[Image above] Hitting crystalline alumina with intense laser bursts turns the material into a plasma that cools rapidly on a substrate to form a glassy solid. Credit: Erkka Frankberg, Tampere University
In numerous CTT posts last year, we discussed the inherent brittleness of oxide glasses and how scientists work to combat this shortcoming by increasing an oxide glass’s ductility, i.e., a material’s ability to plastically deform without fracturing.
We described several techniques to increase glass (micro)ductility, including hydrating the atomic network and adding nanoparticles to the glass (investigated experimentally and through simulation). Yet “the plastic deformation mechanisms at room temperature are believed to be limited to geometrically confined loading modes, such as bulk indentation,” researchers write in a recent paper.
The researchers come from various universities and institutes in Finland, France, Italy, Austria, Norway, and the United States. And they explain that unless an oxide glass can plastically deform under unconfined loading conditions, such as bending and pulling, its applications still are limited.
Silica glass, the most common type of glass, likely will not achieve such unconfined plastic deformation because of small gaps in the atomic structure that prevent atoms from moving around when the material is stressed, explains Erkka Frankberg, postdoctoral researcher at Tampere University of Technology (Finland), in a C&EN article. However, another kind of glass might: aluminum oxide (alumina).
“Experimental observations of Al2O3 at the nanoscale have been mixed: Some measurements show prerequisites for plastic deformation at room temperature (15–18), whereas others display fully brittle behavior (19–21),” the researchers write in the paper.
They decided to create alumina glass and test the ductility themselves. But creating alumina glass is not easy.
“It is exceedingly difficult to convert aluminum oxide into a glassy substance. The traditional glass manufacturing processes cannot be applied to aluminum oxide because it easily transforms into the crystalline form,” Frankberg says in a Tampere University press release. “The solution is to cool the material down extremely fast from a high temperature to prevent crystallization.”
To accomplish this extremely fast cool down, the researchers used pulsed laser deposition to turn crystalline alumina into 60-nm-thick, 2-µm-wide alumina glass films.
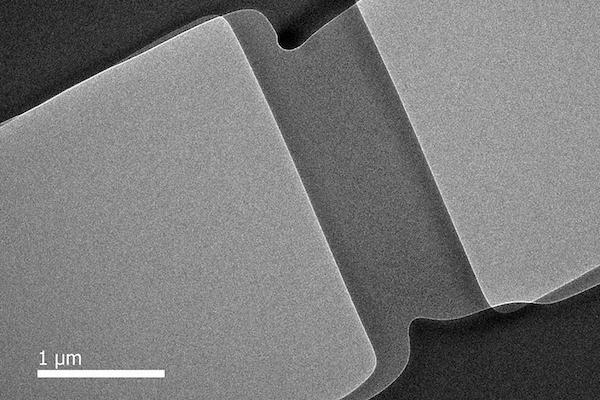
Through experimental measurements supported by simulations, the researchers showed their microscopic films could stretch by 8% and compress to half their size before fracturing. They attributed this relatively high plasticity to the fact that their alumina glass, unlike silica, has a tightly packed, defect-free atomic network, which means the atoms “can more easily switch places, which is needed for plastic deformation,” Frankberg says in the C&EN article.
Translating this research to real-world application, though, could be a long way off. Because alumina prefers to be in a crystalline rather than glassy form, making large pieces of the material will require advances in manufacturing and new processing techniques.
Still, “this work clearly provides a guide to chemists on how to design better glasses,” says Antonio Facchetti, a chemist at Northwestern University unaffiliated with the study, in the C&EN article.
The paper, published in Science, is “Highly ductile amorphous oxide at room temperature and high strain rate” (DOI: 10.1126/science.aav1254).
Author
Lisa McDonald
CTT Categories
- Basic Science
- Glass