their breakthrough could be a huge advancement in lowering the cost of producing energy from solar power.
“Ultimately, with continued development, this technology would allow for large-scale penetration of renewable solar energy into the electricity grid,” Sandhage adds. “This would mean dramatic reductions in man-made carbon dioxide emissions from electricity production.”
The paper, published in Nature is “Ceramic–metal composites for heat exchangers in concentrated solar power plants” (DOI: 10.1038/s41586-018-0593-1).
Watch the video below to learn more.
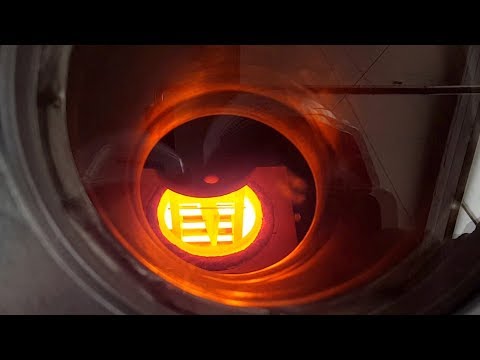
Credit: Purdue University, YouTube
Author
Faye Oney
CTT Categories
- Energy