[Image above] Images (A, C, E) after and (B, D, F) during flash sintering of copper oxide samples with varying applied power densities. The sample with the lowest applied power density (A, B) has a homogeneous orange glow, while the two samples with higher applied power densities (C–F) break during the flash event due to the development of hot spots. Credit: Murray et al., Journal of the American Ceramic Society
For researchers entering the ceramics field, one of the first key terms they will learn about is sintering.
Sintering is the process of compacting and forming a solid mass of material through application of heat and pressure below the melting point. It is an essential step in ceramics processing to achieve final density of a ceramic part.
While there are numerous sintering methods, microwave sintering and the newer flash sintering technique offer improved energy efficiency. Instead of heating up an entire furnace to sinter the part, these methods achieve total or partial heating within the ceramic itself through a coupling between the material and an electromagnetic or electrical field.
However, because heating occurs within the sample, ceramics processed using microwave or flash sintering commonly experience hot spots, i.e., the development of local overheating in certain regions.
Understanding the mechanisms that drive hot spot development can help researchers manage this phenomenon. A recent paper provides a useful look at these factors and describes possible ways to manage hot spot development.
The authors of the paper come from Université Grenoble Alpes and Normandie Université in France. They begin by describing typical setups for microwave sintering and flash sintering experiments before diving into the specific mechanisms that drive hot spot development in each case.
Causes of hot spot development
Overall, the simple reason hot spots develop during microwave and flash sintering is because of thermal instabilities in the samples triggered by high power and high heating rates, high positive temperature coefficients, and/or low heat conductivity (i.e., low heat dissipation).
In the case of microwave sintering, thermal instabilities typically manifest as hot spots on the surface of the sample, though hot spots within the sample are possible as well. Hot spots can also develop inside the insulating material placed around the sample.
In the case of flash sintering, thermal instabilities generally develop along a preferential current path, which results in a “hot line” rather than a hot spot.
Several factors determine where thermal instabilities will occur within a sample.
- Inverted thermal gradients. According to the authors, bulk heating in both microwave and flash sintering naturally produces a thermal gradient that is “inverted” with respect to the usual gradient obtained by surface heating in a classic furnace. This inverted gradient provides an inhomogeneous temperature profile at the scale of the specimen size, “suitable to trigger an instability in any large enough specimen,” they explain.
- Defects in the field distribution. Review articles often point to uncontrolled field nonuniformity in multimode microwave cavities as a cause of thermal instabilities. (I.e., cavities in which microwave energy bounces around inside the applicator.) The field, and therefore the dissipated power, depend on the sample shape and position in the cavity. In flash sintering, the field results from the application of voltage at specific contact points. If the sample is not symmetric, the slight off-centering can lead to thermal instabilities. Additionally, the quality of the contacts is a significant potential source of defects leading to localization.
- Composition inhomogeneity. In microwave sintering, the presence of particles of a highly absorbing material in a weakly coupling matrix is a cause of hot spots. In flash sintering, local composition inhomogeneity induces preferential current paths that lead to the development of hot spots or lines.
Strategies for managing hot spot development
Because thermal instability tends to develop from any source of localization—be it field nonuniformity or sample inhomogeneity, as described above—the first strategy for managing hot spots involves suppressing, limiting, or compensating for the sources of nucleation.
Thermal insulation is one option for reducing thermal exchanges. In the case of flash sintering, one study achieved some success using different types of insulation on a small cross-section of dog-bone-shaped samples. However, thermal insulation does not prevent localization in microwave sintering (hot spots can develop inside this material, as mentioned above).
Adapting the application of current is another way to balance the natural thermal gradient. For flash sintering, one study tested a “current path management” approach on numerical models and experiments in the case of a flat dog-bone specimen.
Regarding adaption of current in microwave sintering, a commonly used technique is the so-called hybrid microwave heating. In this process, materials with a significant ability to couple with microwaves and a weak evolution of the permittivity with temperature are placed close to or around the sample. These materials act as “susceptors” that both transform the MW energy into heat—which is then classically transmitted to the sample—and limit the field applied to the sample itself.
While the first strategy aims to prevent hot spots, the second strategy for managing hot spots aims to limit or delay their development long enough to achieve satisfactory density.
The first option is to use a controlled heating rate, as very high heating rates can trigger thermal instability. The hybrid heating technique described above achieves this option sufficiently for microwave sintering. For flash sintering, a fixed current step limits the dissipated power in the sample but does not by itself stop localization. Several studies, such as here and here, created “processing maps” revealing the maximum constant current density that can be used before localization starts to occur.
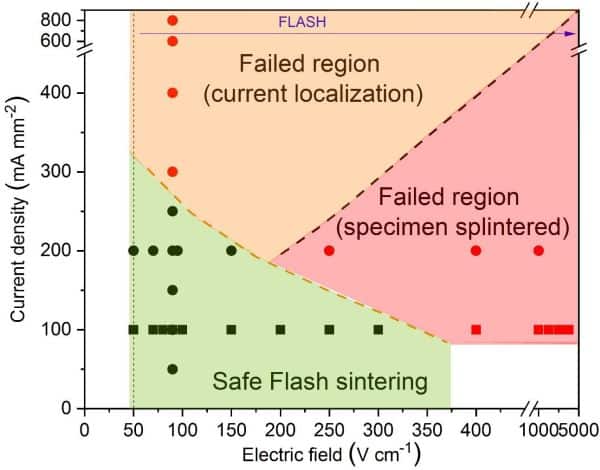
Example of a “processing map” for voltage-to-current controlled flash sintering of gadolinium-doped ceria. Credit: Prasad Mishra et al., Journal of the American Ceramic Society (CC BY-NC 4.0)
Based on results achieved with these strategies so far, the researchers conclude that “Although localization is almost unavoidable, both types of approaches contribute to obtain acceptable conditions for the densification of homogeneous ceramic parts while keeping the expected advantages of field assisted techniques, namely, fastness and energy saving.”
Finally, there is the possibility of using hot spots to achieve beneficial results. For example, researchers from Tel Aviv University in Israel developed the concept of localized microwave-heating intensification (here and here), and they identified applications such as drilling of glass, thermite reaction ignition, and local sintering of metal powder.
The paper, published in Advanced Engineering Materials, is “A viewpoint on hot spots in microwave sintering and flash sintering” (DOI: 10.1002/adem.202201742).
Author
Lisa McDonald
CTT Categories
- Manufacturing