[Image above] Credit: Jim Ross, NASA photo
Imagine being able to fly from New York to Los Angeles in one hour or from Tokyo to London in two. With speeds of Mach 5, which is equal to 1 mile per second (6,200 km/hr), hypersonic aircraft have the potential to realize these fantastic trips.
But traveling at these speeds creates very high and rapidly changing temperatures which, in turn, present significant materials challenges that are yet to be overcome.
Scientists developed ultra-high temperature ceramics (UHTCs) that can withstand temperatures of over 2,000˚C, which means they have the potential to be used on some of the hottest portions of the hypersonic aircraft. Unfortunately, the brittleness of these materials reduces their resistance to thermal shock, i.e., the stresses of rapidly changing temperatures.
Researchers turned toward using fiber reinforced UHT ceramic matrix composites (UHTCMCs) to improve the toughness, with a 30-fold increase in research output over the past decade. A recent open-access review article published in International Journal of Ceramic Engineering and Science (IJCES) discusses the progress and challenges in this most interesting field.
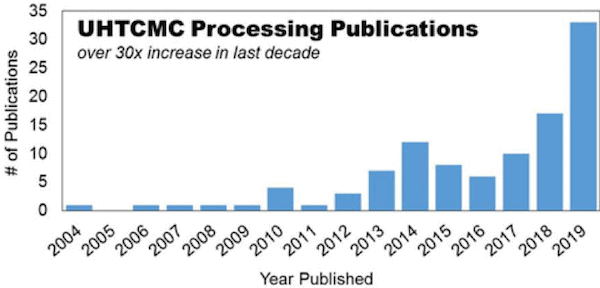
Before I delve into the specific case of UHTCMCs, I’d like to review some of the basics of mechanical testing and the associated terms.
Basics of mechanical testing
The primary test for assessing mechanical behavior is the stress-strain test, in which a sample of well-defined dimensions is stretched, compressed, twisted, or otherwise deformed with a force gauge attached to it. Force is required to pull or push the sample, for example, and that force changes according to how far it is deformed and the internal bonding within the sample. Two example types of results are shown in the figure below.
Stress is the force on the sample multiplied by a shape factor determined by the sample dimensions and the type of motion; strain is the distance traveled multiplied by a shape factor. From this data comes three significant measurements that, in combination, provide a complete picture of the mechanical behavior of a material.
In the early stages of the measurement, the stress increases in a mostly straight-line fashion. This stage of the measurement is called the elastic region. Like a stretched rubber band returns to its original shape after you release the force on it, materials will return to their original shape in this region. The modulus is determined from the slope of the curve and is the measurement of stiffness of the material. Essentially, higher slope means a stiffer material (consider steel versus copper or aluminum). In the figure, the brittle material has a higher modulus.
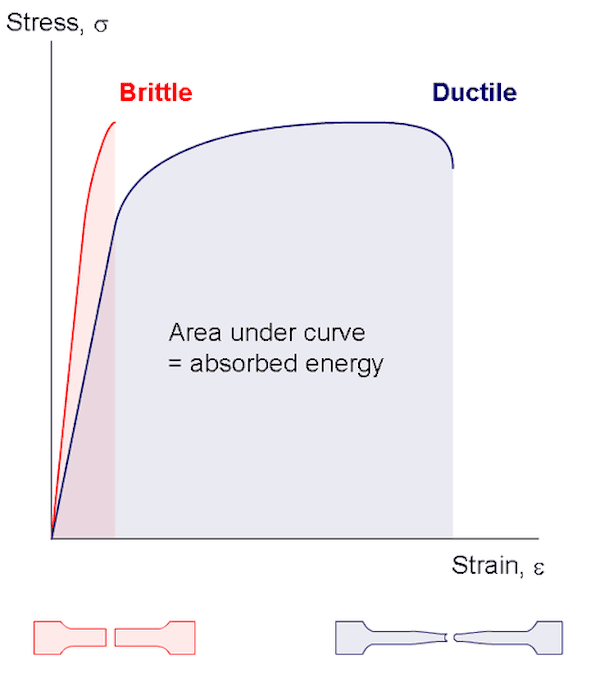
As the sample is deformed further, it goes past the point of no return after which the sample will not return to the original shape. The stress at this point defines the strength of the material—how the material behaves after this point defines whether it is brittle or ductile. Brittle materials break apart suddenly when the stress exceeds the strength. In the above figure this is seen as the curve ending for the brittle material. Ductile materials will continue deforming (strain increases), often with a significant shape change as the atoms and molecules move around to accommodate the deformation. Notice the shape of the ductile test sample in the figure. Many metals and polymers are ductile (meaning they can bend without breaking) while most ceramics are brittle.
The final measurement is toughness, which is related to the energy absorbed (area under the curve) until the sample breaks. With brittle materials, the main failure (breakage) mechanism is the growth of cracks and other flaws in the sample, which absorbs relatively little energy. The flaws are both inherent in the material (e.g. grain boundaries) and caused during sample processing (e.g. scratches, porosity).
To intensify and create reproducible flaws for toughness testing, notches are cut into samples. The toughness (K) is the stress at failure adjusted for the notch length and sample geometry according to the following equation:
KI = σ√πaβ
where σ is the stress, a is the notch length, and β is dimensionless geometry factor. KI has the measurement units MPa m½.
Where two materials have similar modulus values, the one with the higher toughness can withstand more deformation without breaking apart. See this article for more info.
UHTCMCS: Improving toughness with fibers
You may ask how adding fibers helps improve toughness. The answer is rather complicated, as is well explained in the review article “Processing of fiber‐reinforced ultra‐high temperature ceramic composites: A review.”
In some case, the fibers act as reinforcement to prevent flaws and cracks from widening or lengthening too quickly as the material is stressed. However, the reinforcement bonding cannot be too strong or the reinforcing fibers themselves could show brittle failure. The researchers describe the various ways in which this occurs, such as fiber pullout, a situation in which some of the energy is absorbed by partially breaking the bonds between the matrix and the fiber.
In other cases, the reinforcement acts to deflect cracks. This deflection allows the composite to absorb more energy by making the cracks longer before they coalesce to create the breakage points.
Fabricating UHTCMCs is as equally challenging as finding the optimal combinations of matrix and fiber materials for each application. There are so many factors to consider that listing them all would make the task seem insurmountable. A few examples include fiber format (continuous, chopped, nanoscale), matrix infiltration for uniform distribution, and densification method and conditions. And accounting for these factors must be accomplished with an eye toward reproducible and economically feasible production. I would not be able to do justice to even one of these topics here.
Fortunately, progress is being made with many techniques that show promise. Examples include the use of chopped fibers, which are less expensive than the more-traditional continuous fibers and are amenable to near-net shaping processes, for example, additive manufacturing and gel casting. Additionally, hybrid processing methods are being explored for situations in which a singular method does not provide adequate results. The researchers conclude that continued research is warranted because these products are needed to fulfill the requirements of hypersonic aircraft and other extreme temperature applications.
The open-access paper, published in International Journal of Ceramic Engineering & Science, is “Processing of fiber‐reinforced ultra‐high temperature ceramic composites: A review” (DOI: 10.1002/ces2.10033).
Author
Jonathon Foreman
CTT Categories
- Aeronautics & Space
- Basic Science
- Education
- Manufacturing