[Image above] CAD model and printing of zirconia gear using organic sacrificial supports. Credit: Li et al., International Journal of Applied Ceramic Technology
Additive manufacturing (AM) is an extremely popular fabrication process across all of materials science. AM produces parts by building three-dimensional structures layer-by-layer, typically using x-y control of a nozzle or laser light with a z-axis stage. In contrast, subtractive manufacturing involves removing material from pre-forms to achieve the final part, often by computer numerical control machining.
There are many different technologies for additive manufacturing. The most common include laser sintering from powders (typical for metals and being explored for ceramics), fused-filament fabrication of polymers, and room-temperature deposition of pastes or slurries for ceramics. This latter method has been used to fabricate concrete houses cheaply and quickly, as reported in earlier CTT posts.
The suite of techniques that comprise AM provide the promise of producing complicated internal structures that cannot be achieved by subtractive manufacturing or other traditional techniques, such as slip casting (ceramics) or sand casting (metals). However, designing complex shapes with large-sized unsupported regions can be challenging.
This challenge is resolved by including removable support structures in the layer build-up process. For laser sintering, the powder base provides the support. For fused-filament fabrication (FFF), a second dissolvable polymer is often employed to create lattice-like support structures.
With ceramics, the pastes or slurries are deposited at room temperature and then thermally post-processed. This sequence creates many challenges for fabricating ceramic shapes with large unsupported areas. In particular, the slurries are formulated with binders and viscosity control materials that are temperature sensitive. Support materials cannot affect the past/slurry viscosity to maintain the integrity of the print. Additionally, the pastes/slurries must be kept at a constant humidity level throughout the printing phase to prevent cracking.
Solutions to these challenges are explored by researchers at the Missouri University of Science and Technology and San Diego State University in a recent paper published in the International Journal of Applied Ceramic Technology.
The researchers apply secondary support materials, as is done with FFF. They found that typical polymers used for FFF supports cannot be used with ceramics because the high temperatures needed to melt polymeric filaments reduce the viscosity of the slurries. At high temperatures, the reduced viscosity causes the part to slump before the thermal post processing.
Instead, the researchers experimented with materials that are applied at lower temperatures yet melt or disintegrate during the thermal processing steps. Their choices of very common commercially available organic materials for this purpose impresses me—polycaprolactone, with a low melting point of 60˚C, is used by hobbyists for sculpture or prototype modeling; silicone paste is common as a household sealant; and petrolatum, which is better known as petroleum jelly or Vaseline. Using low-cost materials reduces a barrier to commercialization.
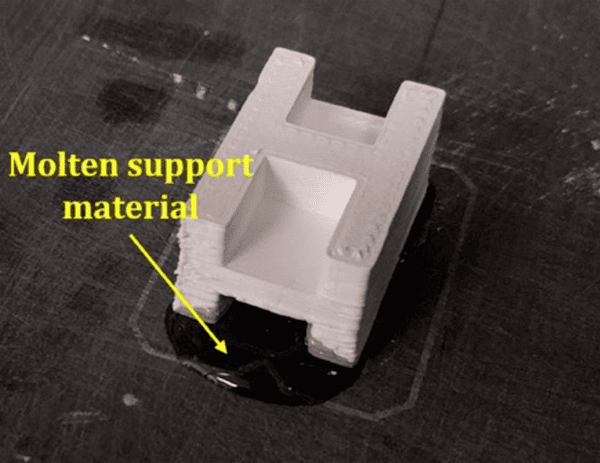
Double-H test part and substrate heated on hot plate to melt polycaprolactone support before sintering. Credit: Li et al., International Journal of Applied Ceramic Technology
Their results show a ranking among the three materials, with petrolatum being the best overall and silicone the worst—read the full article to find out why.
Another of their findings is very encouraging for using AM in medium- to large-scale production of ceramic parts. Using their composition of 52 volume% 3YSZ in an aqueous slurry, they achieved reproducible and anisotropic shrinkage upon firing, with low surface roughness. These qualities are important for scale-up as they can lead to net-shape or near net-shape production with little to no processing after sintering.
One final note. This article was reviewed and published under the ACT “Fast Track” process. The editors of ACT select manuscripts on important topics that are well researched and well-written for Fast Track. These articles are then given special attention to substantially shorten publishing time, so the information gets to our readers quicker.
The paper, published in International Journal of Applied Ceramic Technology, is “Additive manufacturing of zirconia parts with organic sacrificial supports” (DOI: 10.1111/ijac.13520).
Author
Jonathon Foreman
CTT Categories
- Manufacturing