[Image above] Example of an injection molded transparent ceramic shaped like a gear. Scale bar: 5 mm. Credit: Mader et al., Advanced Science (CC BY 4.0)
Ever since the 1990s discovery that properly aligned polycrystalline ceramics can be optically transparent, so-called “transparent ceramics” now are a mainstay in many commercial lasers.
Achieving the perfect positioning of crystals to allow for optical transparency, however, is easier said than done. The excellent mechanical, thermal, and chemical stability of ceramics makes structuring them inherently challenging.
Currently, fabrication of transparent ceramics, such as magnesium aluminate spinel, typically involves casting powders from water-based solutions or pressing raw powders followed by a sintering process. This approach, however, only produces simple geometries; more complex structures require time-consuming post-processing steps such as grinding, polishing, or etching.
Some studies on additive manufacturing of transparent ceramics have taken place, but these methods are not suited for mass-market manufacturing.
Powder injection molding is a well-known method for manufacturing small, complex-shaped inorganic components that could benefit fabrication of transparent ceramics. It involves mixing metal or ceramic powders with polymeric binders and then pushing the heated mixture under pressure into a die cavity, where it cools and is subsequently ejected. The composite then undergoes heat treatments to remove the polymeric binder and achieve final density.
In a recent open-access paper, German researchers showed that transparent magnesium aluminate spinel ceramics can be shaped and structured using conventional injection molding machinery.
The researchers come from Albert Ludwig University of Freiburg and include colleagues from Karlsruhe Institute of Technology. In their paper, they describe using a two-step debinding process followed by sintering and hot isostatic pressing to fully densify their transparent ceramics. Notably, no sintering aids were used because “it has been shown repeatedly” that dopants can affect the final properties of a transparent ceramic, they write.
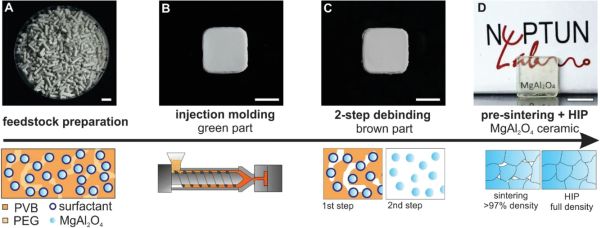
Injection molding of transparent magnesium aluminate spinel ceramics. Scale bar: 10 mm. Credit: Mader et al., Advanced Science (CC BY 4.0)
Without further post-processing steps, the magnesium aluminate spinel ceramics achieved high optical transmissions of up to 84% and high surface quality with a roughness of less than 20 nm. Additionally, the researchers could create the ceramics in a variety of sizes, from macroscopic components with wall thicknesses up to 4 mm down to microstructured components with single micrometer resolution.
“This work paves the way to a large number of novel applications … such as functional cover windows for consumer electronics … that were previously inaccessible or too expensive on a larger scale due to the lack of suitable, high-throughput MAS [magnesium aluminate spinel] processing methods,” the researchers conclude.
The open-access paper, published in Advanced Science, is “Injection molding of magnesium aluminate spinel nanocomposites for high-throughput manufacturing of transparent ceramics” (DOI: 10.1002/advs.202204385).
Author
Lisa McDonald
CTT Categories
- Manufacturing
- Material Innovations