[Image above] OLED with composite structure of TiO2/graphene/conducting polymer electrode in operation. Credit: KAIST
Tomorrow’s electronic devices won’t just be more efficient, they’ll be durable enough to bend and stretch without the slightest fracture, all while being fully operational.
From smartphones to wearables to cameras, tech companies and researchers are innovating electronics that are thinner, more durable, and can bend without breaking.
And this year’s already revealing to be rife with major innovations in flexible electronic tech.
In March, scientists at Australian National University (Canberra, Australia) created what they describe as “the world’s thinnest lens, one two-thousandth the thickness of a human hair,” which could revolutionize flexible computer displays and miniature cameras.
Fast forward to April, and researchers from Columbia University’s School of Engineering and Applied Science reported that they’re developing a new flat, thin camera that is so flexible it can be wrapped around objects to capture images that can’t be taken with conventional cameras—even with multiple camera setups.
And last month, a team of researchers from Pennsylvania State University successfully created self-healing electronic materials capable of restoring device functionality post-bend-and-break trauma.
When it comes to next-gen flexible electronics, graphene’s been the standout material due to its single-layer thickness, toughness, and supreme mechanical and thermal properties—all of which make it the ideal choice for developing electronic, optoelectronic, and electromechanical devices and sensors.
As we’ve reported before, scaling up graphene for widespread use in consumer electronics has been complicated and expensive. But that time-to-market gap for commercially viable graphene continues to narrow.
This week, researchers from the Korea Advanced Institute of Science and Technology (KAIST) developed what they say is an “ideal electrode structure composed of graphene and layers of titanium dioxide and conducting polymers, resulting in highly flexible and efficient organic light-emitting diodes (OLEDs),” according to a KAIST press release.
Flexible OLEDs, when built on thin substrates—like plastic, glass, or foil—can be used to create next-gen electronic displays that can be rolled or bent while remaining fully operational.
As explained in the release, the OLED-on-substrate setup works like this:
OLEDs are stacked in several ultra-thin layers on the substrate, in which multi-layers of organic compounds are sandwiched between two electrodes (cathode and anode). When voltage is applied across the electrodes, electrons from the cathode and holes (positive charges) from the anode draw toward each other and meet in the emissive layer. OLEDs emit light as an electron recombines with a positive hole, releasing energy in the form of a photon. One of the electrodes in OLEDs is usually transparent, and depending on which electrode is transparent, OLEDs can either emit from the top or bottom.
An anode in conventional bottom-emission OLEDs is transparent, which allows the emitted photons to exit the device through its substrate, the release explains. A common material used for such a substrate is indium-tin-oxide (ITO) because it’s highly transparent and has low sheet resistance.
But ITO doesn’t come without its challenges. It’s not the cheapest material and, perhaps more concerning, it’s brittle—not ideal for developing flexible electronic devices to scale.
Enter: Graphene. It’s naturally conductive and ultrathin properties seemingly make it an ideal alternative to ITO. But, as the release explains, the performance of graphene-based OLEDs reported to date hasn’t really outpaced ITO-based OLEDs.
So to solve graphene’s underwhelming performance issue, the KAIST team proposed a new device architecture that can maximize the efficiency of graphene-based OLEDs.
The team “fabricated a transparent anode in a composite structure in which a TiO2 layer with a high refractive index (high-n) and a hole-injection layer of conducting polymers with a low refractive index (low-n) sandwich graphene electrodes. This is an optical design that induces a synergistic collaboration between the high-n and low-n layers to increase the effective reflectance of transparent electrodes,” the release explains.
This new approach maximizes optical cavity resonance—and that’s important because improved optical cavity resonance translates directly to improved efficiency and color gamut in OLEDs, according the release.
The team also found that the new approach reduced loss from surface plasmon polariton (SPP), a major cause for weak photon emissions in OLEDs, thanks to the presence of the low-n conducting polymers.
When put to the test, the team says these graphene-OLED devices remain intact and operational even after 1,000 bending cycles at a radius of curvature as small as 2.3 mm—a remarkable result for OLEDs containing oxide layers such as TiO2, the team says, because oxides tend to be more brittle and are prone to fracture even at low strain.
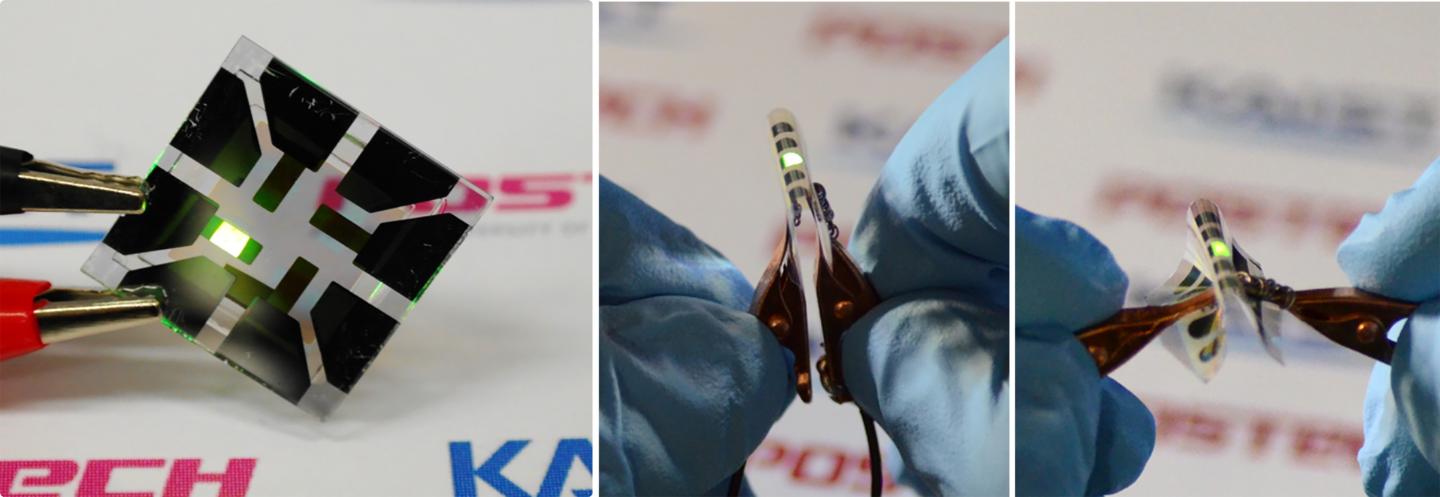
OLED with composite structure of TiO2/graphene/conducting polymer electrode in operation. The OLED exhibits 40.8% of ultrahigh external quantum efficiency (EQE) and 160.3 lm/W of power efficiency. The device prepared on a plastic substrate shown on the right remains intact and operational well after 1,000 bending cycles at a radius of curvature as small as 2.3 mm. Credit: KAIST
“What’s unique and advanced about this technology, compared with previous graphene-based OLEDs, is the synergistic collaboration of high- and low-index layers that enables optical management of both resonance effect and SPP loss, leading to significant enhancement in efficiency, all with little compromise in flexibility,” Seunghyup Yoo, one of the lead researchers and electrical engineering professor at KAIST, says in the release.
The team hopes this advancement could lead to more sophisticated flexible consumer electronics in the not-too-distant future.
Tae-Woo Lee, the other lead researcher from the Department of Materials Science and Engineering at Pohang University of Science and Technology, says he expects that the technology “will pave the way to develop an OLED light source for highly flexible and wearable displays, or flexible sensors that can be attached to the human body for health monitoring.”
The research, published in Nature Communications, is “Synergetic electrode architecture for efficient graphene-based flexible organic light-emitting diodes” (DOI: 10.1038/ncomms11791).
Author
Stephanie Liverani
CTT Categories
- Electronics
- Manufacturing
- Material Innovations