[Image above] High temperatures, wide temperature swings, corrosive and abrasive environments—how can steel producers protect equipment used in such harsh settings? Credit: Pixabay
There are few materials science problems more challenging than developing equipment for use in steel production. High temperatures and wide temperature swings, corrosive and abrasive environments, and the need for uninterrupted production with low operating costs are among the many issues faced by steel producers and equipment suppliers alike.
In particular, designing equipment for use in continuous casting of steel presents a major challenge. In this process, red-hot ingots are supported and transported by a series of rollers. Water-spray used to keep the roller mechanisms from over-heating creates thermal gradients and highly corrosive environments.
The most common roller structure has a martensitic stainless-steel cladding welded over a steel tube. The weld, with different chemical and crystal structure from the rest of the cladding, is vulnerable to both chemical attack and mechanical failure through cracking, spalling, and more.
Thermally sprayed ceramic coatings are beginning to displace welded cladding. Compared to steel cladding, ceramic coatings are harder (and thus more resistant to mechanical abrasion), more resilient against thermal cycling, and more chemically resistant.
For stainless-steel production, there exists advanced thermal barrier coatings (TBCs) that can withstand the higher production temperatures. High-temperature TBC materials consist of mixtures of zirconia, titania, chromium oxide, alumina, yttria, and zirconium silicates.
Ferrochromium (FeCr) slag, a waste product from the production of stainless steel, contains high levels of alumina, silica, and magnesium oxide, along with moderate levels of iron, chrome, and calcium oxides, and low levels of other oxides and silicates. This fact led researchers at Bartin University in Turkey to hypothesize that FeCr slag has the potential to be a zero-cost, environmentally friendly TBC for casting rollers. In their aptly-named article “Comparison of dry sliding wear behavior of plasma sprayed FeCr slag coating with Cr2O3 and Al2O3‐13TiO2 coatings,” they test the idea and—spoiler-alert—their findings support the hypothesis.
In their paper, the researchers used pin-on-disk wear testing, optical profilometry with image analysis, scanning electron microscopy with EDS, X-ray diffraction, and hardness testing to evaluate the coatings. I mention the whole suite of testing because their work provides a thorough picture of the materials, their performance, and underlying explanations, and it is an excellent example of the high-quality work published in International Journal of Applied Ceramic Technology (ACT).
The researchers used these tools to show the FeCr slag is more resilient against wear than the other two commercial coating materials despite, or perhaps because, the ferrochromium slag has the lowest hardness value. Through extensive use of electron microscopy, they show the FeCr slag exhibits a lower degree of spalling than the alumina-titania coating.
Wear patterns in the chromia coating show jagged and easily broken structures in the wear pattern whereas the FeCr slag has rounded, sturdier patterns. In addition, the FeCr slag develops a smooth sliding surface, what the researchers term “tribolayer,” at a higher rate than the other two materials. This combination of factors minimizes wear of the FeCr slag.
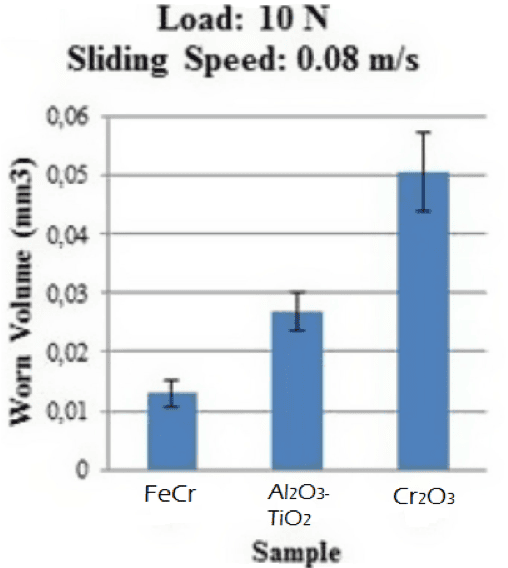
This work is interesting and important and provides an excellent picture of the potential for FeCr slag as a wear coating. I look forward to reading articles on the other factors needed to qualify FeCr slag for continuous casting roller coatings, including resistance to harsh chemical and thermal environments.
The paper, published in International Journal of Applied Ceramic Technology, is “Comparison of dry sliding wear behavior of plasma sprayed FeCr slag coating with Cr2O3 and Al2O3‐13TiO2 coatings” (DOI: 10.1111/ijac.13273).
Author
Jonathon Foreman
CTT Categories
- Environment
- Manufacturing
- Refractories