[Image above] As wind energy becomes a larger share of the U.S. energy market, we need to improve the lifecycle sustainability of wind turbine blades. Credit: Johanna Montoya, Unsplash
At the end of August, the United States Department of Energy released three reports showing record growth in land-based wind energy, significant expansion of the pipeline for offshore wind projects, and continued decline in the cost of wind energy generation.
“[These reports] underscore both the progress made and the capacity for much more affordable wind power to come … At DOE, we will double down on efforts to deploy more wind energy around the country as we also pursue technologies to make turbines even cheaper and more efficient,” says Secretary of Energy Jennifer M. Granholm in a DOE press release.
What the press release fails to mention, though, is what will happen to all these wind turbines once they reach end-of-use.
As explained in a CTT post published at the beginning of this year, most decommissioned turbine blades are either stored in various places or taken to landfills because there are few options for recycling. Such an approach is not sustainable, especially if companies plan to deploy even more wind energy in the coming years.
Numerous companies and organizations are looking at ways to handle turbine waste in a sustainable fashion, and the earlier CTT post highlighted several of these projects. Today we look at the work being done by two more companies.
Carbon Rivers: Glass fiber reclamation and upcycling
The main reason wind turbine blades are so difficult to recycle is because they are made of fiberglass, a composite material.
“The mixed nature of the blade material makes separating the plastics from the glass fibers to recycle into a workable fiberglass material difficult—and the strength needed for the blades means they are also physically challenging to break apart,” a blog post by the Union of Concerned Scientists explains.
Carbon Rivers is one company working to overcome this challenge. Based in Knoxville, Tenn., Carbon Rivers develops and commercializes advanced materials “that will lead to a more sustainable and more technology driven future,” according to its website.
A few years ago, Ryan Ginder, research assistant professor at the University of Tennessee, Knoxville, approached Carbon Rivers with a proposal. He had developed a multistage pyrolysis process to reclaim glass fiber from wind turbine blades in a discontinuous form, which could then be upcycled into new composite products. (Not new turbine blades, though, as the structural components of the blades require continuous glass fiber.)
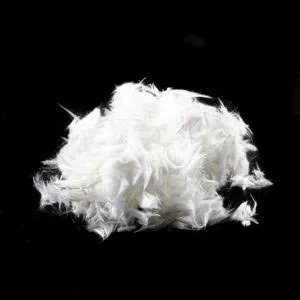
Reclaimed glass fiber from wind turbine blades. Credit: University of Tennessee, Knoxville
Ginder wanted to work with Carbon Rivers to further develop and commercialize the technology. Bowie Benson, founder and CEO of Carbon Rivers and alumnus of UT Knoxville, agreed to the partnership.
In 2019 and 2020, Ginder and Carbon Rivers received two grants totaling $1.25 million through the DOE’s Small Business Technology Transfer program to fund the project. They are now collaborating with partners including GE Renewable Energy and Berkshire Hathaway Energy’s MidAmerican Energy Company and PacifiCorp to develop a pilot-scale glass fiber composite recycling system that will serve as the basis for eventual deployment of a full-scale commercial wind blade waste processing plant.
In a press release this month, Carbon Rivers announced that it upcycled 100 tons of turbine blades in a year and a half, as per goals of the project’s first phase. Now, the company is moving to prove its technology at 20 tons a day, and in 2023 it expects to process 200 tons a day.
As it expands, Carbon Rivers plans to reclaim glass fiber from not only turbine blades but from auto, marine, and construction waste as well. In addition, it plans to explore reclamation of glass fiber in continuous form.
Though the scale-up plan is ambitious, David Morgan, vice president of business development at Carbon Rivers, believes it is the right approach to take.
“The demand globally is going to be hard to keep up with. Our scale up is going to be pretty ambitious and aggressive to meet the needs of global glass fiber streams. We really hope to make a global impact, so we’ll see what the next few months hold,” he says in the press release.
Siemens Gamesa: Recyclable wind turbine blades
In contrast to developing methods to recycle wind turbine blades as they are currently made, renewable energy technology company Siemens Gamesa is looking to reinvent how turbine blades are built in the first place.
On September 7, the company announced the launch of RecyclableBlade, which it says is the world’s first recyclable wind turbine blade ready for commercial use offshore.
“The RecyclableBlade is produced the same way as a standard blade and is based on the same IntegralBlade manufacturing process. The only difference is the use of a new type of resin that makes it possible to efficiently separate it from the other components at the end of the blade’s working life,” the company explains in an infographic on the new technology.
Siemens Gamesa already produced the first six 81-meter (266-foot) long RecyclableBlades at its manufacturing plant in Aalborg, Denmark. The company is now working closely with multinational energy company RWE to install and pilot the blades at the Kaskasi offshore wind power plant in Germany. In the future, Siemens Gamesa will work with EDF Renewables and wpd AG to install RecyclableBlades at their wind farms as well.
“The time to tackle climate emergency is now, and we need to do it in a holistic way. In pioneering wind circularity—where elements contribute to a circular economy of the wind industry—we have reached a major milestone in a society that puts care for the environment at its heart,” says Andreas Nauen, CEO of Siemens Gamesa, in the press release.
See the new RecyclableBlade in the video below.
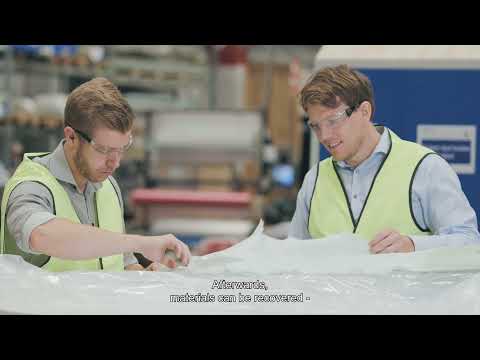
Credit: SiemensGamesa, YouTube
Author
Lisa McDonald
CTT Categories
- Energy
- Environment