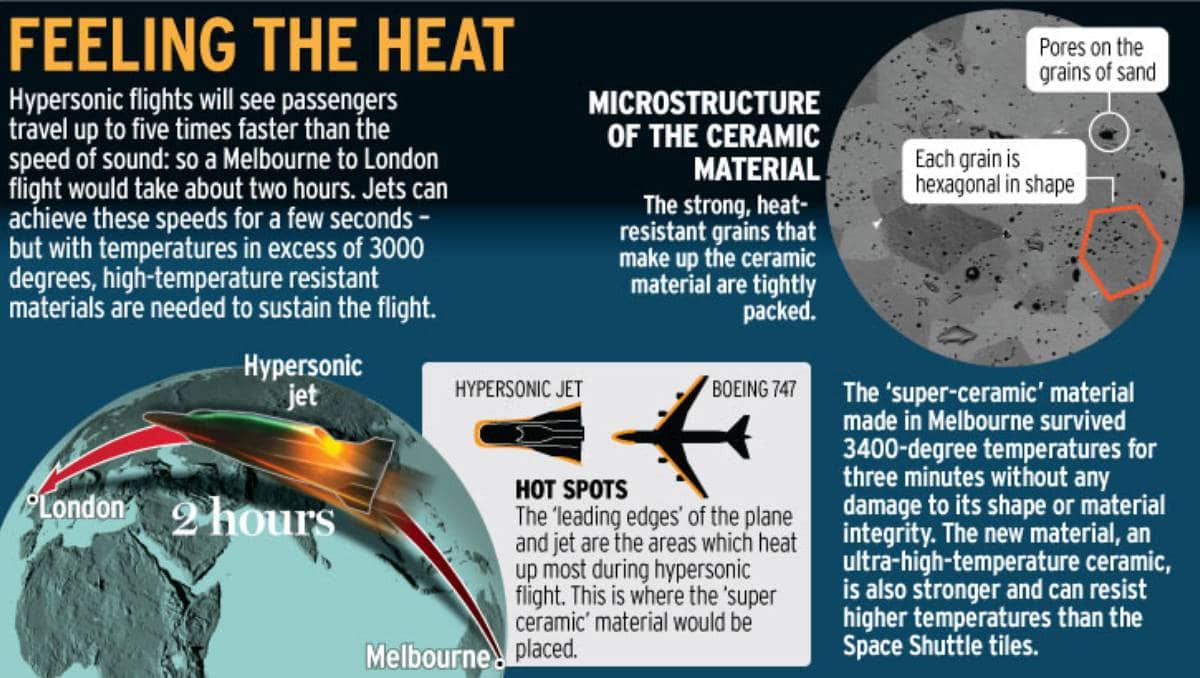
Credit: Sydney Morning Herald; University of Melbourne.
From Fresh Science:
Melbourne University (Australia) researchers are doing rocket science with clay. They have developed a cheaper and more efficient way of making the complex, heat-resistant, ceramic parts needed to build tomorrow’s rockets and hypersonic airliners.
Using clever chemistry to modify a standard method of casting ceramics in a mold, they have developed an alternative to the traditional technique of forming these ceramics as blocks at high temperatures and pressures. And their new method, a form of slip casting, allows them to generate ultrahigh-temparture ceramic components at lower temperatures and pressures, which do not require extensive machining, hence saving time and energy.
“The ceramic pieces we have made are stronger and will survive to higher temperatures than those used on the Space Shuttle,” says Carolina Tallon, who is developing the processing techniques with George Franks of the Department of Chemical and Biomolecular Engineering at the University of Melbourne. Their work is part of the propulsion program of the Defense Materials Technology Center to develop manufacturing capabilities of advanced materials within Australia.
Hypersonic flight will allow passengers to travel at up to five times faster than the speed of sound (Mach 5). A flight between Melbourne and London would take about two hours. Jets have already been built that can achieve these speeds for a few seconds, but maintaining those conditions for an entire flight remains a challenge: and it’s partly a materials challenge.
“In order to lengthen the duration of the hypersonic flight, we need to find a perfect match between aerodynamic design and the materials able to survive what that design entails,” Tallon says. “At Mach 5, for instance, several of the components of the vehicle will be at temperatures of above 3,000°C. At these temperatures, most of the materials typically used in the aerospace industry will already have melted or if they have not, their properties will be severely damaged and they will not perform correctly.”
Ultrahigh-temparture ceramics are a potential solution since they can survive such extreme conditions. But finding the right material is not the end of the story. The actual components to be used in the vehicle have to be formed into complex shapes.
With traditional processing techniques, the nose of a rocket, for example, would be manufactured using very high temperatures and pressures to produce a very simple geometry such as a solid cylinder, which would then require extensive and costly machining. The new slip casting technique simply requires a mould into which a low viscosity slurry of a particular chemistry can be poured. The ceramic particles then pack efficiently into the required shape as the solvent is removed.
“Using these techniques, I can manufacture components, that already resemble their final shape without machining. This can all be done at lower temperatures and pressures-and the end products are stronger than those made in the traditional manner. The preliminary tests showed that the components we made were able to survive temperatures above 3,400°C while keeping their shape and mechanical integrity,” Tallon says. “This technique is so versatile that we can fabricate anything from hip replacements to turbine rotors.”
This Australian technology is the result of extensive collaboration between researchers at universities, national laboratories and industry within the Defense Materials Technology Center.
Carolina Tallon is one of 12 early career scientists unveiling their research to the public for the first time thanks to Fresh Science, a national program sponsored by the Australian Government.
CTT Categories
- Aeronautics & Space
- Manufacturing
- Thermal management