[Image above] Credit: Tom Levy
When we covered Emerging Objects’ Cool Brick—a 3-D printed ceramic brick that combats heat through evaporative cooling—back in February, it turned a lot of heads.
Now, one of its designers, University of California, Berkeley assistant professor Ronald Rael, is turning heads again with Bloom—the “first and largest powder-based 3-D printed cement structure to date.”
According to a UC Berkeley news release, Rael, head of the research team who brought Bloom to bloom, developed a new Portland cement polymer formulation free of iron oxide that was used to create the 840 custom cement blocks that make up the 9-foot-high, 12-foot by 12-foot freestanding 3-D printed structure.
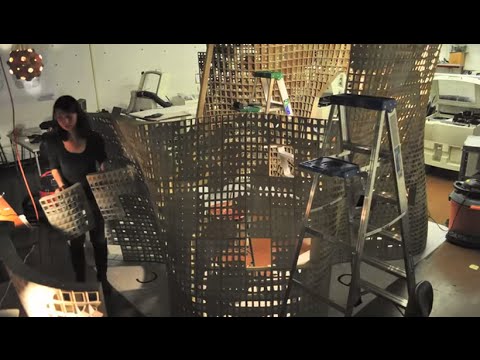
Credit: UC Berkeley Campus Life; YouTube
Unlike other 3-D-printed architectural ventures that have been limited by cost, aesthetics, and practical application, Bloom “overcomes” such limitations, say researchers. It’s also more environmentally friendly, say Rael and his Emerging Objects/Bloom collaborator Virginia San Fratello.
Each block is printed using a farm of 11 powder 3-D printers with a special cement composite formulation comprised chiefly of iron oxide-free portland cement. Iron oxide imparts a gray color to cement, and its removal makes this print much lighter. Also, 3-D printed cement requires no formwork and produces no waste and the support material can be reused to produce more blocks. Coupled with portland cement is an ecologically derived UV resistant polymer that reduces the greenhouse gas emissions from production of resins by 50% over conventional petroleum based epoxies that uses plant-based materials that do not compete with food sources or displace food-based agriculture. Each 3-D printed block is enumerated to designate the blocks position in the overall structure. Rather than a set of blueprints, a spreadsheet that demonstrated the position of a block, was used in constructing Bloom, and each block is assembled and held in place using stainless steel hardware.
Like its Cool Brick counterpart, though, the custom cement construction owes much of its inspiration to the past.
Each block has a printed structural grid that defines the interior of the tempietto and requires no additional structural support, functioning as a load-bearing 3-D printed enclosure. The curvilinear shape gives added stiffness to the thin, lightweight structure, informed by the thin masonry structures of Uruguayan architect and engineer, Eladio Dieste, particularly Iglesia Cristo Obrero, Jefferson’s serpentine brick walls at the University of Virginia, and Torqued Elipse, by Richard Serra, which inspires its form.
In plan, Bloom is a curved cruciform shape that rises 9 feet to meet the same shape rotated 45 degrees, creating a torqued “x” shape with an entrance 45 degrees off of the structures axis. The undulated form and spaces recalls an elephants foot or, when coupled with the flower pattern on the surface, the traditional mud houses of the Tiebele people in Ghana—a reference to the earliest inspirations for 3-D printing by Emerging Objects.
“While there are a handful of people currently experimenting with printing 3-D architecture, only a few are looking at 3-D printing with cement-based materials, and all are extruding wet cement through a nozzle to produce rough panels,” Rael says in the news release. “We are mixing polymers with cement and fibers to produce very strong, lightweight, high-resolution parts on readily available equipment; it’s a very precise, yet frugal technique. This project is the genesis of a realistic, marketable process with the potential to transform the way we think about building a structure.”
Bloom, unveiled at UC Berkeley, will be shipped to Thailand’s Siam Research and Innovation Co. Ltd. (the R&D arm of Siam Cement Group), which helped fund the research project, where it will be displayed before making its way around the world.
Author
Jessica McMathis
CTT Categories
- Cement
- Construction
- Environment
Spotlight Categories
- Member Highlights