[Image above] In 2016, Nissan Motor Company revealed the world’s first solid oxide fuel cell-powered prototype vehicle that runs on bioethanol electric power. Solid oxide fuel cells are expected to play a larger role in transportation and stationary power generation in the coming decade. Credit: Nissan, YouTube
Though fewer people were driving last year due to the COVID-19 pandemic, that didn’t stop the global electric car market from achieving a new milestone.
“After a decade of rapid growth, in 2020 the global electric car stock hit the 10 million mark, a 43% increase over 2019, and representing a 1% stock share,” reports the new International Energy Agency global electric vehicle outlook for 2021.
Battery electric vehicles comprise the majority of electric cars, accounting for two-thirds of new electric car registrations and two-thirds of the stock in 2020. However, batteries are not the only way to power an electric vehicle.
Fuel cells are an alternative technology being explored to power vehicles of the future. As explained in a CTT post last year, the basic setup of both fuel cells and batteries consists of two electrodes (anode and cathode) on either end and an electrolyte (liquid or solid) in between. However, while a battery’s charge and discharge system is self-contained—ions within the battery flow between the anode and cathode—a fuel cell must get its molecules from an external source.
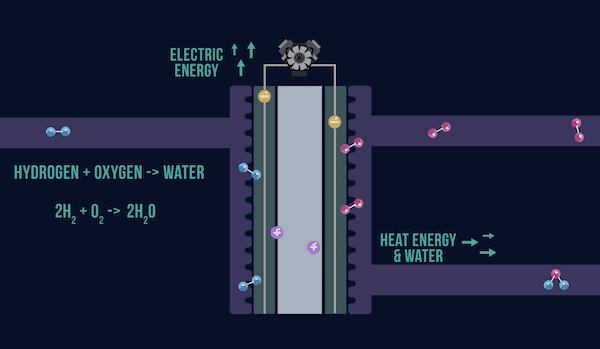
A video by the Hydrogen Hub explains the differences between batteries and fuel cells. Above is a screenshot of a basic fuel cell setup. Credit: Hydrogen Hub, YouTube
There are several different types of fuel cells, which all work in slightly different ways. Polymer electrolyte membrane fuel cells are a main choice for powering vehicles, but solid oxide fuel cells (SOFCs) have received some attention for transportation applications as well.
SOFCS use a hard, nonporous ceramic compound as the electrolyte. Compared to other fuel cells, SOFCs operate at very high temperatures—as high as 1,000°C (1,830°F)—and so are typically investigated for use in stationary power generation (though Nissan Motor Company did reveal an SOFC-powered prototype vehicle in 2016).
The high operating temperatures of SOFCs remove the need for a precious-metal catalyst, thus reducing cost. It also allows SOFCs to reform fuels internally, which allows use of a variety of fuels.
On the other hand, the high operating temperature also places stringent durability requirements on materials used in the SOFC, such as sealants.
Sealants are used to join the various components of an SOFC together, keeping them electrically separated to avoid short circuits. Sealant materials must be electrically insulating and gastight, plus chemically and mechanically compatible with the adjoining elements to avoid interactions that lead to local changes of the sealant properties, causing cracks or delamination.
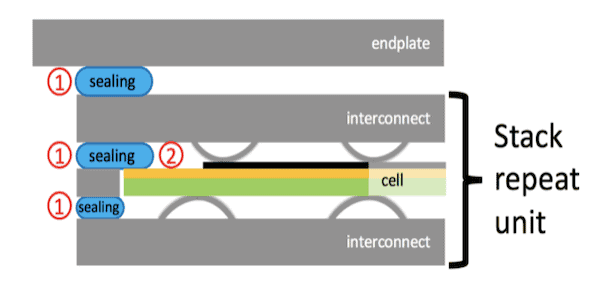
Detail of a stack scheme showing the position of sealants and its interfaces in a solid oxide fuel cell. 1) Sealing portions in contact with steel at both sides; 2) Sealing portions in contact with steel on one side and ceramic on the other side. Credit: Spotorno et al., Materials (CC BY 4.0)
Glass and glass-ceramics are of great interest as sealants in SOFCs because of their ability to achieve good adhesion to metal substrates, gas tightness, high electrical resistance, ease of fabrication and application, and competitive costs.
Two of the most important properties that drive glass and glass-ceramic composition selection are the coefficient of thermal expansion (CTE) and glass transition temperature (Tg). The CTE should be compatible with the adjoining components (i.e., interconnect and electrolyte) to avoid introducing mechanical stresses. The Tg should be close to the high operating temperature of the SOFC so the glass can soften to provide a proper seal while maintaining sufficient rigidity.
In today’s CTT, we look at several studies published this year that explore various glass sealants for use in SOFCs.
Feldspar-based glass sealant maintains voltage stability
In May, researchers from China University of Mining & Technology-Beijing and University of South Carolina investigated the potential of a feldspar-based silicate glass sealant in SOFCs.
Among various glass materials, silicate glass sealants demonstrate good potential in SOFCs due to low leaking rate and high-temperature reliability. However, the properties of silicate glass are highly dependent on the proportion of the constituent oxides, and many studies that demonstrated successful sealing performance used silicate glass with alkaline oxides.
For their study, the researchers prepared a feldspar-based silicate glass that contains around 17 wt.% alkalis (K2O and Na2O). To evaluate applicability of the seals in an SOFC, they carried out single cell testing using a NiO-yttria-stabilized-zirconia anode supported cell.
They determined that the open circuit voltage of the glass-sealed single cells stayed stable at 750°C, with no observable voltage degradation after five thermal cycles. They attribute this observation to the crack healing capability of alkaline oxide silicate glass.
“This study indicates the obtained glass composition is a reliable and self-healing glass seal for intermediate temperature SOFCs,” they conclude.
The paper, published in Ceramics International, is “Feldspar-based CaO–K2O–Na2O–BaO silicate glass sealant for solid oxide fuel cells” (DOI: 10.1016/j.ceramint.2021.02.046).
Modifiers fine-tune properties of glass sealants
To fine-tune the properties of glass sealants, researchers will add modifiers to a composition to interrupt the normal bonding between glass-forming elements and oxygen. In two studies published this July, two different research groups explored the use of mixed alkaline earth modifiers and vanadium-based compounds.
The first group consists of two researchers from Thapar Institute of Engineering and Technology in India. They note that previous studies reported alkaline earth modified glasses to be a good candidate for SOFC sealants, and they looked to expand on this research by investigating the effect of single and double alkaline earth metals oxides containing glasses on structural, thermal, and optical properties.
They synthesized a series of alkaline earth modified borosilicate glasses with the composition (40-x)SrO-(x)BaO-45SiO2-10B2O3-5ZrO2 (x=0, 10, 20, 30, and 40 mol%) via a melt quench technique.
Through testing, they clearly observed the mixed alkaline effect on structural, optical, and thermal properties. Specifically, the mixed modifier effect increased thermal stability and insulating properties and decreased mechanical properties.
“Based on observed properties, it is concluded that the present glasses can be used as sealants in SOFC except SB-20 and SB-0 glasses,” they write.
The paper, published in Journal of Non-Crystalline Solids, is “Mixed alkaline earth modifiers effect on thermal, optical and structural properties of SrO-BaO-SiO2-B2O3-ZrO2 glass sealants” (DOI: 10.1016/j.jnoncrysol.2021.120812).
The second group consists of researchers from the Bhabha Atomic Research Center in India and the Laboratory of Catalysis and Solid-State Chemistry near Lille, France. They investigated the effects of adding vanadium pentoxide (V2O5) to a barium-aluminosilicate sealing glass and a vanadium diboride-based self-healing composite.
They chose V2O5 due to its glass-forming ability and the necessity to keep thermal characteristics of the sealing glass as low as possible.
They found that V2O5 addition lowers the glass transition temperature, but it also leads to a decrease in peak crystallization temperature. “[This effect] is why 2% V2O5 content was found as an optimum value to carry out densification before crystallization occurs [compared to 4 and 6 mol.%.],” they write.
They then used a 15 vol.% vanadium diboride self-healing sealant containing 2 mol.% V2O5 to seal a ferritic stainless steel interconnect with good results—the microstructure at the seal’s interface showed “good bonding with no bubble or crack,” they write.
The paper, published in Solid State Sciences, is “Influence of V2O5 on a sealing glass and self-healing VB2-glass composites” (DOI: 10.1016/j.solidstatesciences.2021.106706).
Author
Lisa McDonald
CTT Categories
- Basic Science
- Energy
- Glass