[Image above] Vickers indents produced in caesium‐aluminoborate glass at 490 N (50 kgf). The indent does not show any sign of radial cracking. Credit: Januchta et al., Advanced Science (CC BY 4.0)
From windows to tableware to fiber optics, oxide glasses are everywhere you look.
Oxide glasses (typically silica) are used frequently in modern day technologies because they have numerous desirable properties, including high transparency and low thermal conductivity. Despite their ubiquity, however, oxide glasses have one conspicuous shortcoming—they are brittle.
When an oxide glass experiences surface damage, tensile stresses gather at the tips of the flaw. Once the gathered stress reaches some critical intensity, brittle fracture occurs and cracks propagate throughout the glass.
To reduce brittleness, scientists have attempted several post-processing methods, including thermal tempering, chemical strengthening, and crack-sealing particle inclusion. These methods aim to increase the critical stress necessary for crack initiation and slow the rate of crack growth by counteracting stresses acting on the crack tip.
While these methods do overcome some limitations of brittleness, post-processing steps can increase production costs significantly. Instead of post-processing, another more economical way that scientists are investigating to reduce brittleness is to create intrinsically ductile glasses.
At this point, creating truly ductile glasses is still out of reach. However, creating microductile glasses, or glasses that deform under sharp contact without cracking, is achievable.
Microductile glasses typically overcome the limitations of brittleness by deforming via densification. Densification is a type of plastic deformation in which an area is compressed under applied pressure. Unlike shear (plastic) flow, which is another type of plastic deformation, densification does not conserve volume.
Scientists create microductile glasses by tuning a glass’s network structure to promote densification. Several recent studies have designed microductile silicon oxycarbide, lithium aluminoborate, and binary aluminosilicate glasses. In new research published last Wednesday in Advanced Science, researchers created yet another microductile glass—one with crack resistance more than ten times higher than previous glasses!
This latest study’s researchers come from Aalborg University in Denmark, Technical University of Denmark, and University of California, Los Angeles. The oxide glass they created, caesium aluminoborate, has shown fairly decent crack resistance in previous work. What pushed their glass to strikingly high crack resistance levels in the new study was a counterintuitive trick—the researchers aged the glass in a humid atmosphere.
Usually a material becomes more brittle with chemical aging. But in the case of caesium aluminoborate glass, the researchers discovered aging actually decreased the glass’s susceptibility to cracking.
“Vickers indents at loads as high as 490 N (50 kgf) can be generated by subjecting the caesium glass surface to humid aging, whereas only around 30 N loading was possible in freshly polished samples of the same composition reported elsewhere,” the researchers report in the paper.
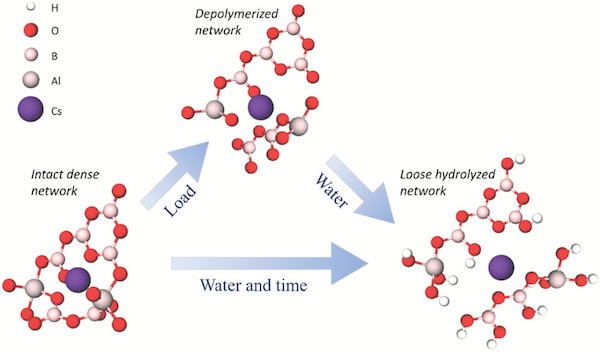
Proposed molecular-scale deformation mechanism for volume recovery and ultra-high crack resistance. When a load is applied, movement of atoms leads to breakage of network bonds; nonbridging oxygen atoms form with both caesium and aluminum cations. The deformed structure is more vulnerable to water attack, leading to absorption and penetration of hydrous species that cause volume expansion of the network. Expansion leads to the observed macroscopic volume recovery of the indent and could lead to compressive stresses in the contact area, thus counteracting crack initiation.Credit: Januchta et al., Advanced Science (CC BY 4.0)
In an email, ACerS member and Aalborg University professor of chemistry Morten Smedskjaer explains they came up with the idea to age the glass during a previous study.
“We normally quantify the densification contribution to indentation by annealing indents below Tg and look at the indent volume changes after annealing,” he says. “However, we were having problems to do this for the caesium aluminoborate glass, because its indent volume was changing over time under ambient conditions, i.e., not only due to annealing.”
“We had not seen this effect previously, which was caused by the aging in ambient air, so this is how we got interested in the effect of aging on indentation deformation and cracking,” he adds.
In the study, the researchers explain that aging the caesium aluminoborate glass in ambient air causes the glass to become hydrated (water vapor enters the glass’s structure). The reason why hydration so significantly increases the glass’s crack resistance, though, is not certain.
“We have some discussion about possible reasons in the new paper,” Smedskjaer says. These possible reasons include:
- Compressive stresses arising due to volume expansion created by hydration,
- Water promoting stress relaxation (as has been found in other studies), and
- OH-groups in the surface making the glass network very flexible.
There are other possibilities as well, and the researchers plan to conduct more studies to work out the details and to see if hydration has a similar effect on other glass compositions.
The researchers do note one limitation to caesium aluminoborate glasses—low chemical durability.
Presumably, the glass’s low chemical durability helps speed up the aging process by allowing water to enter the structure more easily. Unfortunately, low chemical durability also means the glass faces a significant disadvantage in most industrial applications. However, “Such applications might be enabled by coating the glass surface following hydration,” the researchers suggest.
The open-access paper, published in Advanced Science, is “Breaking the limit of micro-ductility in oxide glasses” (DOI: 10.1002/advs.201901281).
Author
Lisa McDonald
CTT Categories
- Basic Science
- Glass