[Image above] Piston rings play an essential role in the transfer of heat and containment of gases and oil within a combustion engine. A hybrid process could improve the deposition of coatings on these rings to protect them from wear. Credit: Scott Pargett, Wikimedia (CC BY 2.0)
While I am grateful to own a Kia when navigating the narrow streets around my home, I still miss the 2001 Buick LeSabre that got me through high school and college.
Of course, being from 2001, it’s no surprise I eventually had to trade the Buick in once repairs cost more than the car was worth. But along the way I learned a lot about the inner workings of a car, one worn part at a time.
Piston rings are small components that play a big role in the efficiency of a gas-powered vehicle. As the video below explains, there are three rings on each piston, and they play an essential role in the transfer of heat and containment of combustion gases and oil within the engine.
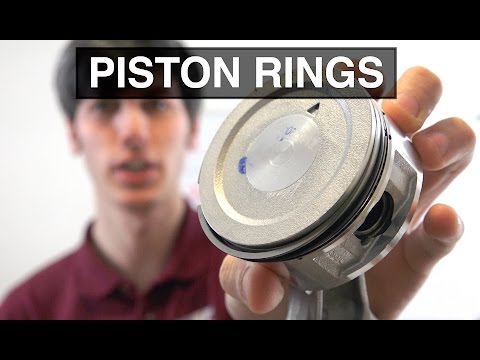
Credit: Engineering Explained, YouTube
When the piston rings become worn or damaged, oil can leak past the rings into the combustion chamber, where it burns and raises the vehicle’s pollutant emission levels. In recent years, the move toward cleaner fuels with reduced sulfur content has ironically made the rings more likely to wear, as the lower sulfur content negatively affects the lubricity of combustion residues. Fortunately, development of new coatings can counteract this effect.
There are numerous types of coatings used on piston rings today. These coatings are typically added using physical vapor deposition (PVD), a group of established processes that work with a variety of material classes.
Magnetron sputtering is a PVD technique widely used in industry due to its advantages of high speed, low temperature, and low damage. In this process, a magnetic field is used to concentrate high-energy ions onto the coating material.
Among the magnetron sputtering processes, direct current magnetron sputtering (dcMS) and high-power impulse magnetron sputtering (HiPIMS) are top choices. dcMS is easily implemented due to the low number of parameters needed for optimization. However, because dcMS relies on continuous current levels, the metallic target may overheat and experience permanent damage. HiPIMS avoids the issue of overheating by using elevated peak power and current applied in short pulses, but its deposition rate is lower than dcMS.
Researchers have explored combining dcMS and HiPIMS in a hybrid process to achieve faster deposition rates. The hybrid process also allows researchers to produce nanostructured multilayers with superlattice structures by tailoring the way different target materials are switched to the different power supplies.
In a recent open-access study, researchers from Brazil and Chile add to the literature on this hybrid process by using it to deposit chromium nitride/chromium aluminum nitride (CrN/Cr1-xAlxN) multilayer coatings on piston rings.
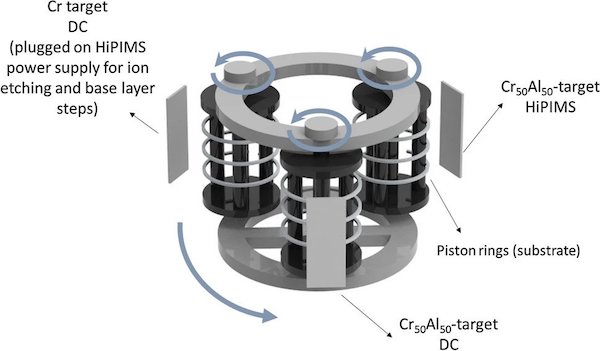
Scheme of the carousel rotation within the sputtering system mounted with gas-nitrided piston rings and three sputtering targets: two of a chromium alloy (50–50 at.%) and one of pure chromium. Credit: de Castilho et al., Scientific Reports (CC BY 4.0)
Analysis of the CrN/Cr1-xAlxN coatings revealed improved wear resistance compared to a commercial chromium nitride reference. Specifically, wear depth produced in the CrN/Cr1-xAlxN multilayers by reciprocating sliding against the cylinder liner was 50% lower than in the reference material, “thus indicating that the multilayers grown by the hybrid sputtering process proposed here is a suitable solution for piston rings of the next generation of diesel combustion engines,” the researchers write.
The open-access paper, published in Scientific Reports, is “Hybrid magnetron sputtering of ceramic superlattices for application in a next generation of combustion engines” (DOI: 10.1038/s41598-022-06131-9).
Author
Lisa McDonald