[Image above] Compared to conventionally fired ceramics, ceramic tiles grown via microbial activity release less carbon dioxide into the atmosphere during the manufacturing process. But the process must be optimized to ensure the tiles have sufficient mechanical properties. Credit: PxHere
When something is said to have been built from the ground up, the phrase is typically used in a figurative manner. But in the case of bricks created by Dyllon Randall, associate professor of civil engineering at the University of Cape Town in South Africa, the phrase serves as a literal description.
In 2018, Randall and his students grew bricks at room temperature using microbially induced calcium carbonate precipitation (MICP). MICP is a biomimetic process that relies on the metabolic action of microorganisms to form calcium carbonate. The process is primarily used to improve soil properties, but Randall and his students used it to bind sand together, thus forming a brick.
The biobricks made headlines in 2018 due to a key ingredient that Randall and his students used in the MICP process—human urine. Urine served as the source of urea, an organic compound and waste product excreted by many living organisms. In the MICP process, microorganisms produce an enzyme called urease that breaks down the urea into carbonate ions, which combine with excess calcium ions to form calcium carbonate.
While the biobricks offered several benefits over conventionally fired bricks, such as reducing the release of carbon dioxide into the atmosphere during processing, each brick was produced individually. A method for producing multiple bricks at a time is required to scale up the process for commercialization.
The submersion technique, developed by Zhao et al. in 2014 for biocolumns, has potential for scaling up production of MICP-based biomaterials. In this method, the MICP process takes place within a full-contact flexible mold to enhance the reaction between the microorganisms and the cementation medium (e.g., sand).
In 2020, Cheng et al. used the submersion technique to produce several biobricks simultaneously. However, they discovered that the centers of the bricks were weaker than the outer edges, confirming the results of a previous study by Bu et al. in 2018.
“Hence, the manufacturing of a biomaterial that is thinner, such as biotiles, should allow for more consistent diffusion and compressive strength,” Randall and his colleagues write in a new open-access paper.
Randall wrote this paper with doctoral student Emma Jane Horn and Robert Huddy, proposal development project manager in the Faculty of Health Sciences. They aimed to grow strong ceramic tiles using the MICP process by focusing on four key parameters, which previous studies identified as majorly influencing the final properties of MICP-based biomaterials:
- Calcium concentration
- Urea concentration
- Particle size distribution of aggregate material (in this case, unsieved dune sand)
- Magnesium concentration
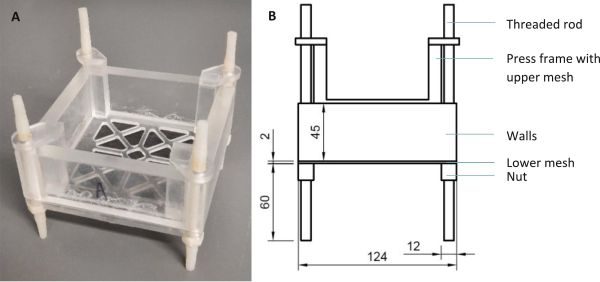
Photo (A) and schematic diagram (B) of biotile mold, where the press frame with upper mesh closes downward with wing nuts to compress a biotile of desired height. Clear acetate and petroleum jelly lined the walls of the mold. Dimensions in mm. Credit: Horn et al., Science of The Total Environment (CC BY-NC-ND 4.0)
As seen in the chart below, the researchers determined the parameters necessary to achieve biotiles with acceptable values for breaking strength (637 N ± 60 N) and modulus of rupture (13.0 N/mm2 ± 2.3 N). These values exceed the conventional standards of breaking strength (600 N) and modulus of rupture (8 N/mm2) for tiles with a water absorption above 10%.
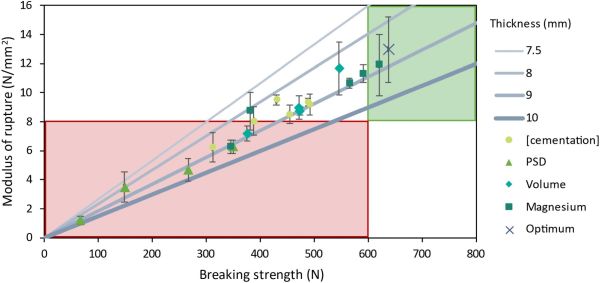
Chart depicting the data for each of the four key parameters tested, with diagonal lines showing the minimum thickness (mm) along the broken edge of the biotile and the breaking strength (n = 4) and modulus of rupture targets to be met. The red region indicates where neither of the targets are met, the white regions indicate where one target is met, and the green region indicates where both targets are met. Credit: Horn et al., Science of The Total Environment (CC BY-NC-ND 4.0)
The researchers note that synthetic urea was used as the urea source in this study, but they acknowledge that human urine could also be used as the urea source.
“This [choice of urine] would result in the recycling of another ‘waste’ stream, but at an additional cost. It is therefore suggested that future work look at a detailed economic and life cycle assessment of the proposed process for a range of products (bricks, pavers, roof tiles, etc.) and different operational conditions,” they conclude.
The open-access paper, published in Science of The Total Environment, is “Growing bio-tiles using microbially induced calcium carbonate precipitation” (DOI: 10.1016/j.scitotenv.2023.165050).
Author
Lisa McDonald
CTT Categories
- Environment
- Material Innovations