If you watched the Olympics over the past few weeks, one of the recurring advertisements was for a luxury car (Cadillac or Lexus, I believe) that featured the car’s heads-up night vision system. I’ve always thought that night vision/thermal camera systems were a nifty idea—especially after experiencing some frighteningly foggy days—but, the truth is that such an option would not be extremely high on my list of desired accessories if I were in the market for a new car.
One factor is that, because these systems have solely been offered on high-priced vehicles, I have tended to assume, I think correctly, that these systems are very pricey. Although the systems have been offered on some vehicles since 2000, carmakers have been ambivalent about whether consumers wanted to pay for these systems and have acknowledged in years past that price has been a factor.
In 2005, discussion began about forming a European consortium project to develop a low-cost effective automotive far infrared camera for driver-vision applications. According to a story from that year on the Optics.org website, one project’s target was going to be the creation of an FIR microbolometer detector. At that point, one of the consortium members, Umicore, said it had developed a process for a chalcogenide glass that could be directly molded into a final lens shape as an alternative to grinding, polishing or diamond turning lenses for the microbolometer. (Previously, the materials of choice were crystalline materials, such as germanium, zinc selenide or zinc sulfide.)
However, it looks as though the project and funding (three years) didn’t come together until 2008 when the Infrared Imaging Components for Use in Automotive Safety Applications (ICU) was formed (pdf). It’s not clear to me what the status of the ICU is now, and the most recent information on the project’s website is dated 2010 (when the funding would have run out). They did, however, produce this video about the technology:
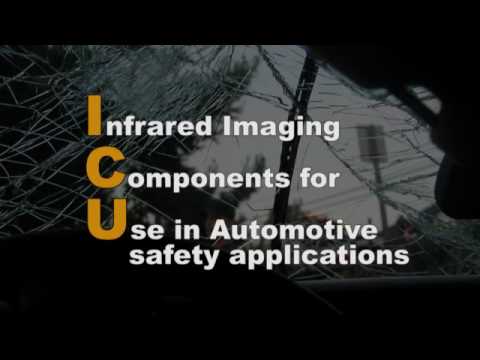
Credit: B-Phot Brussels Photonics; YouTube
None of Germany’s Fraunhofer institutes were a part of the ICU group, however the Fraunhofer Institute for Mechanics of Materials stuck to the goal of developing low-cost chalcogenide glass-based IR lenses and now the institute says it has pretty much perfected the technology and cut costs 70 percent.
In a new press release from Fraunhofer IWM, one of the scientists working on lenses, Helen Müller, says, “Instead of crystalline materials, we use the amorphous chalcogenide glass. Its softening temperature—that is, the temperature at which it can be formed—is low. Therefore, we can form it using non-isothermic hot stamping.” The institute already has a reputation for developing processes to mold high-quality glass surfaces.
Müller likens the new process of making the lenses to making waffles, with the chalcogenide glass being placed between two pressing tools. These tools are heated and, after a few minutes, cooled to below the softening temperature. The shape of the press surfaces determines the final lens configuration. The researchers assert that no additional processing is needed to get an optical imaging quality equal to polished crystal.
Fraunhofer IWM says the next steps involve tweaking the process so that it can be adapted to cost-effective mass production.
The institute also has in mind markets beyond the auto industry. If the production can be scaled up and the total price driven down, Fraunhofer IWM projects that the technology could be used for such things as monitoring the movements of health-fragile populations (e.g., older people in danger of falling or being too sedentary), monitoring industrial production (by tracking manufacturing temperatures and employee heat exposure) and continuous energy auditing of buildings.
CTT Categories
- Basic Science
- Electronics
- Glass
- Manufacturing
- Optics