[Image above] Rather than lighting electric candles, lithium-ion batteries tend to really catch on fire when their polymeric separators fail. Separators made from oxide ceramic films could be a solution. Credit: Pixabay
Tesla has been on fire lately—and not in a good way.
In April, an older Model S seemingly spontaneously combusted while sitting in a parking structure, and only a few weeks later, another Model S in a different parking lot did the same. Tesla is pushing out an over-the-air software update in response to the fires as it tries to determine the root cause.
The fire problem Tesla faces is not unique—any company relying on lithium-ion batteries (as Tesla does) takes on a certain amount of risk. The property that makes Li-ion batteries desirable—the ability to store large amounts of energy—also sets these batteries up for large explosions when they short circuit.
The main reason Li-ion batteries short circuit is due to separator failure. A separator is a permeable membrane between a battery’s anode and cathode that keeps the two from touching. If the separator fails and the two electrodes contact, it can lead to a thermal runaway situation in which temperatures rise rapidly and cause the flammable liquid electrolyte to combust.
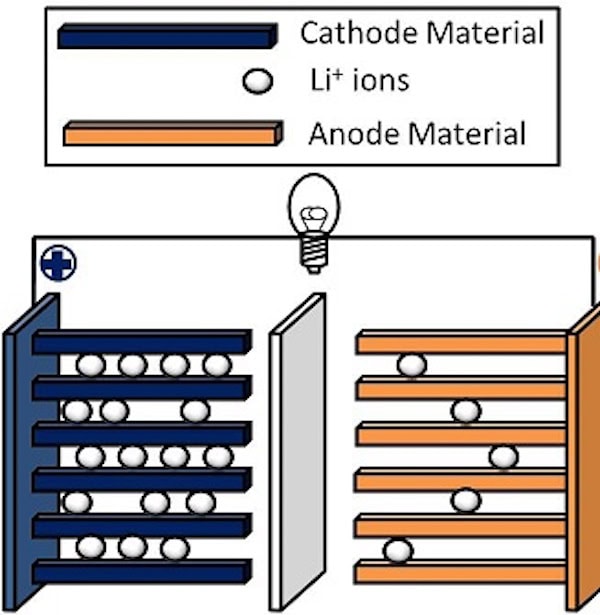
Failure of the separator (center) is a major cause of battery fires. Credit: Materialsgrp, Wikimedia
Many separators fail because they are made of polymeric materials that have low melting temperature, poor mechanical strength, and poor chemical inertness, which are unfortunate qualities to have when undergoing excessive heating and chemical oxidation during charge cycles.
To enhance the stability of separators, efforts have been focused on several methods, including:
- Fabricating ultrastrong separators with special polymers that can withstand high temperatures of 120°C–350°C;
- Blending different polymers together to construct multicomponent separators; and
- Forming composite separators by filling or coating polymeric separators with chemically and thermally stable ceramic particles.
Though these methods do improve polymer separator stability, there are still some challenges. For example, thermal runaway can cause temperatures to reach over 500°C, at which point the separators degrade immediately. Also, ceramic particles may block pores and impede Li-ion transfer.
Though polymer is the precedent material for Li-ion battery separators, it is not the only option. As researchers from Donghua University in Shangai showed in a recent study, rather than just coating polymeric separators with ceramic particles, a separator made from an oxide ceramic film could prove a better option.
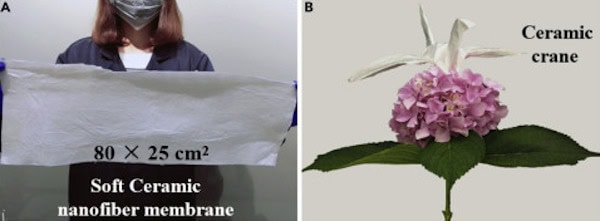
The Donghua researchers tested the efficacy of oxide ceramic nanofiber films as separators for Li-ion batteries (the films doubled as cute cranes too!). Credit: Yan et al., iScience (CC BY-NC-ND 4.0)
“Oxide ceramics have been widely used in engineering and technology fields and enjoyed rapid development because of their superior properties such as robust mechanical strength, exceptional thermal and chemical stability, and physical integrity,” the researchers explain in an open-access paper on their research.
Specifically, the researchers note that recently scientists have successfully fabricated binary oxide ceramic films such as ZrO2, TiO2, and Al2O3 with shape memory performance. The mechanical responses of these “soft” oxide ceramics offer appealing prospects to a variety of fields, with one application being Li-ion battery separators.
In their study, the Donghua researchers developed a scalable ceramic nanofiber fabrication technique based on electrospinning and calcination. They used this method to create a variety of ceramic films, including binary oxide of SiO2, ternary oxide of BaTiO3 (BTO), and quaternary oxides of Li7La3Zr2O12 (LLZO) and Li0.33La0.56TiO3 (LLTO).
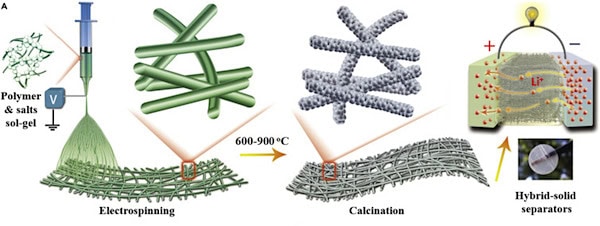
A general depiction of sol-gel electrospinning followed by calcination to fabricate ceramic nanofiber separators for Li-ion batteries. Credit: Yan et al., iScience (CC BY-NC-ND 4.0)
The researchers found that when applied to Li-ion batteries, all their synthesized ceramic nanofiber separators exhibited low internal ionic penetration resistivity, high chemical stability, and robust mechanical strength. Additionally, the ceramic separators rendered batteries with high thermal stability over the operating temperature range without thermal runaway.
However, the researchers did give two words of caution in their conclusion. One, despite attempting to minimize the separators’ pore sizes by increasing film thickness and by adding a small amount of polyvinylidene fluoride (PVDF) polymers in the electrolytes, the films still had a larger average pore size than commercial separators. Two, they did not characterize the separators’ ability to resist lithium dendrite growth, which is another safety factor that should be considered.
Despite these limitations, the researchers conclude, “This work provides a promising strategy to produce oxide ceramic films that possess both soft and rigid properties with a low-cost and scalable synthesis method.”
The open-access paper, published in iScience, is “Polymer template synthesis of soft, light, and robust oxide ceramic films” (DOI: 10.1016/j.isci.2019.04.028).
Author
Lisa McDonald
CTT Categories
- Electronics
- Energy