[Image above] Scratch resistance of the surface of container glasses is one of the key challenges for the glass industry. Credit: Miss Shari, Flickr (CC BY-NC-ND 2.0)
I’ve been playing with fire ever since last summer when I got a new phone—I still haven’t put on the tempered glass screen protector. I’m one drop away from scratching or cracking the screen of a device that I paid a couple hundred dollars to own.
We often take glass for granted because, in many applications, we are looking through the glass rather than at the glass itself. It’s not until the glass suffers a scratch or crack that we become (painfully) aware of its existence.
What causes glass to scratch, though? The simple answer is hardness—anything harder than the glass can put a mark in its surface.
The mechanisms behind scratch formation in glass, however, are more complicated—partly because we don’t know much about them yet.
“…The technical knowledge pertaining to the parental scientific background behind the formation of scratches on glass surfaces in terms of structural properties is still limited,” researchers write in a recent open-access paper.
The researchers are from the University of Bayreuth in Germany and include ACerS member Stefan Schafföner. They explain that collecting more information on scratch formation mechanisms is a priority for the glass industry, as scratches in the glass surface can lead to crack formation. Soda–lime–silica glass is of particular interest because this type of glass is widely used in the container industry.
In recent years, the effect of indenter geometry and applied normal load on the plastic deformation, microcracking, and chipping of glass has gained attention in numerous studies. However, “To the best of our knowledge, there is no information available on the surface structural behavior of the silicate network in terms of an elaborate analysis of network connectivity, which is responsible for triggering the formation of a visible scratch,” the researchers write.
In their study, they looked to illustrate the structurally “weakening elements” that are responsible for formation of scratches on soda–lime–silica glass surfaces. To do so, they created samples of both untreated and heat-treated soda–lime–silica glass for the experiment.
First, they analyzed the structure of the glass samples using X-ray photoelectron spectroscopy and Raman spectroscopy. Then, they scratched the glass surfaces using a fixed high normal load of 5 N (which generates scratches in the micro-abrasive regime). Finally, they characterized the scratches using field emission scanning electron microscopy and laser scanning microscopy.
Based on the analyses, the researchers determined that the heat-treated glass was more sensitive to visible formation of scratches than the untreated glass. They suggest this vulnerability is due to the subsurface structure of heat-treated glass.
Up to a depth of about 5 nm, the heat-treated glass contains relatively lower concentrations of “mechanically weakening elements,” i.e., nonbridging oxygens and SiOH/H2O species, and a high concentration of bridging oxygens, which “indicated a strong and rigid network.” In contrast, the untreated glass has higher concentrations of nonbridging oxygens and SiOH/H2O species at that same depth, which “is accountable for its lower hardness.”
Critically, the reverse is true in the 5–100 nm region—the heat-treated glass is mechanically weaker in this “intermediate zone” due to a higher OTotal/Si ratio. However, in the bulk region of the glasses (1–5 µm, or 1,000–5,000 nm), the heat-treated glass is again stronger due to a lower variation of the bond angle in its network at this depth.
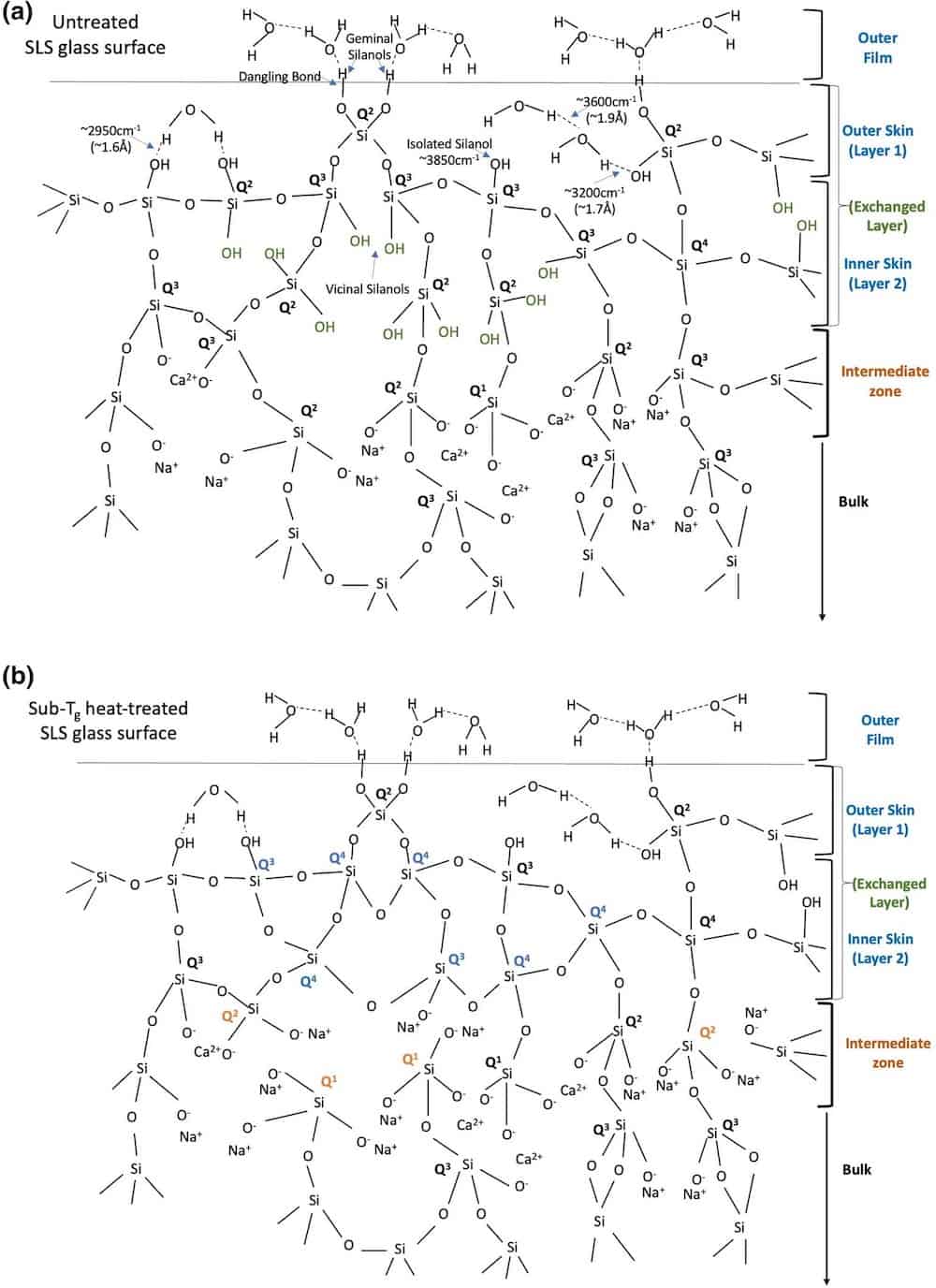
Typical surface structural schematic representations of soda–lime–silica (SLS) glass that is (a) untreated and (b) heat-treated at 510°C for 30 min. The mechanically weakening structural characteristic of the intermediate zone with respect to higher OTotal/Si ratio obtained in the heat-treated surface is critical to scratch formation. More details on this figure available here. Credit: Roy et al., Scientific Reports (CC BY 4.0)
Simply put,
- Untreated glass: weak (up to 5 nm)—strong (5 to 100 nm)—weak (1 to 5 µm)
- Heat-treated glass: strong (up to 5 nm)—weak (5 to 100 nm)—strong (1 to 5 µm)
The mechanically weaker “intermediate zone” of the heat-treated glass is what the researchers identify as a key factor in visible scratch formation.
“This depth is critical to propagation of cracks from a surface flaw during a scratching event because the size of the cavities in the vicinity of crack tips is reported to be in the same range on the order of nanometers,” they write.
So, “A weaker structural network in this region … is expected to contribute to easy propagation of a surface-initiated crack to the depth of the stronger bulk network,” they explain. “Any surface injuries will be subsequently accompanied by higher scratch depths, wear volume, and material pile up.”
The researchers are working on a new study that extends the X-ray photoelectron spectroscopy measurements for several hours—accompanied by argon etching with low-energy gas cluster ion beam—to ensure that the glass network is not affected despite prolonged exposure.
“This may give rise to the possibility to probe further into the depth of the glass network to complementarily correlate the distribution of Qn species obtained by Raman investigations in the bulk structure of the solid specimens,” they add.
They also suggest that further investigations on the effect of atomistic surface roughness and waviness on scratch formation are needed to propose a surface structural model of soda–lime–silica glass, “which could possibly further explain the parent cause of scratches induced during the handling and storage of container glass bottles in reality.”
The open-access paper, published in Scientific Reports, is “Revealing the surface structural cause of scratch formation on soda-lime-silica glass” (DOI: 10.1038/s41598-022-06649-y).
Author
Lisa McDonald
CTT Categories
- Basic Science
- Glass