[Image above] University of Illinois professor Paul Braun holds a model showing how a simple layered material, depicted in orange and blue, transforms into a complex Archimedean-structured composite when it freezes around a template, depicted in gray. Credit: Fred Zwicky, University of Illinois
We are now almost a month into the new year, which I find hard to believe—the weather in Columbus has felt like autumn these past few weeks!
The weather finally started acting like true winter a few days ago, but even before the chill, I knew snow was on its way—thanks to the new white lines on the roads.
Cities often proactively prepare for winter weather by spreading anti-icing chemicals on the pavement. Salt is a common anti-icer—giving the appearance of those white lines—because it keeps the roads from icing by mixing with water to create a eutectic system.
A eutectic system is a homogeneous mixture of substances that melts or solidifies at a temperature lower than the melting point of the constituent elements. For example, water typically freezes at 0°C (32°F) but will freeze at -16°C (2°F) in a 20% salt solution, meaning temperature must be considerably colder before ice forms on the roads.
However, when eutectic liquids do solidify, they demonstrate a unique ability—individual components of the mixture self-assemble to form a cohesive structure. This ability is highly desirable in the production of many modern technologies.
“Instead of depositing layers of material individually, we start with a liquid that self-assembles as it solidifies,” Paul Braun, professor of materials science and engineering and director of the Materials Research Lab at the University of Illinois at Urbana-Champaign, says in a university press release. “This can speed up production and allows us to make larger volumes at one time.”
Many common solder alloys used in electronics are eutectic materials, such as tin-lead alloys. Also, directionally solidified turbine blades comprised of eutectic alloys are in regular service in both commercial and military jet engines.
However, natural self-assembly can be limiting.
“Decades of research on solidification of binary and ternary eutectic systems indicate that only a limited set of regular mesostructures emerge, even over a broad range of processing conditions,” Braun and coauthors explain in a recent paper. “By engineering the heat removal, for example, the microstructure could be modified … however, the resulting microstructures are still quite similar to those found in the native eutectic.”
This narrow range of natural self-assembled structures is why Braun and coauthors from University of Illinois (Ashish Kulkarni and Runyu Zhang) and University of Michigan (Erin Hanson and Katsuyo Thornton) decided to investigate synthesizing eutectic materials by templating.
Template synthesis uses a template to control material formation and is one of the most important techniques for controlled synthesis of nanostructured materials.
“Templating is a common practice used in organic polymers processing,” Kulkarni, first author and graduate student, says in the press release. “However, it is not something that has been explored in inorganic materials processing because inorganic microstructures are more rigid and harder to control.”
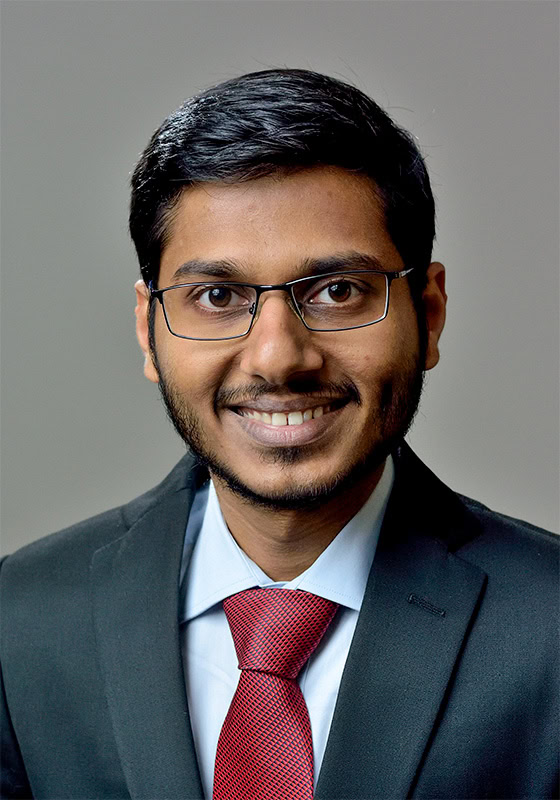
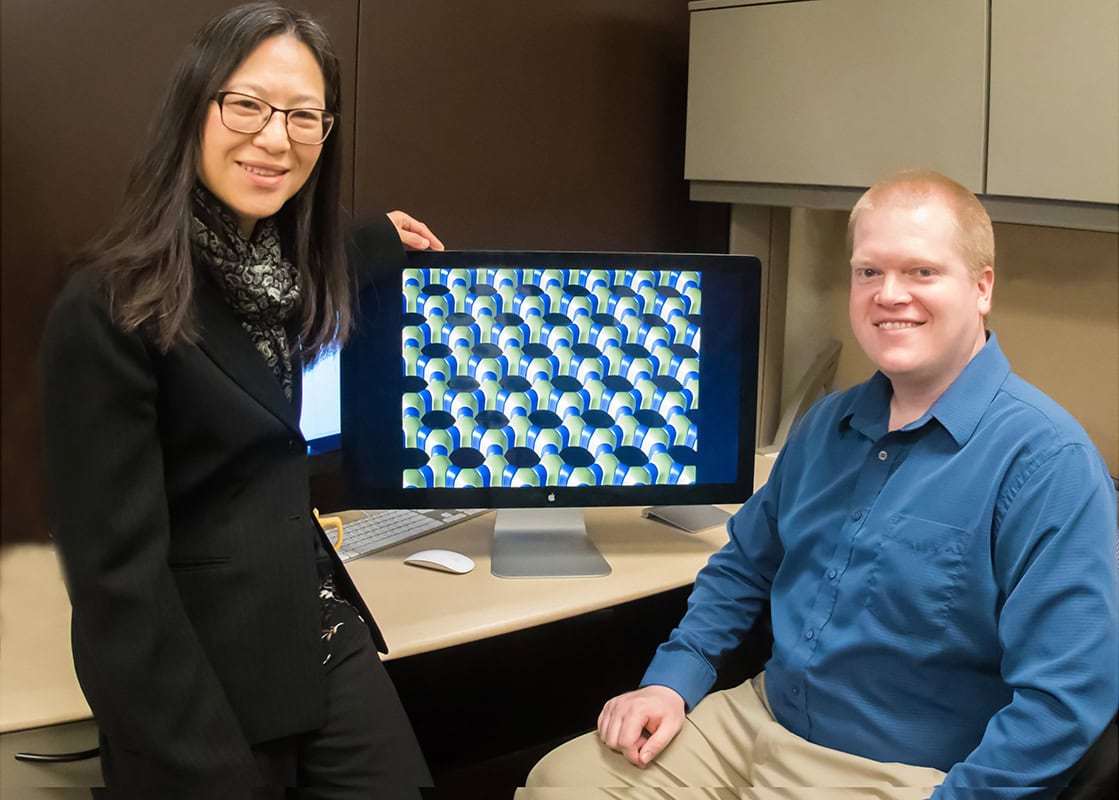
To investigate templating inorganic eutectic materials, the researchers studied silver chloride-potassium chloride (AgCl-KCl). “The silver chloride-potassium chloride system was largely selected as a model system due to it forming a simple lamellar eutectic [material with layered structure] with a low (318°C) melting point,” Braun and Kulkarni explain in an email. “This system is also interesting because it is optically transparent, and readily forms microstructures with characteristic length scales on the order of the wavelength of visible light. Finally, this system has a low surface tension, and thus flows easily into the template.”
The researchers poured an AgCl-KCl melt in a template containing tiny posts arranged in hexagonal shapes. As the AgCl-KCl melt solidified, the posts disrupted layer formation and caused a composite to form with an array of different square, triangular, and honeycomb-shaped microstructures.
The fact the researchers achieved new microstructures was not the only exciting finding—they also found the template reduced the number of defects in the material.
“When eutectics are forced to solidify through a template, the template both modifies and regulates the kinetics of the solidification and increases the energetic cost of defect formation,” Braun and Kulkarni explain. “The net effect is that if the template has a near-perfect repeating pattern (like in our case), the eutectic solidifying through it will closely follow the order of the template and thus have reduced number of defects.”
Braun and Kulkarni say they are now working on fabricating such Archimedean patterns out of metal-dielectric eutectics for use as optical metamaterials (in contrast to the all-dielectric system used in this study). They are also looking at the possibility of designing templates that could lead to eutectic microstructures with quasicrystalline patterns (the Chemistry Nobel Prize-winning topic of 2011).
“If we succeed, then we can potentially impart such exotic microstructures, forming for example materials with unique magnetic properties from what otherwise would be a simple eutectic material,” Braun and Kulkarni say.
The paper, published in Nature, is “Archimedean lattices emerge in template directed eutectic solidification” (DOI: 10.1038/s41586-019-1893-9).
Author
Lisa McDonald
CTT Categories
- Material Innovations