[Image above] Laser cladded yttria-stabilized zirconia microcolumns processed at different vertical robot velocities with 20-W laser power. Credit: Vorkötter et al., Advanced Materials Technologies (CC BY-NC-ND 4.0).
When I see airplanes flying overhead, I always marvel that a device consisting largely of metal can defy gravity with seemingly little effort. However, decades of research made such flight possible, and some of the most significant developments hide in plain sight.
Thermal barrier coatings (TBCs) are a key airplane component that often escapes public view. TBCs are multilayer coatings applied to aircraft turbine blades to protect them from the high-temperature, corrosive environment of the engine. TBCs typically consist of four layers: the metal substrate, metallic bond coat, thermally grown oxide, and ceramic topcoat.
Today, the ceramic topcoat in many state-of-the-art TBCs features a columnar rather than smooth microstructure. Such a structure imparts a certain pseudo-plasticity to the coating, which translates into better tolerance to spalling, strain, and thermal shock.
As with any material, usage leads to wear of TBCs, and current methods for repairing this multilayer coating face limitations. For example, the inability to perform complex spot repairs can lead to inadvertent blockage of the cooling holes, which help prevent turbine blades from overheating. To avoid blockage, it can become necessary to perform a full coat removal and reapplication to address localized damage. Thus, there is a great need to develop methods for performing intricate point reconstruction without clogging the cooling system.
In a recent open-access paper, researchers from Forschungszentrum Jülich (FZJ) in Germany proposed a new laser-cladding-based additive manufacturing technique named Clad2Z that they say shows great potential for repairing localized damage in thermal barrier coatings.
Laser cladding is a surface modification technique that conventionally is used to deposit metal layers. It involves feeding a stream of powder or a wire into a melt pool that is generated by a laser beam as it scans across the target surface, depositing a coating of the chosen material.
Airplane manufacturers have used laser cladding with metal powder to repair turbine blades for several decades. Trying to deposit a ceramic coating on the metal blade using this technique, however, almost inevitably leads to crack formation due to high residual stress from solidification shrinkage and thermal expansion coefficient mismatch between the coating and blade.
That is, if you are trying to deposit a smooth, homogeneous ceramic coating. If instead you are trying to produce microcolumns, which many state-of-the-art TBC ceramic topcoats consist of, “the formation of cracks due to thermomechanical stresses can in principle be suppressed—even for completely dense columns, if they have a sufficiently small cross section,” the FZJ researchers write in the paper.
For their study, the researchers used laser cladding to produce a coating made from yttria-stabilized zirconia (YSZ), which is one of the most widely used materials for TBCs.
Their process involves using an argon gas jet to blow a fine YSZ powder into a laser-generated melt pool on Inconel 738, a nickel-based superalloy commonly used as a blade material. They slowly moved the laser beam and powder feed upward about five millimeters per second, allowing them to grow the YSZ microcolumn in a precisely controlled manner.
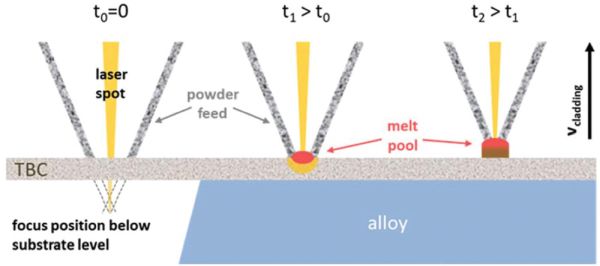
Repeated hundreds of times, they created an entire forest of closely spaced microcolumns, each less than half a millimeter to six millimeters long. Because the columns were created individually, the process did not block any of the cooling holes.
Thermal cycling performance tests showed the Clad2Z TBCs outperformed TBCs created through suspension plasma spraying, an evolving technique for manufacturing columnar TBCs. The Clad2Z TBCs also performed well within the range of commercial TBCs deposited via electron beam physical vapor deposition, which is the established state-of-the-art method for manufacturing columnar TBCs.
“Once further development and certification have taken place, components with conventional thermal barrier coatings could be repaired [using this new method],” says Christoph Vorkötter, first author and previous FZJ postdoctoral researcher, in an FZJ press release (translated).
The researchers applied for a patent for their new method and are looking for partners in industry to help advance development. “We are quite optimistic about this,” says ACerS Fellow Olivier Guillon, senior author and director of the Institute for Energy and Climate Research at FZJ, in the press release.
The open-access paper, published in Advanced Materials Technologies, is “Additive manufacturing of columnar thermal barrier coatings by laser cladding of ceramic feedstock” (DOI: 10.1002/admt.202200098).
Author
Lisa McDonald
CTT Categories
- Aeronautics & Space
- Manufacturing
- Material Innovations