[Image above] Partial refractory assembly for ingot casting of high alloy steel made by Steuler KCH in Höhr-Grentzhausen, Germany. The full setup has eight spokes that fill from the bottom to cast ingots. These are single-use assemblies. Credit: ACerS
Be careful what you ask for, because you just might get it!
In this case I had several invitations from members of the ceramics and glass industry in Germany to visit if ever I were in the area.
I was in Germany in late May, along with my ACerS colleague Mark Mecklenborg, for the first joint meeting of the DGG and ACerS Glass and Optical Materials Division. (I reported from the event here and here.) While we were there we took the opportunity to accept those invitations and learn more about manufacturing, education, and workforce development in Germany.
We visited six manufacturing plants, three post-secondary education institutions, and the European Center for Refractories, which also houses several research and contract entities.
Coincidentally, the Harvard Business Review published a blog post while we were in Germany titled, “Why Germany Dominates the U.S. in Innovation.” As an American touring German ceramic and glass manufacturers, I read it with interest.
“Innovation” gets a lot of attention these days. The premise of the HBR post by Dan Breznitz seems to be that in the United States, invention tends to be mistaken for innovation. He says in the post, “… Germany is better at adapting inventions to industry and spreading them throughout the business sector.” He also says, “Economic growth doesn’t happen at the moment of invention. Only innovation policies that target the complete innovation cycle will succeed in creating economic growth that enhances the welfare of all its citizens.”
Breznitz speculates three sources underlie Germany’s successful approach to innovation. Paraphrasing:
- Germany, by custom, requires that innovation beget widespread increases in productivity. New industries are great, but existing industries readily incorporate new ideas, too.
- Public institutions facilitate technology—“innovation doesn’t end with invention.” The Fraunhofer Institutes are the archetypal example.
- Germany constantly trains its workforce, which incubates and allows for rapid adoption of new ideas.
Our visits focused on the refractory and lighting industries—only a narrow slice of German industry. However, I’d say my observations align pretty well with Breznitz’ premises.
Our visit began in the Koblenz region in Rhineland-Palatinate, which comprises a unique ecosystem of ceramic industry, and specifically, the refractory industry. Our host was Dr. Peter Quirmbach, director of the European Centre for Refractories (ECREF) in nearby Höhr-Grenzhausen, as well as faculty at the University of Koblenz. He describes the ECREF as a “toolbox” for advancing industry, research, and education, and for providing services. ECREF houses the DIFK, which provides on-request testing services; the FGF—a contract research and innovation entity; and the German Refractories Association (DFFI). The ECREF was founded in 2009 to “shape science and innovation in Europe,” says Quirmbach.
The ECREF works closely with stakeholders at the global, European, national, state, and local level. We got a close-up look at the local level, where Quirmbach works with seven local partners to fashion an integrated educational system tailored to the specific needs of the refractory industry. He has a unique advantage—the German refractory industry is concentrated in the region, with 22 refractory companies in about a 100 km radius of ECREF. Not surprisingly, the German steel industry also is concentrated in this area, but more diffusely. That means students and education institutions are very near employers. Sometimes really close—one technical school we visited trains technicians/skilled workers and is directly across the road from a large 100-year-old refractory and tile manufacturer.
The local partnership is “The Ceramics Education and Research Centre” (German acronym, BFZK) and includes a university, polytechnic institute (B.S. and M.S. degrees in ceramic engineering), vocational and technical colleges for training skilled workers, an incubator for startup companies, and a ceramics museum. The educational institutions work closely with industry to design not only curricula that meet their needs, but also to coordinate with the workday. For example, The State Technical College for Ceramics Technology and Ceramics Design has designed a modular approach where students—who are already employed in local plants—take course “modules” in the morning and work in the afternoon. At the university or polytechnic level, all B.S. students must complete a semester-long practicum in industry.
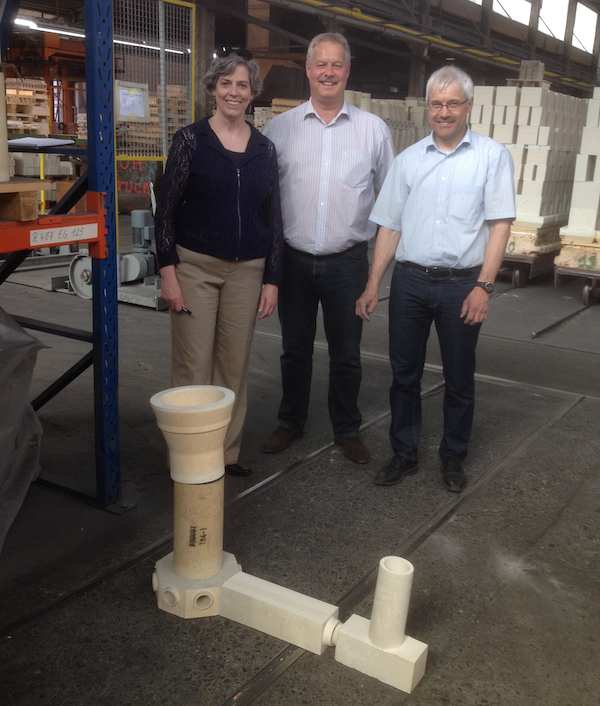
At the Steuler refractory plant in Höhr-Grentzhausen, Germany. From left: Eileen De Guire (ACerS), Peter Quirmbach ECREF), Peter Leukel (Steuler KCH). Credit: ACerS
One of Germany’s strategies is to compete on quality and efficiency—a strong tradition in that country. Some plants we saw were highly automated. We visited a glass plant, for example, that runs two glass tanks 24/7 with only 22 people. Even the forklifts are robotic. In contrast, several of the refractory companies we visited make products that are very labor intensive. Purging plugs are critical components for steelmaking, but laborious to cast properly. However, a plug failure becomes catastrophic and possibly fatal quickly. You want the best quality. Similarly, family-owned Steuler KCH makes only specialty refractories, many by ramming individually. The company has more than 8,000 molds in its collection, most of which are also hand-built.
Knöllinger GmbH is also a privately held refractory manufacturer, but much younger than Steuler. Founded in 1996, it exclusively serves the steel and iron industry in Germany. It sees itself as an innovator and uses the FGF housed at ECREF to conduct its R&D activities. They know their innovative slide gates have found their mark because large refractory companies are scrambling to imitate the new design. The two managing directors, Marcus Blumenberg and Peter Stein, see their smallness, and geographic and industry focus as their competitive advantage. Blumenberg says, “Our customers are all in Germany. If anything unexpected happens at a plant, we want to be able to respond right away.”
We also stopped in at RHI in Urmitz to see how refractories are made at a large, multinational company. Specialty refractories for the steel industry are a tough business because their manufacture is still so labor intensive. To avoid holding inventory, the company only manufactures to order, and provides some additional assembly of parts. Also, as a large company, they have the ability to offer a wide range of products for the steel industry. They are doing some interesting work at their R&D facility in Vienna on laser systems for characterizing compositions of recycled sources of raw materials—things like whiteware sinks and toilets.
Like “fun” in the Army, sometimes innovation is forced. That is the case with lighting in Europe as well as in the U.S., where legislation stipulates efficiency requirements and has spurred research into solid-state lighting. A leap in lighting technology occurred in 1994 when a high bright blue phosphor was discovered, but with a pitiful external quantum efficiency of 2.7 percent at room temperature. Companies like Osram have invested heavily in developing phosphor technology and manufacturing processes for solid-state lighting. As a result, the blue phosphor external quantum efficiency is now 50–60 percent, high enough to be commercially useful. Osram is designing some interesting approaches to manufacturing solid-state lighting, too, with an eye on efficiency, agility, and of course, quality.
Besides conducting in-house research, companies have close relationships with their local research universities. Corporate support for university research seems to be stronger than it is in the U.S., and students often conduct some of their work at corporate facilities. For example, Technische Universität Ilmenau graduate student Pascal Rabenbauer is collaborating with Osram’s glass technology development team in Augsburg. Rabenbaur presented his work in a poster at DGG-GOMD, “Development of high refractive glass solders.”
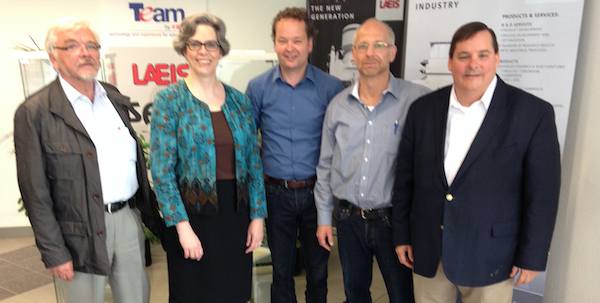
Alpha Ceramics in Aachen, Germany. From left: Alfred Kaiser (Laeis GmbH), Eileen De Guire, Roel van Loo and Robert Kremet (Alpha Ceramics), and Mark Mecklenborg (ACerS). Credit: ACerS
Along similar lines, Aachen-based Alpha Ceramics specializes in refractory design and development work, and they work closely with Aachen University (RWTH), which is only a few kilometers away. A subsidiary of industrial press manufacturer Laeis GmbH, they work with clients to “transfer scientific results into industrial processes,” according to Robert Kremer, ceramic engineer. They work with clients to develop refractory products, and related production processes, including machine and plant design, and can produce small production runs. “This provides the possibility to supply products for a limited time, for example, for testing the market acceptance or to bridge the time until a production plant can be put into operation,” Kremer says.
We also visited the University of Cologne and the research group of ACerS member (and Fellow-elect), Sanjay Mathur. Mathur supervises a substantial research group of 40 postdoctoral researchers, graduate, and undergraduate students. Similarly, he has close connections with local companies, some of which are in nearby Chempark.
Finally, we learned that because the ceramic and glass industry is “small,” relative to steel or automotive, employers know they need to have a global view when looking for qualified talent. Several times we were told, “We want the best people we can find,” regardless of where they come from.
Author
Eileen De Guire
CTT Categories
- Glass
- Manufacturing
- Refractories