Credit: Mariordo, Wikimedia (CC BY-SA 2.0)
As I write this, ambient temperatures are soaring around the northern hemisphere, reaching over 40°C in the United Kingdom for the first time ever. Some argue we are very close to the global climate tipping point.
In response, governments around the world are pouring funding and resources into building up renewable energy infrastructure to reduce reliance on greenhouse-gas-emitting fuels. However, relying solely on wind and solar power is challenged by the fact these technologies cannot provide a reliable baseload, which is the constant minimum flow of energy required to fulfill basic electricity demands.
Nuclear and fossil fuel power plants readily provide baseloads while fuel is supplied. However, the latter option recently is less reliable in areas that depend on natural gas from Russia.
Hydroelectric power plants, which generate electricity using flowing water, also can provide reliable baseloads. For example, Canadian electricity company Ontario Power Generation maintains a storage pond near Niagara Falls that has reversible pumps. During the night they widen the water intake gates above the falls, which increases power generation and reduces water to the falls. The excess power is used to fill the reservoir, which then delivers energy as it is emptied during the day when the hydroelectric inlet flows are reduced and the falls are brought back to their splendor.
But hydroelectric is in jeopardy now as well. Rising temperatures and rainfall changes are shrinking the reservoirs behind the hydroelectric dams. Lake Mead, the largest reservoir in the United States and where Hoover Dam is located, has fallen 158 feet in the last two decades. The lake’s water level currently measures 1,041 feet, and the Bureau of Reclamation says the lake levels must stay above 1,000 feet to continue operating the dam’s hydropower turbines.
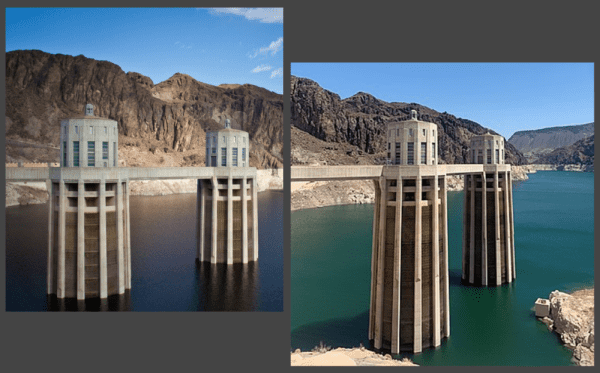
Left, Hoover Dam water levels in 2012. Right, Hoover Dam water levels in 2021. Credit: (Left) Tony Webster, Flickr (CC BY 2.0); (Right) 北纬的星空, Wikimedia (CC BY-SA 4.0)

Instead of pumping and discharging water like hydroelectric power plants, batteries charge and discharge by the motions of ions and electrons. In a typical battery, the metal in the anode gives off electrons during discharge to form positive ions. The electrons flow through the external circuit while the ions migrate through the electrolyte and are deposited in the cathode and reunited with electrons to reform the metal.
In primary batteries, this flow of electrons and ions only happens once and then the battery is spent. In contrast, a reverse polarity voltage applied to rechargeable batteries drives the metal ions and electrons back to the anode, much like electricity runs the pumps to lift water into the reservoir near Niagara Falls. The batteries can then repeat the discharge/charge process.
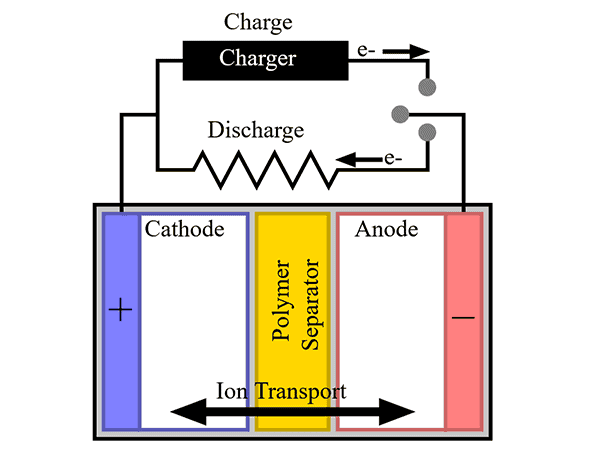
Schematic of a battery showing electron and ion transport during charge and discharge. Credit: Tkarcher, Wikimedia (CC BY-SA 3.0)
There are other types of battery systems, but all involve the internal flow of ions and the external flow of electrons. Fuel cells work similarly, though they use fuel such as hydrogen at the anode and oxygen at the cathode. Electrolyzers generate hydrogen or other useful chemicals by essentially running a fuel cell in reverse.
The lead-acid rechargeable battery has been around for more than 150 years. It is the most reliable and cost-effective device for transportation (auxiliary systems and small-scale motive) and stationery (e.g., backup power) applications.
However, lead-acid batteries are heavy and bulky and do not work for portable electronics or large-scale transportation, such as electric vehicles and airplanes. Plus, they contain toxic and corrosive materials and release hydrogen off-gassing during recharge, posing explosion hazards that must be addressed.
Lithium-based batteries are the best energy storage solution presently for portable and transportation applications, offering high energy in compact and lightweight packages.
Unfortunately, lithium batteries have some substantial shortcomings. The issue with greatest notoriety is the fire hazard that plagued toys and phones and even the Boeing 787. Other issues include uncertainty in the supply and pricing of cobalt and lithium and various performance parameters, such as longevity and costs.
Substantial ceramics research projects are addressing these issues by improving or replacing lithium battery technology. A quick search for “lithium” and “battery” on https://ceramics.onlinelibrary.wiley.com reveals more than 200 entries since 2017 alone.
A selection of recent papers in The American Ceramic Society journals highlights some of the efforts toward new electrolyte, cathode, and anode materials.
Oxide coatings for cathodes
The key goal for cathode research is reducing or eliminating the cobalt used. Lithium cobalt oxide cathodes have good performance, but they are expensive. Other technologies include replacing some cobalt with manganese, aluminum, and/or nickel.
Two cobalt-free options include lithium iron phosphate (LFP) and lithium manganese oxide (LMO). Both have good qualities, with LMO being used in the Nissan Leaf. The biggest downside of LMO is loss of capacity with charge–discharge cycling.
Authors of the recent International Journal of Applied Ceramic Technology (ACT) paper “Improved cycling stability of V2O5 modified spinel LiMn2O4 cathode at high cut-off voltage for lithium-ion batteries” note that the mechanisms leading to reduced capacity are initiated by loss of surface oxygen at high voltage. To avoid this loss, they tried coating an LMO cathode with vanadium oxide (V2O5).
The V2O5 coating strengthened the oxygen bonding to the manganese and weakened the bonding to lithium. This chemistry resulted in higher rates of charge transfer and lithium diffusion into and out of the spinel structure, along with stabilizing capacity over many charge-discharge cycles.
While the coating did improve these parameters, the initial capacity and cutoff voltage (high voltage on recharge) were lower than for samples featuring some other coating materials, such as SiO2 and TiO2. However, the other coatings resulted in higher capacity losses with cycling.
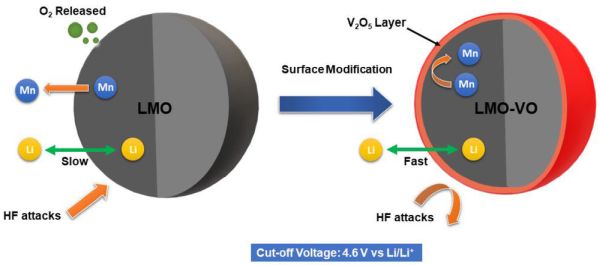
Schematic illustration of the functioning mechanism of V2O5 coating layer. Credit: Radzi et al., International Journal of Applied Ceramic Technology
High-entropy materials for electrolytes
One approach for improving the safety of lithium-based batteries is replacing the highly flammable organic liquid or polymeric electrolytes with solid-state ceramics.
Electrolytes based on lithium lanthanum metal oxides (LLMO) show promise due to high lithium-ion conductivity, wide operating voltages, and good mechanical properties. The choice and amount of the metal dopants (M) influences these properties, and research is being performed on a wide range of metals including zirconium, tantalum, niobium, aluminum, tellurium, and tungsten, along with mixtures of these metals and others.
High-entropy materials garnered much attention recently due to the stabilizing effect of having multiple metals with ranges of sizes and oxidation state occupying crystal sites. As the name of a recent Journal of the American Ceramic Society (JACerS) article suggests, “Processing and characterization of an Li7La3Zr0.5Nb0.5Ta0.5Hf0.5O12 high-entropy Li–garnet electrolyte,” the authors synthesized LLMO with equimolar amounts of zirconium, niobium, tantalum and hafnium. The ceramic electrolyte was sintered at 1,100°C to 94% density with small grains and homogenous distribution of the elements.
Electrochemical testing showed high ionic conductivity (4.67 x 10-4 S/cm) and extremely low electronic conductivity (~10-8 S/cm). Low electronic conductivity is necessary to minimize leakage currents/self-discharge while the battery is idle. They attribute the high ionic conductivity to the different dopant radii stabilizing the cubic structure and maximizing the lithium-ion disorder and vacancies.
Oxides and glass-ceramics for anodes
Like with cathodes, structure stabilization and increased capacity are goals for new anode materials as well. Lithium batteries mostly use graphite for the anode. While graphite easily accommodates intercalation and release of the lithium ions during the charge–discharge cycle, its total charge capacity is rather low. Lowering the cost of batteries and extending the range of electric vehicles both depend upon increasing the charge (energy storage) capacity.
As with the cathodes, anodes must conduct both electrons and ions while minimizing the distance the lithium-ions must diffuse into the structure. The authors of the ACT article “High entropy oxide nanofiber by electrospun method and its application for lithium battery anode material” combined the structural integrity of high-entropy magnesium–cobalt–nickel copper–zinc oxides with low-cost electrospinning process.
Prior studies showed this oxide has good properties, particularly with nanoscale particles. The keys to this study are the format, which accommodates electrical conduction along the fiber direction while the lithium enters and exits radially, and the stability achieved using a proven, scalable fabrication method.
Their results are promising, with high stability of capacity over many cycles. However, the low initial capacity indicates more work is needed for commercialization.
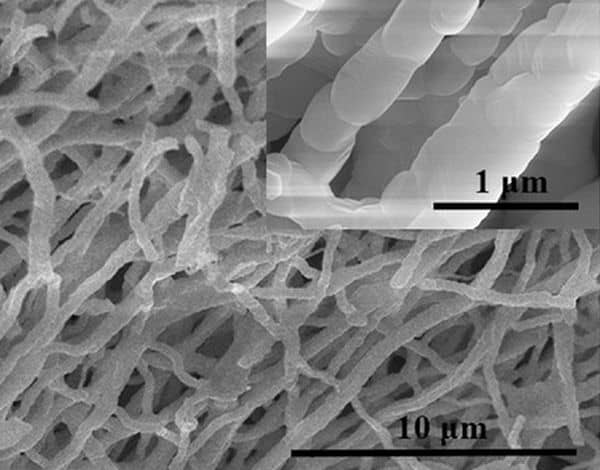
SEM of electrospun HEOs. Credit: Su et al., International Journal of Applied Ceramic Technology
Another study in JACerS also focuses on facile fabrication of distinctively structured crystalline materials for high stability and high capacity. In the article “Micro/nanostructured Bi2Mn4O10 with hierarchical spindle morphology as a highly efficient anode material for lithium-ion batteries,” the title material is synthesized via hydrothermal methods without surfactants or templates. The resulting materials have nanoscale crystals agglomerated into ovoid (egg or spindle-shaped) particles that are about 0.9 μm in diameter and 2.95 μm in length.
The materials showed high initial capacity, high stability of the reversible (usable) capacity, and good electrode kinetics. The authors attribute the material’s performance to the pores and the nanoscale crystals accommodating the volume change and shortening the lithium diffusion paths, and the spindle shape providing electrical connectivity.
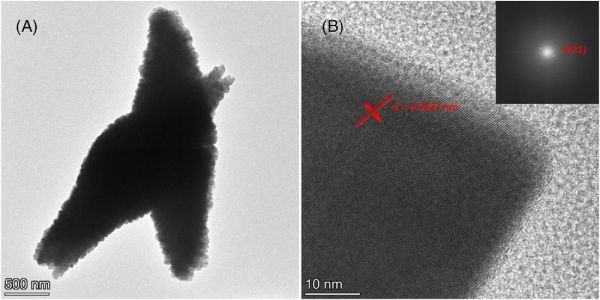
TEM of spindle-shaped particles of nanocrystalline bismuth manganate. Credit: Cheng et al., Journal of the American Ceramic Society
A third approach uses glass iron phosphate for the anode material. The loose network structure of glass readily accommodates insertion and removal of lithium during charging and discharging. However, the glassy state has insufficient electronic conductivity to be a good electrode material.
The authors of “Iron-phosphate glass-ceramic anodes for lithium-ion batteries,” appearing in the International Year of Glass special issue of International Journal of Applied Glass Science, found that reducing the iron phosphate and allowing it to partially crystallize created a glass-ceramic with promising performance characteristics. While the capacity dropped by 50% initially during cycling, after about 50 cycles the capacity began growing, reaching close to the original value at around 700 cycles. After that point, capacity fell again but more slowly.
The authors showed that the crystals in the material experienced an order–disorder transition. The resulting material was in an amorphous state, although with no glass transition when measured by DSC.
In summary, ceramics research for the next generation of lithium-ion batteries is robust. New materials are being developed while manufacturing studies are being performed on some of the more promising ones. With many predictions of electric vehicles comprising half or more of the new vehicles manufactured or sold by 2030, the enabling technology of ceramic battery components cannot be brought to market soon enough.
Author
Jonathon Foreman
CTT Categories
- Energy
- Material Innovations