[Image above] Schemes of the crack-healing mechanism induced by anodization in ceramic-based composites. Osaka University researchers found anodic oxidation allowed them to self-heal ceramic-based composites at room temperature. Credit: Journal of the American Ceramic Society
When it comes to self-healing materials, we’ve given quite a bit of coverage to self-healing concrete on CTT. But research on healing scratches and cracks takes place across all types of materials (just check out this self-healing shoe!).
One material that is difficult to self-heal is ceramic-based composites. Like concrete, ceramic-based composites are materials that play a large role in our daily lives—they can be found in aircraft engines, car brakes, and different types of power plants (from solar to nuclear). And some of their most advantageous qualities—high chemical and thermal stability—are also reasons why creating self-healing versions of ceramic-based composites is challenging.
To fix a crack in ceramic-based composites, scientists commonly rely on a high-temperature heat treatment. At high temperatures (generally above 1,000°C), a secondary sintering process takes place, followed by an oxidation reaction and oxide formation, which closes the crack.
Though this high-temperature heat treatment works, it is not an ideal solution. At these high temperatures, unexpected and/or unwelcome reactions (such as catastrophic oxidation) can take place in addition to desired oxidation, and excess grain growth may be triggered by secondary sintering. Additionally, only standalone ceramic parts can receive thermal treatment, limiting the practicality of this healing process.
What if scientists could perform oxidation at room temperature instead? That was the question asked by researchers at Osaka University—and that is the process they accomplished using anodic oxidation.
Anodic oxidation, unlike high-temperature heat treatment, relies on an electrochemical method to initiate oxidation and thus can take place at room temperature. Conductive metals have been repaired at room temperature using this method, but, according to the Osaka researchers, the technique has not been applied to ceramics until now.
To achieve anodization of their ceramic, the researchers explain in the paper that they needed to overcome two challenges. First, they needed to transform the ceramic material from insulating to conductive, which could be achieved by embedding metal particles into the ceramic matrix. Second, they then needed to convert these embedded metal particles into oxides (perform the actual anodization).
In previous studies, the Osaka researchers dispersed fine metallic micrometric titanium particles into an aluminum oxide (Al2O3) ceramic matrix, creating electrically conductive Al2O3/Ti composites. Based on these results, they hypothesized the titanium particles could be anodized to form titanium oxides, and that is what they tested in this study.
They cracked their Al2O3/Ti composite using an FV‐310e Vickers hardness tester and then performed the crack-healing anodization at room temperature in 1 mol/L H3PO4 electrolyte solution using platinum as the cathode and the composites as anodes. The anode and cathode were set 15 mm apart, and anodization took place under three different conditions: two conditions (A1 and A2) used a three-step process, while the last condition (A3) used a one-step process.
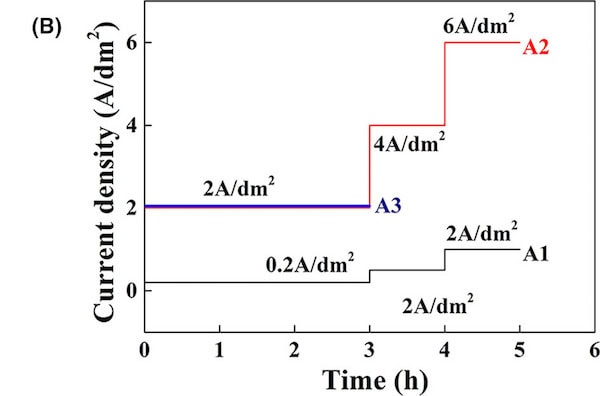
Osaka University researchers tested three different anodization conditions for healing ceramic-based composites. Conditions A1 and A2 used a three-step process, while condition A3 used a one-step process. Credit: Journal of the American Ceramic Society
One of their most crucial discoveries was that while samples with higher electrical conductivity (containing more titanium particles) were more effective for anodization, samples with lower electrical conductivity and fewer titanium particles displayed better crack-healing ability. The researchers attributed this finding to differences in fracture toughness.
The sample with lower conductivity and fewer titanium particles had a higher fracture toughness value, leading to shorter crack length during crack propagation. In contrast, the sample with higher conductivity and more titanium particles had a lower fracture toughness value, leading to longer crack length during crack propagation. “Based on the obtained results, when comparing the fracture toughness and the conductivity, the former had a stronger influence in the crack-healing ability for the same indentation load,” the researchers explain in the paper.
When looking at individual samples, the researchers found size of the crack open distance (COD) determined what current density was needed to heal the crack. For example, in samples containing 20 vol% titanium, when current density was 3 A/dm2 and COD was greater than 0.5 μm, part of the crack remained unconnected. However, when COD was less than 0.3 μm, the expanded oxides sealed the crack. “For different crack sizes, the optimal anodization conditions must be experimentally determined,” the researchers say.
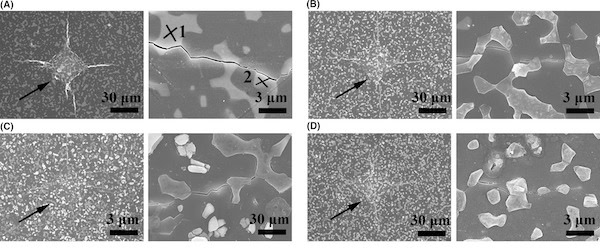
SEM micrographs of the cracked Al2O3/20 vol% titanium composite (A) before anodization and after crack healing under conditions (B) A1, (C) A2, and (D) A3. Arrows indicate the indentation. Credit: Journal of the American Ceramic Society
Though their study focused on Al2O3/Ti composites, the researchers say this technique is not limited to that composite system. “The results of our study can also be applied to ceramic-based composite systems other than Al2O3/Ti composites as a new crack-healing method for ceramics and a technique for ensuring the reliability of the ceramics themselves,” senior author Tohru Sekino, ACerS member and professor of engineering at Osaka University, says in an Osaka University press release.
Additionally, the researchers emphasize that their Al2O3/Ti composites could be of great importance for unexplored potential applications. “With the combination of the high strength of the Al2O3 ceramic and the high fracture toughness and better biocompatibility of the [titanium] metal, the resultant Al2O3/Ti composites are expected to be useful as structural components in engineering applications and as biomaterials with novel functions, such as room‐temperature crack healing,” the researchers add in the paper.
The open-access paper, published in Journal of the American Ceramic Society, is “Electrochemically assisted room-temperature crack healing of ceramic-based composites” (DOI: 10.1111/jace.16264).
Author
Lisa McDonald
CTT Categories
- Material Innovations