[Image above] University of Cambridge researchers partnered with Materials Processing Institute to test their simultaneous steel and cement recycling process at scale in an electric arc furnace. Credit: Cambridge University, YouTube
In addition to cement and concrete, steel production is another emissions-intensive industry. However, “The emissions reduction potential of conventional process routes and scrap is limited,” according to the International Energy Agency website, “and so innovation this decade will be crucial to commercialize new near zero-emission steel production processes.”
On May 22, 2024, three groups announced different approaches to reduce carbon emissions in this heavy industry. Highlights from each announcement are below.
Use of hydrogen in steel production: Effects on refractories
In a monthly newsletter, Austria-based international refractories manufacturer RATH announced the results of its study on how hydrogen firing affects the refractory materials used in steel plants.
The use of hydrogen as a replacement for fossil fuels is a hot topic in many industries, including steel and glass, because it generates little or no carbon dioxide depending on its production method. However, as explained in the cover story of the March 2022 Bulletin, using hydrogen to fire a furnace changes its atmospheres and temperature characteristics. So, manufacturers may need to adopt novel refractory materials and configurations to maintain current furnace lifetimes and maintenance schedules.
In the study conducted by RATH personnel, comprehensive comparative corrosion tests were carried out on the company’s portfolio of aluminosilicate and high-alumina refractory materials. Samples in the form of lightweight bricks, dense bricks, monolithic products, high-temperature wool mats, and vacuum-formed parts were all evaluated.
Main findings from the study were
- High-corundum materials showed very good corrosion resistance in all products.
- Under certain conditions, mullite was a suitable material in an atmosphere containing hydrogen.
- Glass phases and SiO2 phases were significantly reduced in high-hydrogen atmospheres.
- Foreign oxides and impurities in the refractory material significantly affected system stability.
- Porosity of refractory materials had only a minor influence on corrosion.
- A significant increase in the corrosion rate was recorded in the temperature range of 1,250–1,400°C.
- Phosphate-bonded fired bricks were only slightly more resistant to corrosion than phosphate-free products.
“In summary, RATH’s study results are highly relevant for future material selection in the respective application [steel production],” the newsletter concludes.
Making steel with electricity: Commercialization of molten oxide electrolysis
In a news story, the Massachusetts Institute of Technology News Office reported on the work of university spinout Boston Metal, which is commercializing an electrochemical process called molten oxide electrolysis (MOE) to decarbonize steelmaking.
In general, electrolysis is a technique that uses direct electric current to drive an otherwise nonspontaneous chemical reaction. In Boston Metal’s process, iron ore rock is fed into a modular cell that contains an anode and cathode immersed in a liquid electrolyte. When electricity runs between the anode and cathode and the cell reaches about 1,600°C, the iron oxide bonds in the ore are split, producing pure liquid metal that can be collected from the bottom of the cell.
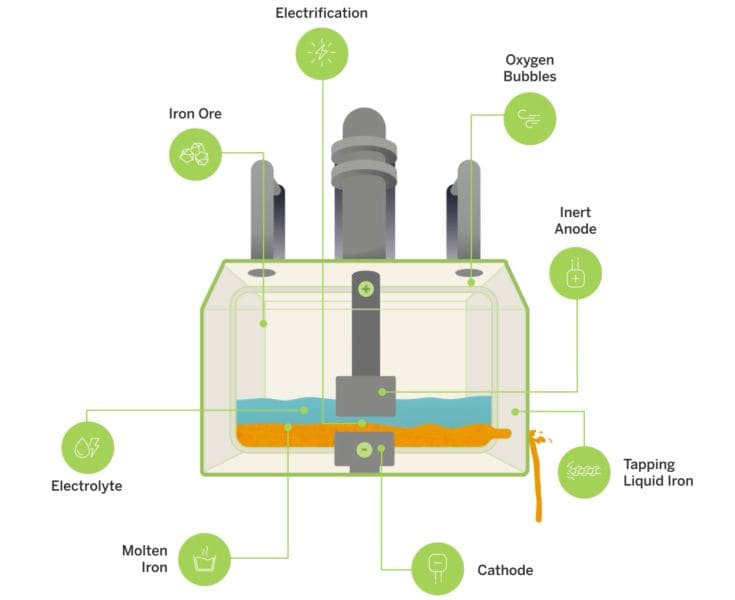
Schematic of Boston Metal’s molten oxide electrolysis process for steel production. The modular cells in this process are each the size of a school bus. Credit: Boston Metal
The only byproduct of the MOE reaction is oxygen, and the process does not require water, hazardous chemicals, or precious-metal catalysts. Thus, “I think our approach goes hand in hand with that…tremendous worldwide push to decarbonize the energy sector,” says Guillaume Lambotte, chief scientist at Boston Metal and former MIT postdoc, in the news story.
Since the company was founded in 2012, the MOE process has gone from being a coffee cup-sized experiment that produces a few grams to an industrial-scale method that produces hundreds of kilograms. Boston Metal’s leadership expects the process will be scaled to produce tons of metal by 2026, but they are already using the process to recover high-value metals from mining waste at the company’s Brazilian subsidiary, Boston Metal do Brasil.
Simultaneous steel and cement recycling significantly reduces emissions from both industries
In a press release, researchers at the University of Cambridge in the U.K. announced how the simultaneous recycling of steel and cement can significantly reduce carbon emissions in both of these industries.
Traditionally, lime–dolomite flux is used in steel recycling to protect the steel from air, provide the required basicity for the process, protect the lining and graphite electrodes, and increase energy efficiency.
However, as described in their open-access Nature paper, the Cambridge researchers found that recovered cement paste can be substituted for the lime–dolomite flux with only slight adjustments to account for the silica content in the paste. This substitution has two benefits:
- In the traditional process, the lime–dolomite flux ends up as a waste product (slag). Using cement paste, however, results in recycled cement that can be used to make new concrete (despite its higher levels of iron oxide).
- If the process is powered by emissions-free electricity, it can lead to zero-emissions cement while also reducing the emissions of steel recycling by reducing lime–dolomite flux requirements.
In partnership with Materials Processing Institute, the Cambridge researchers showed the process can be performed at scale in an electric arc furnace. In the press release, they say the process could possibly produce one billion tonnes of cement per year by 2050, which represents roughly a quarter of current annual cement production.
The researchers have filed a patent on the Cambridge Electric Cement process to support its commercialization.
Author
Lisa McDonald
CTT Categories
- Cement
- Manufacturing
- Refractories