[Image above] Researchers from two Polish universities tested three types of ceramic waste as concrete aggregate, and found sanitary ware outperformed even traditional aggregate materials. From top: sanitary ware ceramic, red ceramic, and tiling (glazed) ceramic. Credit: Przemysław Brzyski, Materials 2018, 11(2), 2565
If you saw the live-action Cat in the Hat movie with Mike Myers, one of the most memorable scenes is when he tests out the Kupcake-Inator, a device that can make cupcakes out of anything: hot dogs, ketchup, even a fire extinguisher. While the absurdity of making cupcakes out of wildly inappropriate materials makes for a good laugh in this case, not all recipes adhere to such “concrete” guidelines of what is considered an appropriate ingredient.
Especially if your recipe is for actual concrete.
Concrete is a composite material made of aggregates bound together with cement. While the list of materials used for making cement is pretty standard—mainly limestone and clay—the materials used for aggregates can vary immensely—especially in recent years.
Each year, more than 4 billion tons of cement are produced, accounting for around 8 percent of global CO2 emissions. The Global Cement and Concrete Association, whose members own about 30 percent of the world’s total cement production capacity, launched in January 2018 to address this pollution and drive advances in sustainable construction.
One tactic the concrete industry employs to advance sustainable construction is reusing waste for aggregates. Traditionally, aggregates are made from materials like crushed stone and sand extracted from larger rock formations. Extracting material for aggregates, though, causes significant impact and damage to the environment. Instead, construction companies are turning to materials already at hand that can be crushed and used in lieu of extracted materials.
Two well-known examples of recycled material used in aggregates are slag, a byproduct of iron and steel production, and fly ash, a byproduct of coal combustion (because of its pozzolanic properties, fly ash is also used in the cement phase). But researchers have been hard at work to identify additional recyclable byproducts, such as sewage sludge.
One area of much research is use of ceramic waste as aggregates. Researchers have looked at the utility of red ceramics, like brick, and white ceramics, like sanitary ware.
When testing concretes based on ceramic waste aggregates, it is not enough to measure strength and density in the lab. To understand how these concretes would hold up in real life, they need to be put through aggressive chemical environments that occur in industrial applications, like pipes for municipal sewage.
Researchers from Siedlce University of Natural Sciences and Humanities and Lublin University of Technology published an article on ceramic-waste-based aggregates, with a particular focus on ceramic waste obtained from sanitary ware products. “The aim of the research was to select specific types of ceramic construction waste (from three different kinds of ceramic products) … and evaluate the effect of modification of aggregate composition on the concretes resistance to aggressive environment,” the researchers write in the paper.
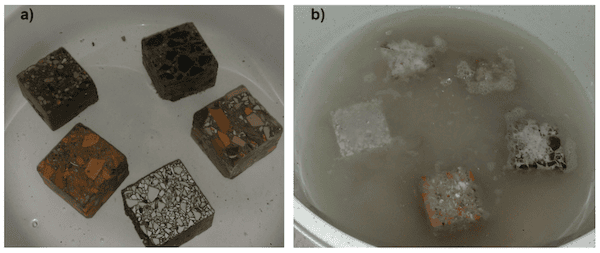
Concrete samples were placed in both a) water and b) an aggressive chemical solution to compare how each faired over a course of 240 days. Credit: Przemysław Brzyski, Materials 2018, 11(2), 2565
The researchers collected ceramic waste materials from landfills and split the waste into three groups: red ceramics, glazed ceramics, and sanitary ware ceramics. The ceramics were crushed and made into concrete using concrete recipe C35/45 as reference. The researchers then placed samples in an aggressive chemical solution consisting of hydronium ions, sulfate ions, ammonium ions, and magnesium ions. Compressive strength was tested after 40 days of immersion, and mass was measured at regular intervals over 240 days in solution.
The researchers found aggregates made of ceramic waste presented relatively lower apparent density than traditional aggregates made of gravel and basalt, but displayed higher absorptivity. Specifically, sanitary ware ceramic concrete displayed greater flexural and compressive strength than basalt-based concrete, while glazed ceramic concrete showed similar strength properties to gravel-based concrete. The red ceramic concrete was weakest of all concretes in the study.
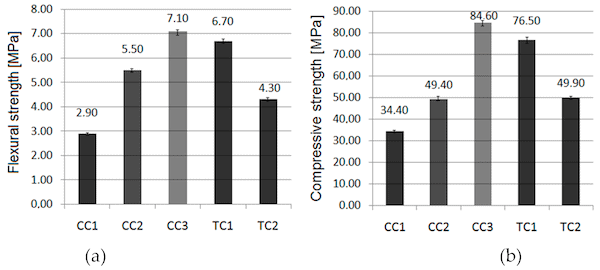
Concrete samples were placed in both a) water and b) an aggressive chemical solution to compare how each faired over a course of 240 days. Credit: Przemysław Brzyski, Materials 2018, 11(2), 2565
When the ceramic-based concretes were exposed to aggressive chemical environments, sanitary ware ceramic concrete demonstrated both the lowest drop in compressive strength (13.4 percent) and smallest weight loss (20.2 percent). These losses were both lower than what traditional basalt-based concrete experienced—a 27.8 percent drop in compressive strength, and a 57.9 percent loss in mass.
“The use of sanitary ceramic cullet as aggregate is the most advantageous in the production of the concrete resistant to aggressive environments and is recommended for the production of concrete sewage pipes,” say the researchers in the paper.
I find the results poetic in a way. If this suggestion is implemented, not only would sanitary ware begin the sewage transportation process as toilets in the bathroom, sanitary ware would then help transport that sewage all the way to proper disposal.
The open-access paper, published in Materials, is “Analysis of the effects of aggressive environments simulating municipal sewage on recycled concretes based on selected ceramic waste” (DOI: 10.3390/ma11122565).
Author
Lisa McDonald
CTT Categories
- Cement
- Environment