[Image above] Credit: Herr Olsen; Flickr CC BY-NC 2.0
Concrete—it’s pervasive. It’s under our feet on sidewalks, it makes up the world’s vast infrastructure network of roadways and buildings, and it can be quite beautiful.
Frankly, modern civilization wouldn’t exist without it.
The ancient Romans knew this. In fact, ancient Roman concrete is so strong and durable that the material has kept the Pantheon and the Colosseum intact thousands of years post-construction.
We’ve investigated the mysteries of ancient concrete before—specifically, how unique crystals prevent crack propagation and bestow strength to Roman concrete, and how scientists are looking to ancient technology to make modern concrete more durable and sustainable.
Earlier this year, we reported on research from Rice University in Houston, Texas, where scientists are working to reduce the impact that concrete manufacturing has on our environment.
Rouzbeh Shahsavari, theoretical physicist at Rice, and his team took an atomic-level look at the details of how concrete is produced. Based on the results of computer modeling studies, they found that dislocations—or screw-like defects—in raw crystals used for concrete could be the key to “greener” manufacturing processes.
Beyond more efficient concrete manufacturing, Shahsavari and his team also wanted to find out what it takes to make concrete stronger and tougher. And after analyzing more than 600 computer models of concrete’s inner matrix, they determined that “both voids and portlandite particles are significant players in giving the material its remarkable qualities,” according to a Rice press release this week.
Why go so deep into the concrete structural voids? Shahsavari and his team want provide new insights that will inform design guidelines and strategies to make the cement hydrate at the heart of concrete more tunable at a molecular level. Although concrete appears brittle, the team found that the material actually incorporates ductile fracture mechanisms at the nanoscale that help fortify it.
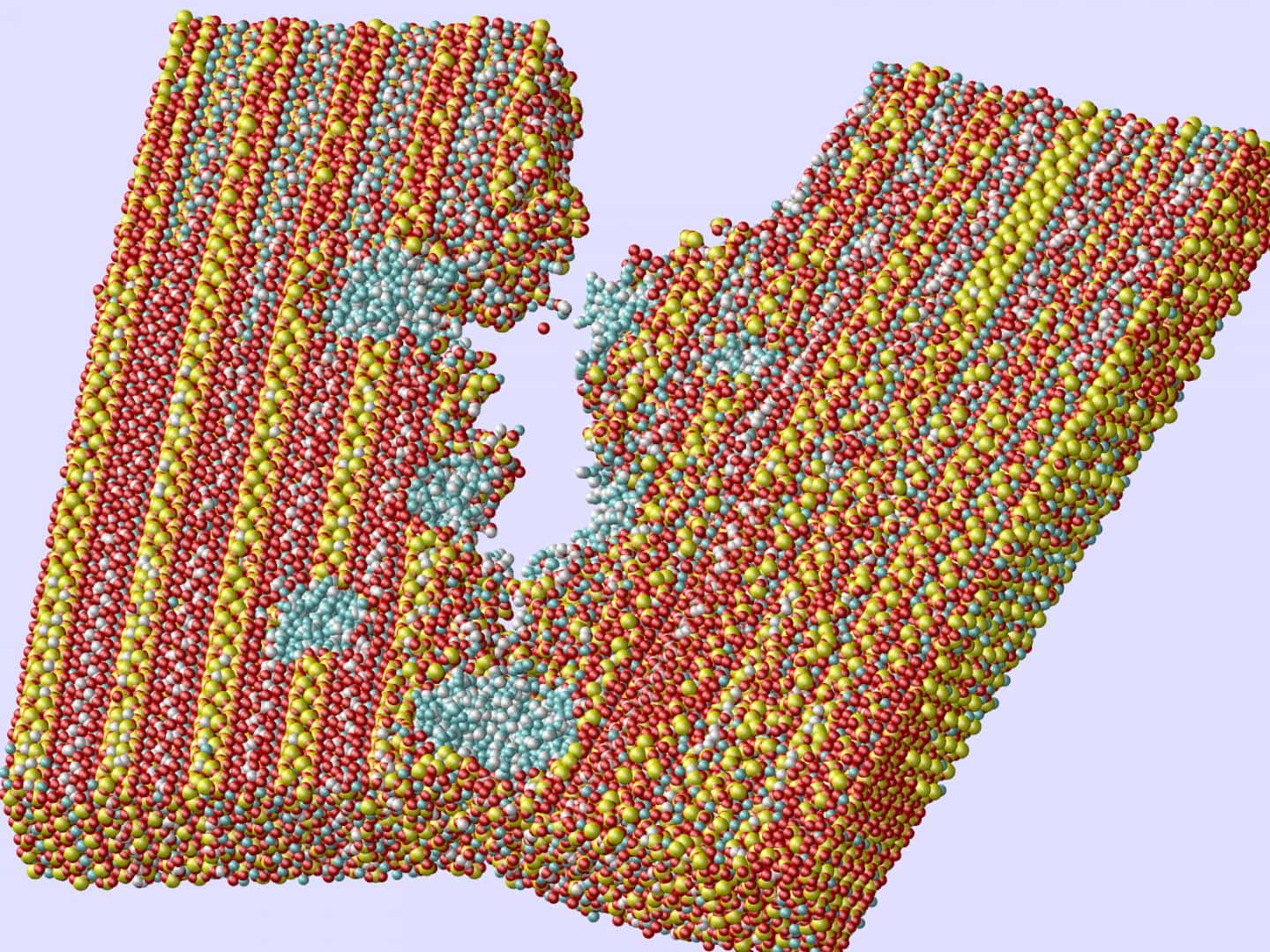
Rice University researchers used computer models of concrete’s inner matrix to show how tiny holes filled with portlandite (blue) impart strength and toughness by preventing the spread of cracks. Credit: Ning Zhang; Rice University
Cement hydrate, known as calcium-silicate-hydrate (C-S-H), “is the smallest building block in concrete, and we want to understand and control it to our advantage,” Shahsavari says in the release. “Modeling how its molecules interact helps us understand its nanoscale structure, defects, and fracture toughness. But this is very difficult to study through experiments alone because of the scale of the features we’re looking at.”
The team looked at how the interaction of either random air voids or random portlandite particles in C-S-H affect strength, stiffness, and toughness—specifically where voids meet crack formations.
“Besides C-S-H, portlandite is another product of cement hydration, but it forms in lower quantities compared with C-S-H and mainly exists as sort of inclusions or isolated islands surrounded by the C-S-H matrix,” Shahsavari explains. “Because portlandite has different crystalline features and mechanical properties than C-S-H, its presence and distribution can significantly impact the mechanics of C-S-H.”
The researchers used computerized molecular dynamics simulations to delve deep into how cracks form and found they tend to follow the path of least resistance—cracks turn in the direction of either the nanovoids or portlandite particles they encounter. The voids and particles sort of alter the geometry of the cracks as they propagate, which Shahsavari says likely contributes to concrete’s strength.
“When it comes to cement hydrate’s strength and toughness—properties that are typically exclusive in man-made materials—random voids and portlandite particles play a key role by regulating a series of competing deformation mechanisms, such as crack growth, crack deflection, voids coalescence, internal necking, accommodation, and geometry alteration of voids and particles,” Shahsavari says. “Our work decoded all such complex competing mechanisms.”
The team tested many variations of C-S-H—including C-S-H that’s more amorphous than crystalline, like tobermorite concrete—and found that the smaller the mean diameter of both voids and particles, the tougher the concrete overall.
More than 30 billion tons of concrete are used each year, and manufacturing it contributes up to 10% of the world’s carbon dioxide emissions. So anything that can be done to make the process more efficient—no matter how small it seems—is worth the effort, according to Shahsavari.
“Our findings could impact the modern engineering of durable concrete infrastructures and potentially other complex brittle materials,” Shahsavari says.
The research, published in the Journal of the Mechanics and Physics of Solids, is “Balancing strength and toughness of calcium-silicate-hydrate via random nanovoids and particle inclusions: atomistic modeling and statistical analysis” (DOI: 10.1016/j.jmps.2016.07.021).
Author
Stephanie Liverani
CTT Categories
- Basic Science
- Cement
- Construction
- Energy
- Environment
- Material Innovations
- Modeling & Simulation