[Image above] An example of the McKee-Farrar prosthesis, which was the first widely used total hip replacement to employ a metal-on-metal articulation. These implants had a high rate of early aseptic loosening. Today, metallic implants are often coated with bioactive materials to improve adhesion to the host tissue. Credit: John Marton, National Archives and Records Administration
From a mechanical standpoint, metallic materials such as stainless steel, cobalt–chromium, and titanium-based alloys are the gold standards for load-bearing implants, such as hip and knee replacements.
But though these alloys are biocompatible, meaning they do not provoke an adverse effect in the host tissue, they are not bioactive, meaning they do not provoke a beneficial response either.
This lack of bioactivity means metallic implants sometimes struggle to attach to the host tissue, which can lead to loosening and eventual failure of the implant. For this reason, metallic implants are often coated with bioactive materials to improve their integration.
Bioactive glass offers numerous benefits as a coating material. For example, it forms a hydroxycarbonate apatite layer at the interface with bone that helps promote bone cell growth along the implant’s surface.
Commercializing bioactive glass coatings is complicated, however, by the large difference in the coefficient of thermal expansion (CTE) between the coatings and metallic implants. This mismatch leads to accumulation of residual stress at the coating/implant interface, which weakens interfacial adhesion.
To use bioactive glass coatings, then, “an improvement in their adhesion strength becomes necessary,” researchers write in a recent open-access paper.
The researchers come from the University of Barcelona in Spain. In their study, they focused on improving the adhesion strength of bioactive glass coatings deposited using atmospheric plasma spraying (APS).
APS involves injecting powders of the coating material into a plasma jet via a carrier gas, usually argon. The powder particles then melt and are sprayed over the substrate to be coated.
Ceramic coatings, specifically hydroxyapatite, deposited by APS are widely used in the medical field. But bioactive glass coatings deposited by APS, though they have a higher bioactive capacity than hydroxyapatite, have to date demonstrated low adhesion strength.
The researchers deeply evaluated several strategies to enhance the adhesion strength of bioactive glass coatings, including
- Changing the morphology of the feedstock powders through agglomeration;
- Incorporating hydroxyapatite as a support material, either as an anchor layer or blended with the glass powder; and
- Applying heat before or after the spraying process to reduce internal stresses in the coating.
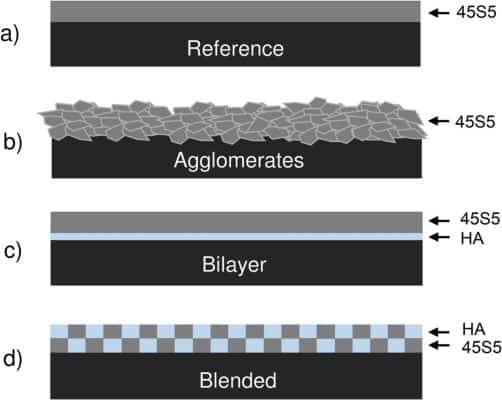
Designed coatings: a) reference, b) agglomerates, c) bilayer, and d) blended. Credit: Garrido et al., Surface and Coatings Technology (CC BY-NC-ND 4.0)
The commercial powders used to produce the coatings were sintered HA Captal®30 powder (Plasma Biotal Limited, U.K.) with crystallinity above 95% and a bioactive glass powder 45S5 (Denfotex Research, U.K.) manufactured by the usual melt-quenching method. Titanium G5 (Ibermetal, Spain) was used as the substrate material.
Following testing of each coating, the researchers drew several conclusions about the different strategies.
- Morphology. A notable increase in bond strength was observed with the agglomerated glass powder, which had lower density, higher porosity, and higher specific surfaces than the commercial glass powder. The researchers hypothesize that this improved strength is due to the agglomerated powders melting more quickly.
- Hydroxyapatite addition. A significant improvement in the bond strength was achieved with both the bilayer and blended hydroxyapatite coatings. The researchers attribute this improvement to the lower CTE mismatch between hydroxyapatite and the titanium alloy in contrast to the bioactive glass.
- Heat treatments. The researchers previously showed the benefits of heat treatments on adhesion strength in a 2021 paper. This study confirmed those earlier results, which they attribute to the formation of some crystalline phases within the coating.
In line with the ASTM regulations for calcium phosphate and metallic coatings, coatings adhered to dense metal substrates require a minimum adhesion strength of 22 MPa to be suitable for orthopedic applications. The bioactive glass coatings that met this requirement, listed below, were mainly heat-treated samples, with the blended coating being the only exception.
- Agglomerate with post-thermal treatment
- Bilayer with pre-surface heating
- Bilayer with post-thermal treatment
- Blended
- Blended with post-thermal treatment
The researchers conducted some additional tests to determine the coatings’ ability to stimulate bone regeneration and degradation behavior. Based on this information, the researchers determined that the blended coating—the only coating to achieve the required adhesion strength without heat treatment—is the most promising candidate to improve the osseointegration process of current implants.
The open-access paper, published in Surface and Coatings Technology, is “Improving the bond strength of bioactive glass coatings obtained by atmospheric plasma spraying” (DOI: 10.1016/j.surfcoat.2023.129837).
Author
Lisa McDonald
CTT Categories
- Biomaterials & Medical
- Glass