[Image above] Credit: Bethan Phillips; Flickr CC BY-NC-ND 2.0
UPDATE: (1/18/2016) The temperature of the new method was originally and incorrectly reported as 390°C. The correct temperature is 200°C.
Silicon, a little element with just 14 protons, has a lot of uses in the world, from electronics to solar cells to composites and more.
Most of those useful uses employ silicon compounds, such as silica (aka silicon dioxide).
“Hundreds of thousands of tons of them are produced every year. They’re used to polish the silicon wafers that go into electronics, to strengthen tires, to make paints and paper white, as an abrasive in toothpaste, and yes, in countless tiny packets of silica gel,” according to a University of Michigan news story about a new technique to produce silica.
The silica industry is a big business, but it’s one that could use some improvements in efficiency—a lot of energy is required to heat silicon metal and anthracite coal to the high temperatures (3500°C) needed to produce silicon compounds.
But ACerS member Richard Laine, a professor of materials science and engineering at the University of Michigan, has devised a new strategy to make silica, one that requires much less energy input and can generate the compounds from waste materials.
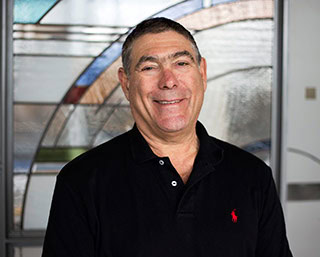
Credit: University of Michigan
According to the University of Michigan story, Laine says the process could save about six tons of carbon emissions per ton of produced silica and cost 90% less than current methods.
And the source of material for the new method? Agricultural waste.
Much agricultural waste contains silica. For example, hundreds of millions of tons of rice hulls (the hard outermost layer of rice grains) are annually produced worldwide.
Many of those discarded hulls are burnt as an electricity source, but even rice hull ash—much of which is then sent to landfills—still contains plenty of silica. Getting that silica out is the tricky part, however, thanks to the strong chemical bonds between silicon and oxygen.
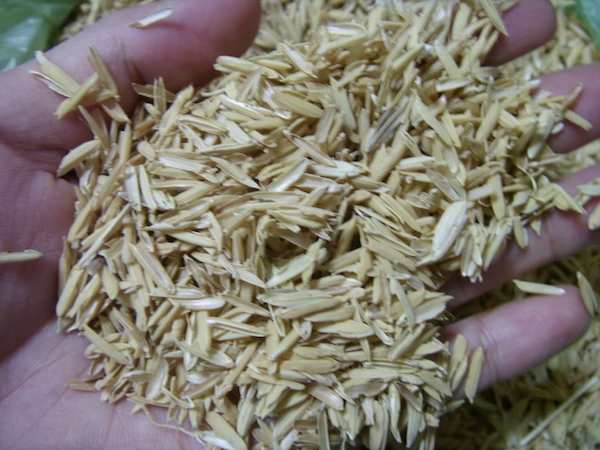
Rice hulls. Credit: Phu Thinh Co; Flickr CC BY-SA 2.0
“Laine found two easy and inexpensive ways to break that bond: ethylene glycol, or antifreeze, and ethanol, or grain alcohol,” according to the news story. “The antifreeze combined with a small amount of sodium hydroxide weakens the chemical bonds between the silica and the rice hull ash at the beginning of the process, dissolving the silica into a liquid solution.”
Heating that solution to just 200°C captures the silica as a silica–antifreeze polymer, which can be filtered to isolate the polymer from the rest of the ash.
“While this stage does require energy, it’s more than offset by the energy produced when the rice hulls are burned at the beginning of the process,” the story continues. “And because the carbon released when the hulls are burned was previously absorbed by the rice plant, the process is considered carbon-neutral.”
Due to the similar chemical structures of ethanol and antifreeze, adding grain alcohol to the polymer replaces the antifreeze, which can then be removed and reused. The silica can be distilled from the alcohol mix, isolating high-purity silica.
Laine is commercializing the tech through the company he formed, Mayasil, which is “in the process of building a ‘pre-pilot’ plant that will be used to develop a scaled up manufacturing process,” according to the news story. “If the scale-up is successful, Laine predicts that it will fundamentally change the way silica products are made and used.”
“I think eventually, we’ll be producing high-purity silica and other silicon compounds right next to the rice fields,” Laine adds in the story. “It will be possible to process rice and produce high-grade silica in a single location with little or no carbon footprint. It’s really very exciting.”
The paper, published in Agewandte Chemie, is “Avoiding carbothermal reduction: Distillation of alkoxysilanes from biogenic, green, and sustainable sources” (DOI: 10.1002/anie.201506838).
Author
April Gocha
CTT Categories
- Energy
- Environment
- Manufacturing
- Material Innovations