[Image above] Steel protection is a riveting topic. Credit: Angelo Andiario; Flickr CC BY-ND 2.0
While we love ceramics and glass, there’s just no denying it—steel is one of the most important materials to modern living.
So this is big—researchers at Harvard University’s John A. Paulson School of Engineering and Applied Sciences have devised a way to improve the ubiquitous steel by protecting its surface from fouling and corrosion.
While there are varying grades of steel today, the surface has remained largely unchanged—meaning that steel is still rather susceptible to corrosion and abrasion.
Both disrupt the mechanical stability of steel, among other materials, and have a huge economic impact. According to the Wikipedia page on fouling, “one estimate puts the losses due to fouling of heat exchangers in industrialized nations to be about 0.25% of their GDP. Another analysis estimated (for 2006) the economical loss due to boiler and turbine fouling in China utilities at 4.68 billion dollars, which is about 0.169% of the country’s GDP.”
And that’s only considering heat exchangers. So helping to prevent fouling and corrosion is a big business.
But before you get too excited, metalheads, do you want to guess who’s the secret steel savior?
That’s right—ceramics.
Harvard researchers have developed a scalable technique to give steel a metal oxide coating to prevent liquids from sticking to its susceptible surface.
The new coating, a rough nanoporous tungsten oxide layer, “is the most durable anti-fouling and anti-corrosive material to date, capable of repelling any kind of liquid even after sustaining intense structural abuse,” according to a Harvard press release.
You may already be familiar with the coating as SLIPS, or Slippery Liquid-Infused Porous Surfaces, which was developed in the lab of Joanna Aizenberg back in 2011.
Since then, the team has figured out ways to apply the SLIPS coating to a variety of surfaces for an even wider variety of purposes. Steel is the latest, and perhaps biggest potential market in terms of sheer magnitude.
“Our slippery steel is orders of magnitude more durable than any anti-fouling material that has been developed before,” Aizenberg says in the press release. “So far, these two concepts—mechanical durability and anti-fouling—were at odds with each other. We need surfaces to be textured and porous to impart fouling resistance, but rough nanostructured coatings are intrinsically weaker than their bulk analogs. This research shows that careful surface engineering allows the design of a material capable of performing multiple, even conflicting, functions, without performance degradation.”
To prevent performance degradation, aka mechanical instability, the team applied the tungsten oxide coating with electrochemical deposition. Instead of creating an even coating, the method grew tiny islands of the metal oxide floating on steel’s surface.
While that may sound like a weakness for the coating, one of the researchers points out just how valuable those islands are.
“If one part of an island is destroyed, the damage doesn’t propagate to other parts of the surface because of the lack of interconnectivity between neighboring islands,” Alexander B. Tesler—former postdoctoral fellow at SEAS, current research fellow at Weizmann Institute of Science in Israel, and the paper’s first author—says in the press release. “This island-like morphology combined with the inherent durability and roughness of the tungsten oxide allows the surface to keep its repellent properties in highly abrasive applications, which was impossible until now.”
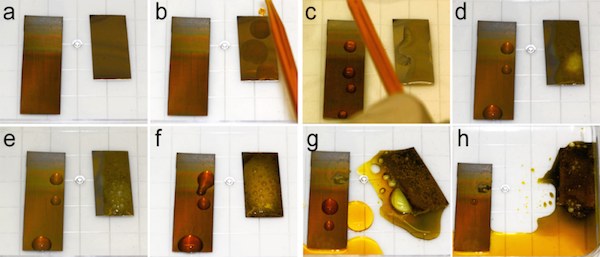
Accelerated corrosion test, in which unmodified stainless steel (300 grade) (right sample) and the lower part of the TO-SLIPS sample with a 600-nm-thick porous TO film on steel (left sample) were exposed to very corrosive Glyceregia stainless steel etchant. (a–h) Images show corrosion evolution as a function of contact time. Credit: Harvard SEAS
The benefit of electrochemical deposition is that the technique is already used in steel manufacturing, so implementation and scaling will be feasible. In addition, the coating is durable.
“The team tested the material by scratching it with stainless steel tweezers, screwdrivers, diamond-tipped scribers, and pummeling it with hundreds of thousands of hard, heavy beads,” according to the release. “Then, the team tested its anti-wetting properties with a wide variety of liquids, including water, oil, highly corrosive media, biological fluids containing bacteria and blood. Not only did the material repel all the liquid and show anti-biofouling behavior but the tungsten oxide actually made the steel stronger than steel without the coating.”
The SLIPS technology has helped launched spin-off company SLIPS Technologies Inc., which thinks that one of the most promising applications is for steel medical devices that prevent growth of microorganisms of their surfaces.
Another potential market is ships and structures near oceans and waterways, which have a big problem with biofouling—think barnacles and algae.
But with all the uses of steel, just imagine the possibilities.
“This research is an example of hard core, classic material science,” Aizenberg says in the release. “We took a material that changed the world and asked, how can we make it better?”
The open-access paper, published in Nature Communications, is “Extremely durable biofouling-resistant metallic surfaces based on electrodeposited nanoporous tungstite films on steel” (DOI: 10.1038/ncomms9649).
Author
April Gocha
CTT Categories
- Construction
- Environment
- Material Innovations
- Nanomaterials
- Transportation