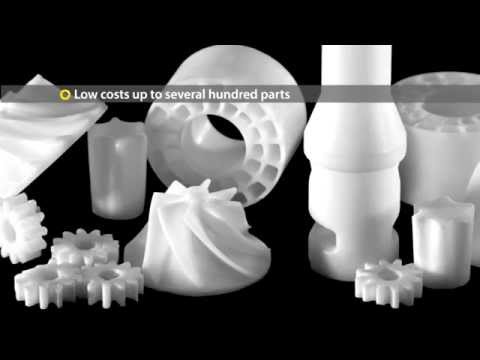
Additive manufacturing seems like a natural for making high-performance ceramic parts, such as screws. An Austrian company uses light to activate a photoinitiator to build ceramic parts one layer at a time. Credit: Lithoz
The market for metal and polymer industrial fasteners is about $12 billion, according to a Freedonia market study released last fall. With modest growth projections, Freedonia expects the market could reach $14 billion–$15 billion in the next five years.
“Industrial fasteners” encompasses a wide range of products: screws, bolts, rivets, washers—any hardware that joins components together.
The Freedonia analysts apparently did not think the market for ceramic fasteners was large enough to merit evaluation. Let’s hope they never break a bone and need it set with ceramic screws.
It is true that steel, titanium, and polymers can hold things together in most situations. However, there are notable exceptions. Ceramco (Center Conway, N.H.), a manufacturer of custom ceramic components, including screws, says on their website that ceramic fasteners are the preferred choice for applications requiring high temperature stability, corrosion resistance, nonmagnetic materials, wear resistance, electrical insulation, thermal expansion coefficient compatibility, stiffness and rigidity, biocompatibility, and high purity (no outgassing and chemical inertness). They manufacture components made of alumina and partially-stabilized zirconia.
Ceramic screws, however, bring the usual Achilles heel to the job—brittleness. A team of researchers in Germany considered the problem from two angles—determining what stress loads ceramic screws can bear and optimizing design of the component. The team includes researchers from the IVWM (Freiburg), the Fraunhofer Institute for Ceramic Technologies and Systems (Dresden), and the Technische Universität Berlin.
According to a Fraunhofer press release, some ceramics have load-bearing capacities similar to some steels; however, threading processes reduce ceramic screw load-bearing capacity by 80 to 90 percent. To determine loads that ceramic screws can support, researchers are testing a variety of ceramic screws and also developing computer simulations to accurately model stress distributions in the screws (see featured image above. Credit: Fraunhofer)
Their results show that microstructure is “the deciding factor—if the tiny grains that make up the substance bond incorrectly during manufacture, small cracks develop, which can later cause the material to fail,” according to the release. (The press release does not specify materials or composition families.)
Design and production factors contribute also to load-bearing capacity. Any number of flaws introduced during the threading step can reduce strength. Christof Koplin, one of the investigators from the Fraunhofer Institute for Mechanics and Materials IVWM, says in the release that by optimizing design, “we were able to significantly reduce the range of the distribution curve and thus raise the stress resistance of the screws.” Lab testing ceramic screws made with optimized designs, the team found the load-bearing capacities exceeded comparable steel components by 30–35 percent.
Although fabrication details used for this work are skimpy, it seems like a natural fit for additive manufacturing. For example, young startup company Lithoz (Vienna, Austria) specializes in lithography-based ceramic component manufacturing. The company uses light to activate a photosensitive monomer binder that adds ceramic layers from ceramic slurry according to a prescribed pattern (see video above). No tooling!
Lithoz manufactures the lithography machines and ceramic slurries, which are mostly alumina, zirconia, and tricalcium phosphate.
Johannes Homa, Lithoz founder and CEO, said in an interview when I met him at ICACC in January, “There are three areas where our process is valuable: prototypes; small scale series up to 1,000 parts for advanced product development and iterations; and highly complex parts.” Images from the company website (right) show some of the shape intricacy that is achievable with the process, including a selection of ceramic screws.
Homa says the process allows for very good control of layer thickness, which ranges from 25–100 microns. The Lithoz system can build up to 100 layers per hour. According to Homa, high performance parts require high density in addition to high strength, and the process yields finished parts that are more than 99% of theoretical density. When asked about firing shrinkage, he said, “We see no warpage. There are no density gradients in the green parts, therefore, shrinkage is well understood.”
Both Ceramco and Lithoz are participating in the Ceramics Expo trade show for ceramic and glass manufacturers, April 28–30, 2015, in Cleveland, Ohio.
Author
Eileen De Guire
CTT Categories
- Manufacturing