[Image above] Cracked screens are the bane of every smartphone user—could sol-gel coatings help strengthen display glass? Credit: Pixabay
We all know the properties of glass: hard, brittle, and easily broken. And ever since the invention of glass some 5,000 years ago, people have been trying to overcome these properties and make glass stronger. There have been some successes, notably the invention of Gorilla Glass (by Corning) in the 2000s, a finding which revolutionized cell phones and was accomplished using the method of chemical strengthening (a method first introduced in the 1960s!). And there have been some massive fails, such as the infamous Tesla Cybertruck demonstration.
But even with the great leap in strength of Gorilla Glass and similar products from Corning, AGC Inc., Schott AG, and others, display glass still cracks, and research into the strengthening of display glass is still going strong.
A recent study appearing in the April issue of International Journal of Applied Glass Science explores using sol-gel glass coatings to strengthen chemically tempered mobile phone cover glass. Sol-gel is a relatively inexpensive and easily controlled coating method, and the glass coatings are directly compatible with commercial cover glass.
The initial results from the research team led by Chenyu Li of Xiamen University make sense. A 5 µm coating cured at 80°C raised the bending strength more than a 3 µm coating cured at the same temperature did (12% versus 6%). More material means greater strength—start the engineering analysis.
But hold on. An article in the literature showed strengthening by a substantially thinner coating was on par with the result from the 5 µm coating—how can that be?
Li et al. inferred the coating in the other study had a substantially higher modulus of elasticity and higher residual stress than the 5 µm coating because it was cured at a much higher temperature (300°C). Residual stress in the coating places a compressive stress on the substrate glass, which prevents surface cracks from widening and thus increases the overall strength of the glass.
To test this hypothesis, Li et al. tested another set of samples with 3 µm coating cured at 180°C, a higher curing temperature than what was used for their original coatings but lower than the curing temperature used in the other study.
They found the elastic modulus and residual stress of the coating cured at the higher temperature were both approximately double the measurements for the coatings cured at 80°C. Yet the strength of the higher-temperature coated glass was closer to the 3 µm (80°C) coated glass than the 5 µm. This result seems to contradict the results of the other study—so what other factors are affecting the strength?
To unwind this mystery, the researchers turned to finite element modeling. Their models showed that the coating’s modulus and compressive stress values on the surface were small compared to the native values of the substrate, so small that they could not make a significant impact on strength. So the researchers began to consider another factor—crack filling.
It’s well known that longer cracks lead to lower bending strength. So it makes sense that filling cracks should therefore increase the strength. The modeling explains how this filling works. Though the residual stress has little effect at the surface of the glass, it has significant effect near the crack tip. The elevated stress acts as “closure” stress on the cracks. And the more the cracks are filled, the greater the effects.
The model shows that while the modulus of the higher-temperature cured coating increases, so does its shrinkage upon curing, which means a lower percentage of crack filling. These two factors oppose each other, resulting in a lower-than-expected strength enhancement. On the other hand, the modeling indicates the 5 µm coating has greater crack filling, which leads to substantially higher strengths even with a lower modulus.
The modeling results and interpretation are summarized very nicely in the final figure of this article.
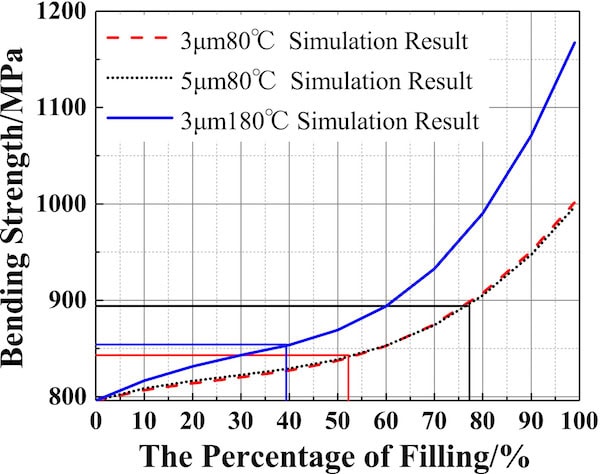
By matching the simulated and experimental data of glass bending strength, the actual filling ratios were obtained (the perpendicular lines). The filling ratios of the SiO2 coatings are 52.22% for 3 μm/80°C, 77.23% for 5 μm/80°C, and 39.37% for 3 μm/180°C. Credit: Li et al., International Journal of Applied Glass Science
In sum, the previous study’s coatings were only 0.6–0.8 µm thick and were cured at 300°C, so the major factor influencing strength in that case was the elastic modulus. But because the coatings were a lot thicker in this study and the modulus and compressive stress values compared to the substrate were negligible, crack filling had a bigger influence.
The results of the models left me wanting more. First, what could be done to confirm the modeling of the filling ratios? Can this ratio be measured directly? Can other indirect methods or models be used? If further methods were explored, how do they compare to the trends predicted by these models?
Second, the model predicts that combining higher curing temperature with a thicker coating should improve strength, though perhaps not substantially given the increased shrinkage. It would be very interesting to see the results of that experiment, as well as results of alternate experimentation aimed at attaining near 100% crack filling. I look forward to reading Li’s next paper and seeing how their research continues to improve the strengthening of glass.
Read all the great articles in IJAGS Volume 11, Issue 2.
The paper, published in International Journal of Applied Glass Science, is “Strengthening mechanism of cover glass by Sol‐Gel SiO2 coating” (DOI: 10.1111/ijag.14774).
Author
Jonathon Foreman
CTT Categories
- Basic Science
- Glass