[Image above] Credit: Peter Rüegg; ETH Zurich
Your toilet may soon undergo a metamorphosis in the way it is manufactured.
Researchers from ETH Zurich have developed a new way to manufacture ceramic products—such as bricks, porcelain, and cement—that saves energy and lowers the world’s carbon footprint.
André Studart, professor of complex materials, and Florian Bouville, a postdoc working on Studart’s team, have devised a room-temperature cold sintering method that uses hydraulics to produce ceramic materials that have proven to be stronger than concrete.
If you’re familiar with the traditional process of making ceramics, you know that manufacturers have to fire materials at temperatures in excess of 1,000oC (1,832oF). For instance, traditional ceramic tiles are fired in tunnel kilns that operate at 1,300oC (2,372oF). That sucks up a lot of energy that could be harnessed to power, say, a third-world country.
Starting with calcium carbonate nanopowder, Studart and Bouville simply added a little water and compacted the materials under extremely high pressure with a hydraulic press. The entire process takes only an hour to turn out a small one-inch piece of ceramic material.
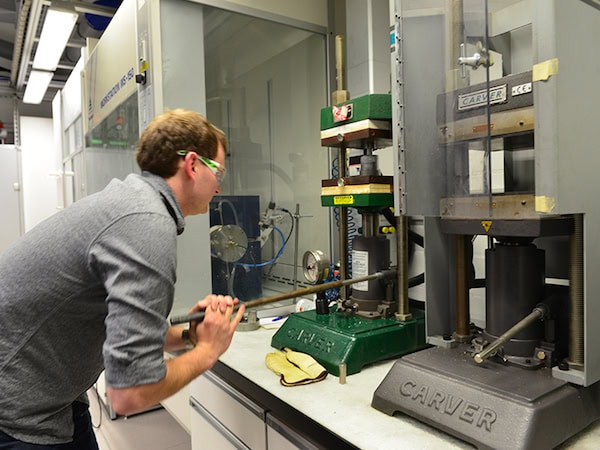
[Image above] Credit: Peter Rüegg; ETH Zurich
This revolutionary process has several positive implications for the industry:
- The finished product can tolerate ten times more force than concrete, according to the scientists;
- The cold sintering process is more energy-efficient, as no high temperatures are required;
- Carbon could possibly be captured from the atmosphere, stored in a carbon sink, and “recycled” to produce the nanopowder; and
- The process contributes to overall reduction of CO2 in the atmosphere.
Although Studart and Bouville used small samples in their experiments, the benefits to the ceramics industry need to happen at scale. Producing larger pieces will require stronger hydraulics that can generate higher pressure and greater force. However, the researchers say it would feasible to create ceramic samples the size of bathroom tiles.
Densification without heat as the primary driving force could have huge impact on our understanding of sintering mechanisms. Pennsylvania State University researcher, Clive Randall, has also made some interesting discoveries in cold sintering, by employing high pressures at low temperatures.
As the cement industry looks to adopt sustainable alternatives in the manufacturing process, Studart’s and Bouville’s research could provide alternative materials to answer some of the environmental challenges. Along similar lines, Richard Riman at Rutgers, the State University of New Jersey, also is working on low-temperature, sustainable manufacturing and has shown that CO2 incorporated into concrete not only captures CO2, but improves the end product.
The end result of research such as the ETH Zurich work, along with Riman’s and Randall’s work could lead to entirely new ways of thinking about manufacturing of ceramics, and could also disrupt the massive trillion-dollar concrete industry.
The paper, published in Nature Communications, is “Geologically-inspired strong bulk ceramics made with water at room temperature” (DOI: 10.1038/ncomms14655).
Author
Faye Oney
CTT Categories
- Cement
- Energy
- Environment
- Manufacturing
- Material Innovations