[Image above] Microscope image of drilled holes in sodalime glass using a GHz-burst mode femtosecond laser. The drilling parameters were 1,000 bursts containing 50 pulses, burst fluence of 136 J/cm2, and interburst repetition rate of 10 kHz for drilling times from 10 ms to 100 ms in steps of 10 ms (from left to right in image). The spot size was 9.3 µm and the effective numerical aperture equaled 0.10. The red dashed line indicates the front surface of the sample. Credit: Lopez et al., Optics Express (CC BY 4.0)
When I attended Ceramics Expo in 2019, it was my first time attending a trade show that did not involve agriculture or horses (the fun of growing up in Iowa!). As my seasoned colleague took me around the show floor, explaining the types of exhibitors who attend such a ceramics-focused event, the device that most caught my attention was an industrial water jet cutter.
Water is not the first material I would think of for machining parts. In typical everyday usage—such as washing dishes or taking a shower—water flows around objects, not through them.
However, as any geologist knows, water can be a powerful force that has shaped and changed the landscape for millennia.
By pressurizing a stream of water (which may or may not contain an abrasive substance), manufacturers can greatly accelerate the natural erosion process. They can then use this high-speed water jet to shape materials, particularly ones that may be too brittle, thin, or heat-sensitive to withstand traditional machining methods.
Similarly, lasers are another machining technology that may surprise some people. Like water, the lasers commonly used at home—such as for cat toys and dance parties—are not going to cut holes in the walls. But if you greatly increase the wattage of a laser, it now has the energy to burn, melt, or vaporize various materials.
Though water and laser machining may sound like recent concepts, both technologies have been around a relatively long time. The earliest form of water jet cutting can be traced to the 1850s for mining purposes (though more advanced applications are attributable to paper companies in the 1930s). Likewise, within a decade of the first working laser being built in 1960, companies had developed laser-based cutting machines and were producing them at a rapid rate by the mid-1970s.
Femtosecond lasers: Development and burst-mode modification
The development of femtosecond lasers in the early 1990s was a breakthrough that the surgical field of ophthalmology rapidly adopted; however, the technology quickly impacted the industrial machining world as well.
Femtosecond lasers are ones that emit ultrashort optical pulses with a duration in the range of 10–15 seconds. Over these extremely short timescales, the laser–material interactions take on some unique features that can be beneficially exploited.
For example, the short duration of each individual pulse allows no time for heat to dissipate through thermal conduction. Additionally, while each pulse contains a low amount of energy (typically 10–15 μJ), the ultrafast pulse rate and focused strike spot result in enormous energy densities, typically in the order of megawatts of peak power and GW/cm2 in intensity. Together, these effects result in a highly concentrated thermal gradient.
Femtosecond lasers have led to great advances in micromachining capabilities, including for glass technologies. For example, femtosecond laser direct writing is an acknowledged technique for producing waveguides in transparent glass. Femtosecond lasers also are advancing the emerging field of dissimilar material welding, e.g., glass and metal.
Recently, a modification of femtosecond micromachining called “burst mode” is attracting much attention. Rather than releasing single pulses at a fixed repetition rate, burst-mode lasers will emit bursts (or groups) of pulses at a fixed repetition rate.
Compared to single pulses, the energy of each individual pulse within a burst is smaller. Thus, the peak fluence of each pulse (i.e., energy delivered per unit) can be nearer the optimum value, thereby increasing the removal rate.
So far, most burst-mode laser studies have involved metals and silicon. But a recent open-access review study predicted there is significant potential for burst-mode micromachining in dielectric (electrically insulating) materials, such as glass.
Exploring the potential of burst-mode femtoseconds lasers for drilling glass
Last year, researchers in France decided to explore this potential. Their resulting open-access papers, published in April and December, provide a first look at using femtosecond laser GHz-bursts to conduct top-down percussion drilling in different glasses.
The researchers come from the University of Bordeaux and laser equipment supplier Amplitude Systems. In their first open-access paper, they investigated the interaction dynamics of a GHz-burst mode femtosecond laser beam with several types of glass during the drilling process.
They used an ytterbium-doped femtosecond laser system emitting 500-femtosecond pulses at 1,030 nm. The intraburst repetition rate was set to 1 GHz containing 50 pulses within the burst (resulting in a burst length of 50 nanoseconds), and the interburst repetition rate was variable between 5 Hz and 200 kHz. Drilling was performed on sodalime, alkali-free alumina-borosilicate, and fused silica glass, as well as sapphire.
Using time-resolved shadowgraphs and thermal imaging, they found that single-pulse and GHz-burst percussion drilling removed material in fundamentally different ways, leading to substantially different hole morphologies. In single-pulse drilling, matter was continuously ejected, leading to conical holes with a rough internal surface. In contrast, GHz-burst mode ejected matter in a discontinuous way, resulting in quasicylindrical holes with a smooth internal surface.
However, for both single-pulse and GHz-burst modes, “The detrimental heat accumulation effects for increasing repetition rates are clearly limiting the drilling rates that can be applied,” the researchers note. But in GHz-burst mode, “drilling rates of tens to hundreds of holes per second are accessible depending on the fluence and the drilling depth that may exceed 300 µm,” they add.
Of the materials tested, fused silica glass showed the best resistance to heating provoked at high interburst repetition rates with no effect on the drilling quality between 100 and 200 kHz.
“This is in agreement with our observation that fused silica is the glass with the highest ablation threshold in GHz-burst regime,” the researchers write. Ultimately, the study demonstrated the potential of GHz-burst drilling to produce holes with very high surface qualities and aspect ratios. It also allowed the researchers to confirm the thermal character of the interaction between GHz-burst pulses and the materials that leads to heat accumulation, which must be accounted for when choosing the drilling parameters.
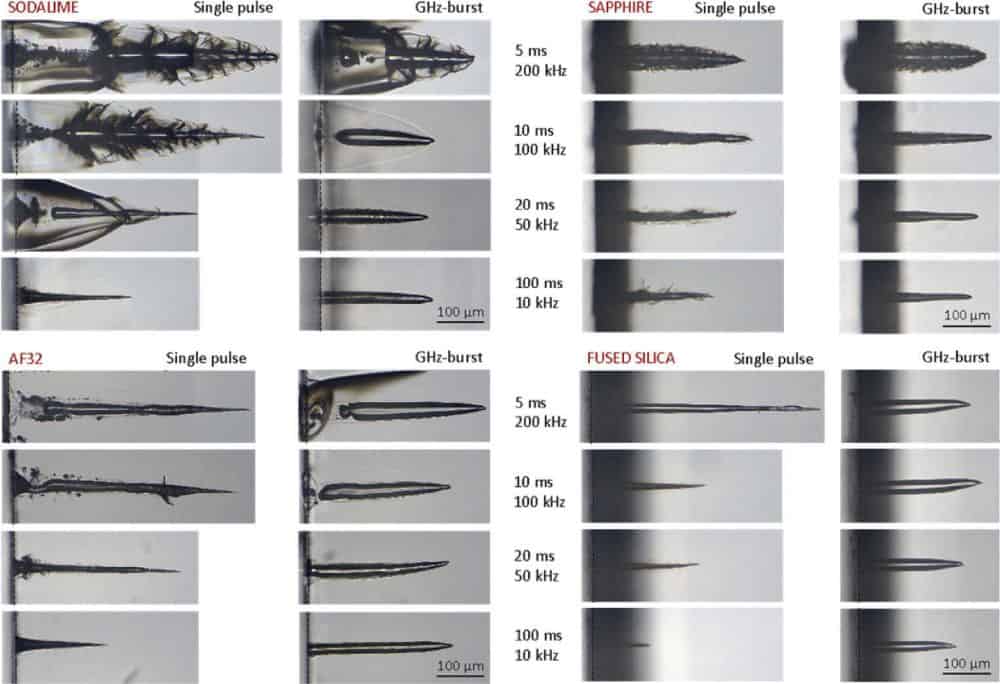
Microscope images of drilled holes for four different repetition rates (10 kHz, 50 kHz, 100 kHz, and 200 kHz) in four different materials (sodalime, sapphire, alkali-free alumina-borosilicate [AF32], and fused silica). The images on the left side correspond to single pulse drilling and on the right side to GHz-burst drilling with 50 pulses at an intraburst repetition rate of 1 GHz, respectively. The drilling time corresponds to 1,000 single pulses (fluence of 289 J/cm2 per pulse) or 1,000 GHz-bursts (fluence of 300 J/cm2 per burst), respectively. Credit: Lopez et al., Optics Express (CC BY 4.0)
In their second open-access paper, the researchers further explored using a GHz-burst femtosecond laser to perform top-down percussion drilling in sodalime and fused silica glass.
They again used an ytterbium-doped femtosecond laser system emitting 500-femtosecond pulses at 1,030 nm. The intraburst repetition rate was set to 1 GHz containing 50 pulses within the burst (resulting in a burst length of 50 nanoseconds). Meanwhile, the interburst repetition rate was set to 1 kHz to avoid the appearance of any heat-affected zone around the holes (per what was learned in the first study).
Analysis of the drilling process in sodalime and fused silica glass revealed three stages in hole formation.
- The first stage corresponds to surface ablation. The ablation plume can expand freely in the ambient air above the target, and the drilling rate is high.
- The second stage corresponds to deep ablation. The ablation plume is confined by the inner walls, leading to a decrease in ablation efficiency and a lower drilling rate (0.70 µm/burst for surface ablation versus 0.15 µm/burst for deep ablation).
- In the third stage, the drilling process is over as the fluence value at the hole bottom is below the ablation threshold.
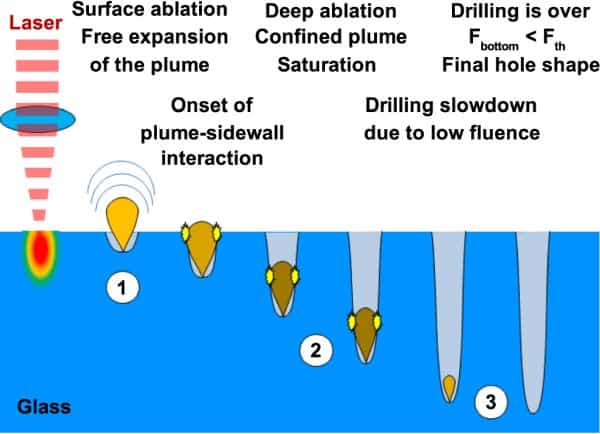
Schematic view of the three stages in hole formation. Credit: Balage et al., International Journal of Extreme Manufacturing (CC BY 4.0)
Similarly to hole length, the burst fluence and number of bursts influenced the size of the hole’s diameter. When drilling begins, the diameter increases rapidly with increasing burst number. Later, it reaches a saturation value that increases with the burst fluence.
Interestingly, the effect of fluence on inner hole surface quality differed for sodalime and fused silica glass. While increasing fluence decreased the quality of the sodalime’s inner hole surface, neither fluence nor burst number affected the quality of the fused silica’s inner hole surface.
This difference in fluence’s effect on surface quality helped explain why the researchers measured similar hole lengths in sodalime and fused silica glass even though fused silica has a higher ablation threshold, as explained below.
“The difference of the inner surface quality induces different scattering losses of the beam during the drilling process in these two materials,” the researchers write. “The glossy surface of fused silica allows for low-loss reflections and therefore a more efficient beam transmission towards the tip of the hole increasing its depth. This results in a compensation for the larger energy amount needed for drilling due to the higher ablation threshold of this material. This is the reason why we measure similar lengths in sodalime and in fused silica.”
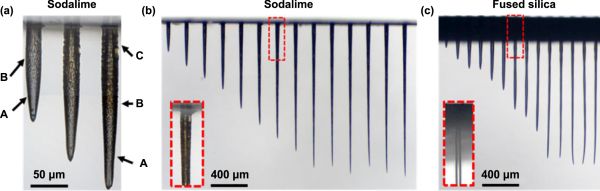
(a) Evolution of the inner surface of the holes in sodalime at a burst fluence of 270 J/cm2 for drilling times of 800 ms, 900 ms, and 1,000 ms. (b,c) Microscope images of the holes for burst fluences of 270 J/cm2 and a zoom of the entry point for a drilling time of 7 seconds in (b) sodalime and (c) fused silica, respectively. Credit: Balage et al., International Journal of Extreme Manufacturing (CC BY 4.0)
Based on this knowledge, the researchers optimized the drilling conditions and reached aspect ratios up to 37 in sodalime and 73 in fused silica.
“These impressive results of percussion drilling in femtosecond laser GHz-burst mode allowing for extreme hole geometries may pave the way for future applications in photonics devices or microelectronics,” they conclude.
The first open-access paper, published in Optics Express, is “Percussion drilling in glasses and process dynamics with femtosecond laser GHz-bursts” (DOI: 10.1364/OE.455553).
The second open-access paper, published in International Journal of Extreme Manufacturing, is “Crack-free high-aspect ratio holes in glasses by top-down percussion drilling with infrared femtosecond laser GHz-bursts” (DOI: 10.1088/2631-7990/acaa14).
Update 01/28/2023 – The original version of this article inadvertently featured an image of an OptiPro OptiSonic 550X ultrasonic machining center rather than a water jet cutter. This image has been removed for clarity.
Author
Lisa McDonald
CTT Categories
- Glass
- Manufacturing