[Image above] Léa Rouquette, Ph.D. student in chemistry and chemical engineering at Chalmers University of Technology, demonstrates a new hydrometallurgy recycling method based on oxalic acid. Credit: Henrik Sandsjö, Chalmers University of Technology
As more and more lithium-ion batteries are produced to keep up with the demand for electric vehicles and renewable energy technologies, the question of what to do once these millions of batteries expire becomes an increasingly urgent situation.
Considering the difficulties associated with securing and ethically sourcing the raw ingredients for lithium-ion batteries, as discussed in the August 2023 Bulletin, recycling lithium-ion batteries is the ideal solution.
There a growing number of recycling companies, such as Li-Cycle and Redwood Materials, that offer an alternative to the landfill for lithium-ion batteries. In addition, other companies are forming partnerships to produce lithium-ion batteries with recycled materials.
Governmental bodies also play a role in driving the material recovery market. For instance, in June 2023, the U.S. Department of Energy announced $192 million in new funding to advance battery recycling technologies. Meanwhile, in July 2023, the European Council adopted a new regulation that sets a target for lithium recovery from waste batteries of 80% by the end of 2031.
Despite this interest in recycling lithium-ion batteries, recycling batteries is not easy because they “are really not designed to be recycled,” says Dana Thompson, previously materials science Ph.D. candidate at the University of Leicester and now battery cell developer at Jaguar Land Rover, in a Science article.
Currently, recyclers use two main techniques to recover metals from the battery cathode:
- Hydrometallurgy. This process relies on aqueous solutions to extract and separate metals. It has higher recovery rates and lower energy consumption than other methods, but it can be more complex and chemically intensive. Toxic inorganic acids, such as sulfuric acid, are typically used, producing problematic wastewater and harmful emissions, such as SO3, Cl2, and NOx.
- Pyrometallurgy. This process uses high-temperature techniques such as pyrolysis, roasting, or melting to recover metals from the cathode. Temperatures ranging from 800–1,200℃ are typically required. Other disadvantages include low lithium recovery rates and the production of harmful emissions, such as carbon monoxide, volatile organic compounds, and dust.
Direct recycling, which recovers battery components directly without breaking down the chemical structure, is an ideal approach to battery recycling. But to realize direct recycling, batterymakers, recyclers, and researchers would need to address a host of issues. For example, manufacturers would need to label their batteries so recyclers know what kind of cell they are dealing with.
It is evident that more environmentally friendly recycling methods are needed to make the lithium-ion battery market into a sustainable and (ideally) circular economy. The two studies described below demonstrate some ways to accomplish this goal.
Just add water: Water-based recovery process for anode scraps
In an April 2023 paper, researchers at Oak Ridge National Laboratory and Argonne National Laboratory described a simple yet efficient water-based recovery process for battery anode scraps.
A typical lithium-ion battery anode consists of graphite, conductive carbon, and a binder material (such as polyvinylidene difluoride or styrene-butadiene rubber) coated onto a current collector, typically copper foil.
Current recycling methods use either hazardous solvents or high temperatures to dissolve/remove the binder, which can result in the release of toxic gases.
“Therefore, it is important to develop a highly efficient, cost-effective, and environmentally friendly process to directly recycle anode scraps and reintegrate the recovered materials into the battery supply chain,” the researchers write in the paper.
In the recent study, they showed that simply immersing the anode in deionized water completely delaminated the anode films from the copper foils without damaging any components. The recovered films could then be directly reprocessed into slurry and recast as new anodes because the films’ composition was not altered. Testing confirmed that the new anode exhibited electrochemical performance on par with that of the original anode.
The water-based recovery process could take place over a wide temperature range, from room temperature (20°C) up to the boiling point of water (100°C). The higher the temperature, the less time it took for complete delamination. For example, delamination took about 4 minutes at 20°C but only 10 seconds at 100°C.
“This environmentally benign and cost-effective separation technique not only presents a closed-loop recycling approach but also provides a new pathway for battery manufacturers to recycle their electrode scraps safely and effectively on-site,” the researchers conclude.
The paper, published in Sustainable Materials and Technologies, is “Direct recycling and remanufacturing of anode scraps” (DOI: 10.1016/j.susmat.2022.e00542).
Hydrometallurgy goes green: Oxalic acid shows potential as leaching agent
In a September 2023 open-access paper, researchers at Chalmers University of Technology in Sweden described a new hydrometallurgy process that uses oxalic acid as a leaching agent to achieve selective separation during battery recycling.
As noted earlier, toxic inorganic acids are typically used in hydrometallurgy processes. However, oxalic acid is an organic acid found in many plants. Not only is oxalic acid considered more environmentally friendly than inorganic acids, but it also has a high potential for industrialization.
Several previous studies, such as here and here, investigated the use of oxalic acid as a leaching agent. These studies confirmed its potential to effectively recover various battery metals. But the effect of oxalic acid on aluminum—a difficult metal to remove using the traditional, inorganic acid-based hydrometallurgy route—was not reported.
In the new study, the Chalmers researchers dismantled spent lithium-ion batteries provided by Volvo Cars AB. The nickel–manganese–cobalt cells were then crushed, mechanically sieved, and magnetically separated at temperatures below 50°C to obtain a “black mass,” or a shiny, metallic mixture containing all the valuable metals from the battery.
During the subsequent leaching process, the oxalic acid reacted with lithium, nickel, manganese, and cobalt oxide to form simple oxalate compounds. Aluminum, on the other hand, formed complex oxalate compounds.
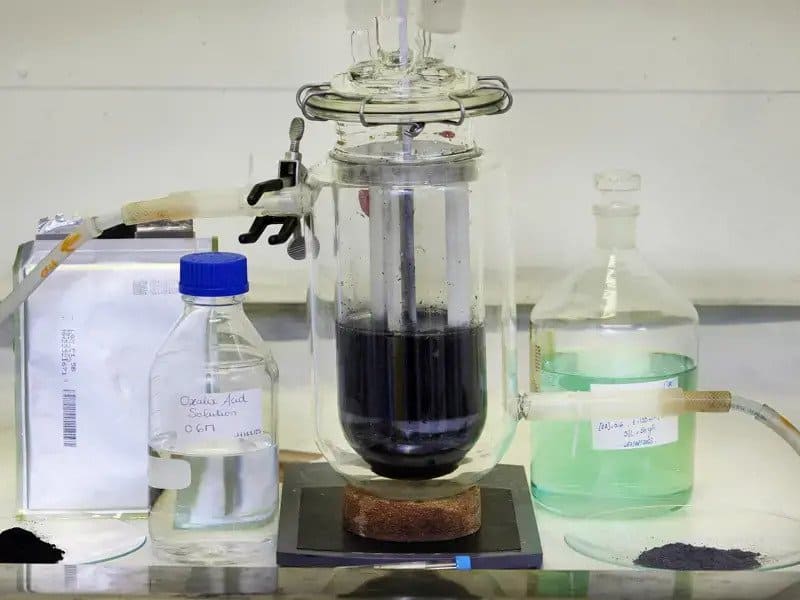
Setup for the new hydrometallurgy battery recycling process. The crushed contents of a spent car battery cell (silver bag), in the form of a finely ground black powder (dish on the left), are dissolved in oxalic acid (transparent liquid). After a set time, the black mixture is filtered. The aluminum and lithium end up in the greenish-blue liquid, while the other metals, such as cobalt, nickel, and manganese, remain in the dark solids (dish on the right). Credit: Anna-Lena Lundqvist, Chalmers University of Technology
Only the lithium simple oxalate and aluminum complex oxalates were soluble. This property allowed them to be selectively dissolved in the leachate, while the other transition metal oxalates remained in the leaching residue.
By optimizing the processing conditions, the researchers successfully leached 98.8% of the lithium and 100% aluminum, while less than 0.5% of cobalt and nickel and 1.5% of manganese were dissolved.
With the cobalt, nickel, and manganese left behind as easily recovered solids, the next step would be to separate the aluminum and lithium in the leachate. The researchers do not believe this separation will be difficult because the metals have very different properties.
The researchers emphasize that the complete leaching of aluminum is a phenomenon not reported previously in the literature. For this reason, their method “can offer the recycling industry new alternatives and help solve problems that hinder development,” says Martina Petranikova, associate professor of chemistry and chemical engineering at Chalmers, in a Chalmers press release.
The open-access paper, published in Separation and Purification Technology, is “Complete and selective recovery of lithium from EV lithium-ion batteries: Modeling and optimization using oxalic acid as a leaching agent” (DOI: 10.1016/j.seppur.2023.124143).
Author
Laurel Sheppard
CTT Categories
- Energy
- Environment