[Image above] Scanning electron microscope images of a hollow tube aluminum oxide nanolattice. The nanolattice shown here is designed with an octet-truss geometry and has characteristic length scales spanning over three orders of magnitude from 50 µm (full structure) to 10 nm (tube wall thickness). Credit: Lucas Meza; Caltech
We at the American Ceramic Society are pretty fond of ceramics—I mean, they are our material—but, as with any healthy relationship, we also recognize that ceramics aren’t perfect.
Ceramics don’t exactly earn high marks on their report card when it comes to elasticity. Their brittleness is actually a limiting factor for many applications (and the topic for one of ACerS’s ceramics short courses and award lectures at MS&T14 next month)—but new research suggests that ceramics don’t have to be brittle.
Imagine the possibilities if you could have the best of both worlds—the hardness, inertness, and toughness of ceramics combined with the elasticity of more resilient materials. Researchers from California Institute of Technology say that it’s more than possible—they report in the latest issue of Science the fabrication of incredibly light alumina nanostructures that are 99.9% air and can bend and deform with the best of them, springing back to shape after compressions of over 50% strain.
“Combining the concepts of architecture and nanomaterials allows us to generate a completely new class of materials,” senior author and Caltech professor of materials science and mechanics Julia Greer says in a phone interview. “Ceramics have always been thought to be heavy and brittle. We’re showing that in fact, they don’t have to be either. This very clearly demonstrates that if you use the concept of the nanoscale to create structures and then use those nanostructures like LEGO to construct larger materials, you can obtain nearly any set of properties you want. You can create materials by design,” she says in a Caltech press release.
To make the ceramic structures, the group first designed polymer skeletons composed of octet-truss unit cells using two-photon lithography direct laser writing. Each unit cell is like a cube filled with little criss-crossing beams for maximum architectural strength and stability. The scientists coated the polymer with alumina using atomic layer deposition, milled it with a focused ion beam, and then nixed the internal polymer with O2 plasma—leaving just an air-encased network of hollow alumina tubes, 450–1,380 nm in diameter with walls just 5–60 nm thick.
The structures are “essentially a 3D nanostructure wrapped in a 2D nanoribbon,” Greer says by phone. This structure allows the material to be lightweight and have interesting size effects, which differ depending on the properties of the nanomaterial used for the nanoribbon. “Ceramics often become tougher,” she says.
[If this is sounding familiar, the process is similar to research we reported on earlier this year from Karlsruhe Institute of Techonolgy.]
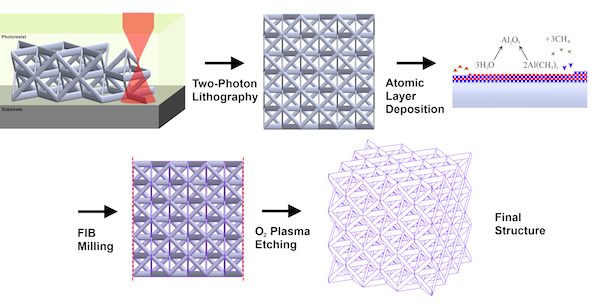
Schematic showing the fabrication process for hollow ceramic nanolattices. The nanolattices are first written out of a photopolymer using two-photon lithography direct laser writing. The polymer scaffolds are coated using atomic layer deposition (ALD) and the underlying polymer is exposed to air using focused ion beam milling. The polymer is then removed using O2 plasma etching, leaving behind a hollow ceramic nanolattice. Credit: Lucas Meza; Caltech
The team then put their miniscule structures to the test, squishing them with a nanoindenter to see just how well they did under pressure—would they stand tall, or crumble apart?

Clockwise, from left to right: an alumina nanolattice before compression, during compression, fully compressed, and recovered following compression. Credit: Lucas Meza; Caltech
Depending on the size of the alumina nanotubes, some did indeed crumble, while others fared surprisingly well. The scientists found that tube diameter to wall thickness ratio was key—tubes with a thickness of 50 nm and a diameter of 1 um shattered, while those with a thinner wall of just 10 nm showed something new.
“You deform it, and all of a sudden, it springs back,” Greer says in the release. “In some cases, we were able to deform these samples by as much as 85 percent, and they could still recover.”
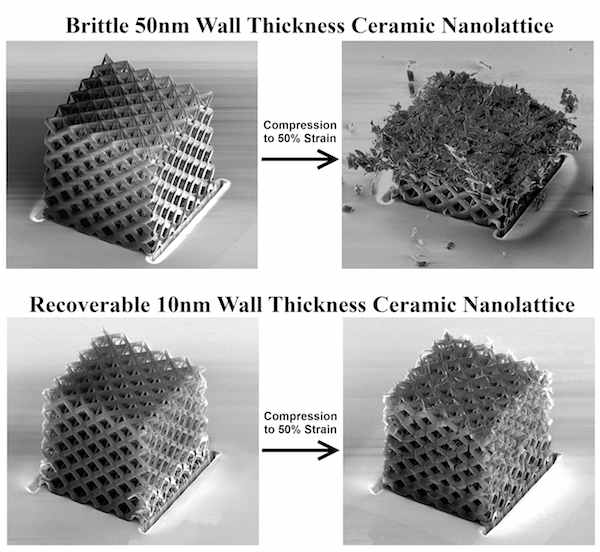
Scanning electron microscope images illustrating a brittle-to-recoverable transition in hollow ceramic nanolattices. Both samples shown are made from the same material with identical structural parameters and processing conditions. For the nanolattice with a 60 nm wall thickness, failure occurs in a catastrophic brittle manner and exhibits no recovery, as would be expected for a ceramic material. When the wall thickness is reduced to 10 nm, the deformation becomes ductile-like and the structures are able to almost completely recover their initial shape. Credit: Lucas Meza; Caltech
And, according to the paper, structures composed of small unit cells recovered from strain the best, bouncing back to 95% of their original height. The technique “effectively tricks the material into having new properties,” Greer says by phone. Once scaled up, the nanostructures could be patterned into larger sheets, which then could be laminated together to fabricate incredibly lightweight yet strong bricks, she says.
Flaws in a material are usually points of failure, especially in brittle materials like ceramics and glass. So, the team speculates, the decreased number and ratio of flaws in the small amount of material in the nanostructures may help to prevent failure of the structure overall.
Since other materials could be applied to the polymer skeletons, the technique has a wide range of possible applications, including those in optics, energy, and biomedicine, among others. According to Greer, there are so many applications—from lightweight components for the aeronautic industry to biomedical implants made of airy biocompatible materials that cells can infiltrate, an avenue that the team is actively pursing through collaborations with the University of California, San Francisco and City of Hope Medical Center, Greer says. The materials could also have many applications for energy, such as in stable yet lightweight electrodes.
The main roadblock, which the team is aggressively pursing now, is scalability of the technology, Greer says.
The paper is “Strong, lightweight, and recoverable three-dimensional ceramic nanolattices” (DOI: 10.1126/science.1255908).
Author
April Gocha
CTT Categories
- Material Innovations
- Nanomaterials