[Image above] Credit: Pikist
Ever hear the expression “I have forgotten more than you know?” That expression aptly describes the history of handmade pottery.
The use of pottery can be traced back to some of man’s earliest recorded history, including 30,000-year-old figurines containing clay and crushed mammoth bones found in eastern Europe. In Japan, craftsmen were producing decorated ceramic containers for food preparation around 13,000 years ago, and some containers are even older.
Recipes for historic pottery were passed down from generation to generation. Firing and other processing conditions relied on the senses and experiences of the masters that could in no way be captured, even when records were kept. It is no wonder some of the beauty and utility of historic pottery is difficult to replicate today, even by our most skilled artisans and engineers.
As archeologists find more artifacts, archeometrists seek to unlock the secrets of ancient civilizations and their engineers and artisans. But how can these scientists uncover key mechanical and chemical information from such priceless, irreplaceable items? How can they figure out how they were produced? Examining shards is helpful when the tests can be destructive, but it only goes so far. Instead, scientists use models to estimate and attempt to reproduce such items.
The word “model” conjures up many images. There are runway models, model homes, model cars, and car models. Models are representations or examples of physical objects and processes, and they are often “ideal” (runway models) or simplified representations (moving models of the solar system).
In science we use many types of models. Two recent open-access articles in International Journal of Ceramic Engineering & Science discuss models that were used to better understand ceramics from different parts of the world designed for very different purposes: commerce and decoration.
Amphorae: Understanding mechanical properties of standard transport containers
With the advent of regional trade, merchants needed containers in which to store and transport goods over long distances, especially by boat. And one type of ceramic container used often in antiquity for this purpose was amphorae.
Amphorae are bullet-shaped vessels, typically with long necks and handles that are affixed near the mouth of the vessel on one end and attached to the body at the other. They are specifically designed to be stacked inside cargo holds of ships in multiple layers.
While the amphorae itself had some value, the real value lay in the vessel’s contents. As such, if the container broke and the contents of that vessel were lost—and potentially damaged other goods in the cargo hold as well—it could result in substantial losses to the producer and the ship owner.
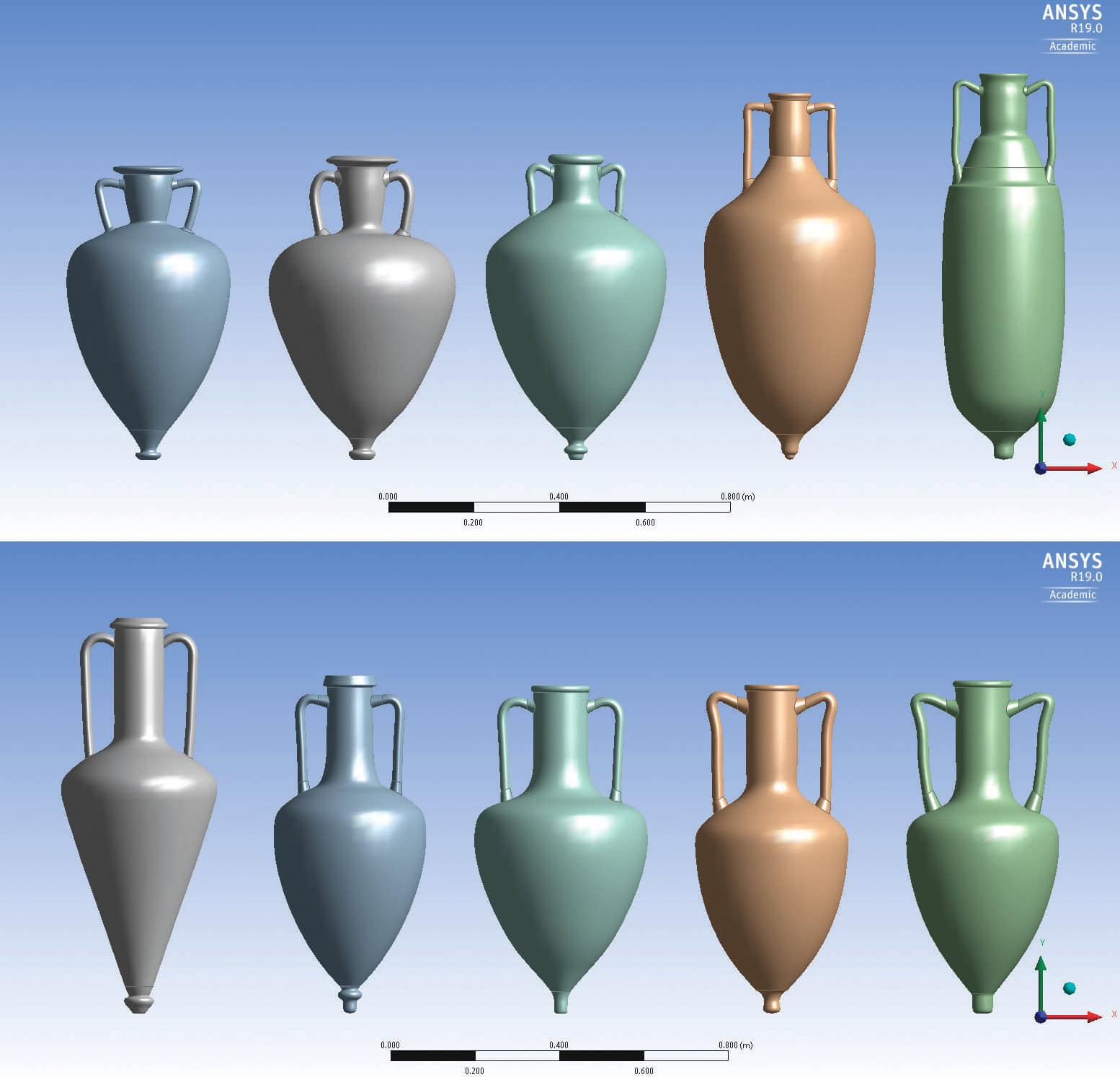
3D models of amphorae from Kos (top) and Rhodes (bottom). Credit: Hein and Kilikoglou, International Journal of Ceramic Engineering & Science (CC BY 4.0)
In the recent open-access paper “Digital modeling of function and performance of transport amphorae,” Anno Hein and Vassilis Kilikoglou from the Institute of Nanoscience and Nanotechnology in Greece assessed specific design features of different amphorae for their performance (e.g., failure potential), particularly during transport. Furthermore, they used simulations to provide information to help interpret typical damages observed in archaeological finds.
The authors could not use destructive methods of testing on the vessels, for obvious reasons. Instead, they ran nondestructive testing such as X-ray tomography to determine wall thicknesses while performing mechanical testing on shards to get insights into mechanical strength, tangent moduli, and plastic deformation.
They used the limited experimental information as inputs and boundary conditions for finite element modeling of the stresses that build up at the contact points of the amphorae due to static vertical loading (e.g., the weight of one layer on the next), dynamic vertical loads (ships travel over waves), and dynamic horizontal loads (ships rocking side-to-side).
For those who may not be familiar with finite element modeling, an object is subdivided into small pieces (or elements) and each element is “analyzed” both separately and as constrained by adjacent elements. This article does an excellent job of describing the modeling process.
The results of the modeling include compressive and tensile stresses on the exterior and interior walls of the amphorae. Excessive compressive loads are found, but the authors surmise these loads result in elasto-plastic deformation, which is not catastrophic. Tensile stresses on the outer surfaces, on the other hand, can lead to crack initiation and eventual failure. Failed amphorae artifacts show damage in the areas predicted by the modeling.
The open-access paper, published in International Journal of Ceramic Engineering & Science, is “Digital modeling of function and performance of transport amphorae” (DOI: 10.1002/ces2.10056).
Ru celadon: Investigating the coloring of a masterwork of Chinese ceramics
Celadon is a pottery term that refers to both a transparent, greenish glaze and the wares to which the glaze is applied. Though the term is purely European, celadon originated in China, and today notable kilns such as the Longquan kiln in Zhejiang province are renowned for their celadon glazes.
Celadons come mostly in some shade of green, but shades of pale blue—notably Ru celadon—are highly valued, and in historical times were reserved more or less exclusively for use in the Chinese Imperial court.
In the second open-access paper, “Analysis of structural effects on coloring mechanism of Ru celadon porcelain,” Yen‐Yu Chen (Chinese Culture University) and Yi‐Wun Bai and Wen‐Cheng J. Wei (National Taiwan University) investigate methods to reproduce the unique color and milky opalescence of ancient Ru celadon glazed ceramics.
The color of celadon is generated by two mechanisms: chemical coloring by iron species in calcium aluminosilicate compositions; and structural coloring by inhomogeneities, specifically crystallites and voids in the celadon glass. While there is some information available about the material composition of ancient celadon—both from analysis of ancient shards and from prior studies—the fabrication methods are not well understood. For example, it is believed the porcelain was fired in a reducing environment, but there is no way of knowing the composition of the gases or their temperature—the technology simply did not exist for those measurements 1,000 years ago.
In this article, the authors created their own celadon by varying a range of experimental conditions, including composition relative to phase stability data for the complex chemical system and firing temperatures, environments, and holding times. They measured the model systems they created against a shard of ancient celadon ceramic for color, microstructure, and chemical content of the glass and crystallites.
In the end they came close to the ancient celadon color and opalescence, giving insight into ancient firing protocols. Their work supports the combination of the chemical coloring and structural coloring mechanisms. Specifically, the dual-phase nature of the glass contributes to Rayleigh scattering while crystallites and voids contribute to the “milky” color, while the ratio of Fe2+ and Fe3+ oxidation states of iron contribute to chemical coloration.
The open-access paper, published in International Journal of Ceramic Engineering & Science, is “Analysis of structural effects on coloring mechanism of Ru celadon porcelain” (DOI: 10.1002/ces2.10058).
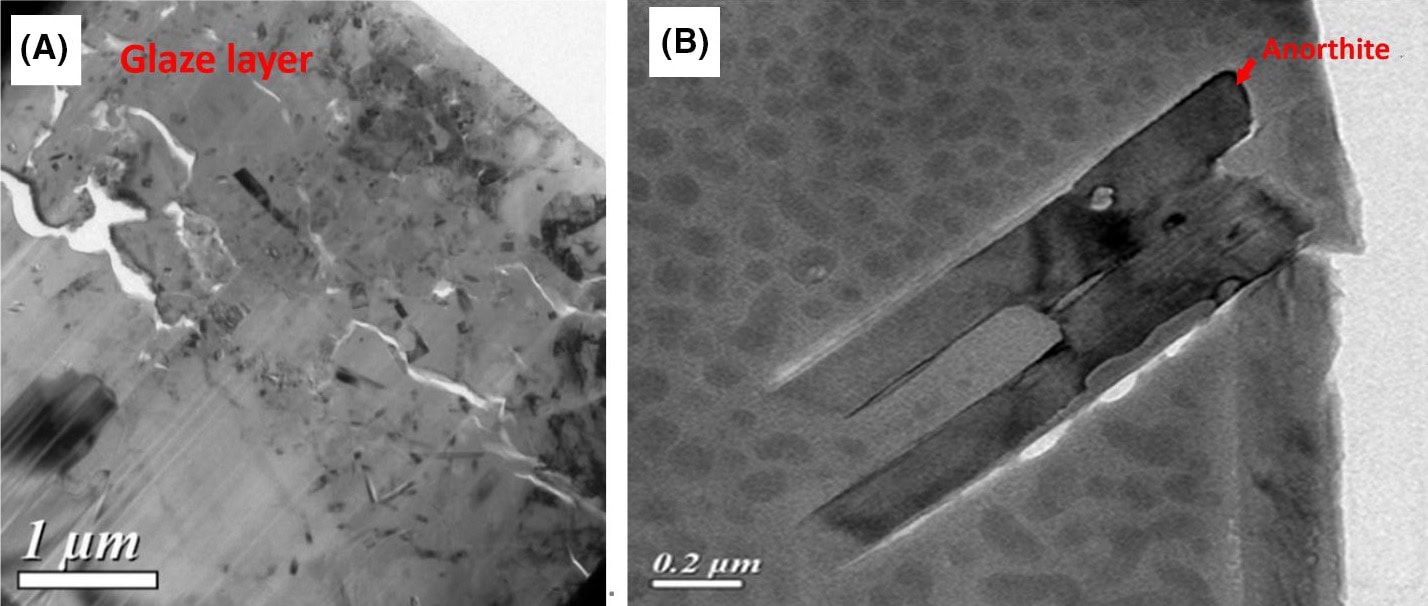
TEM micrographs of the shard of Ru celadon porcelain, including (A) the glaze layer of Ru celadon porcelain, and (B) anorthite surrounded by the dual‐phasic glass matrix. Credit: Chen, Bai, and Wei; International Journal of Ceramic Engineering & Science (CC BY 4.0)
These examples of modeling in ceramics are but two of many different modeling techniques. Some models predict behaviors on first principles (electronic and atomic behaviors) while some explore how microstructure can be manipulated to produce desired outcomes.
Regardless of the specific model used, researchers working on predictive models have a substantial need for data for testing, verification, and adjustment. ACerS supports open science and open data to enable researchers to build from the work of other researchers in more substantive ways.
Author
Jonathon Foreman
CTT Categories
- Art & Archaeology
- Modeling & Simulation