[Image above] Photograph of the polished Fe:ZnSe transparent ceramic sintered at 900°C under 90 MPa for different times. The ceramics could prove an ideal lasing material for mid-infrared lasers. Credit: Yu, Carloni, and Wu; Journal of the American Ceramic Society
Ever since Waymo launched its first commercial autonomous ride-hailing service in December 2018, many more companies have launched their own prototypes. And though the coronavirus pandemic has put a halt on some of these tests, it also highlighted some of the potential strengths of self-driving vehicles, such as continuing essential deliveries when everyone is quarantined at home.
For self-driving vehicles to become a common reality, though, there still is much technological advancement that needs to occur. In particular, LiDAR needs to be improved.
LiDAR stands for “light imaging, detection, and ranging” and is an integrated system that measures the distance to a target by illuminating the target with laser light. Data from LiDAR is used to build a 3D model of the environment around the car.
Most companies working on autonomous vehicles believe LiDAR is an essential part of the sensor suite (Tesla is a notable exception). In addition, many other emerging applications—such as robotics, high-resolution mapping, security, laser guidance, biology and conservation, and physics and astronomy—use LiDAR as well.
A key component of the LiDAR system is the laser light source. “Modern mid-infrared laser sources and detectors primarily use the atmospheric window from a wavelength of 3–5 μm wavelength because of the high-resolution accuracy,” Yiquan Wu, SUNY Empire Innovation Professor at Alfred University, explains in an email. “Therefore, high-powered mid-infrared lasers are essential for developing high-performance LiDAR systems.”
Currently, transition metal ion-doped II-VI chalcogenide materials are the most favorable candidates for broadly tunable and room-temperature mid-infrared (2–5 μm) laser gain materials. “However, creating such laser ceramics remains a significant challenge,” Wu says.
The four main methods for preparing TM:II-VI laser materials—physical vapor transport growth, melt growth, solid phase recrystallization, and thermal diffusion—deal mainly with these materials in their crystalline form, which places limitations on the materials’ size, dopant concentrations, and homogeneity of lasing ion distribution. These limitations make it difficult to scale-up output power of the laser.
In contrast, preparing TM:II-VI laser materials in their ceramic form could offer some advantages.
“Compared to crystal materials, transparent ceramics have unique advantages which are important in the development of high performance lasers: such as easy fabrication of composite structures with different doping content, heavy and homogeneous doping of rare earth ions, and fabrication of large size components,” Wu, postdoctoral researcher Shengquan Yu, and graduate student David Carloni write in a recent paper. “Because of these advantages, material scientists have made great efforts to fabricate TM:II-VI laser materials using the ceramic method.”
In the new paper, Wu, Yu, and Carloni expand on previous ceramic processing attempts—with very promising results.
They prepared iron-doped zinc selenide (Fe:ZnSe) transparent ceramics by spark plasma sintering Fe:ZnSe nanopowders they created using co-precipitation. (Prior to their research, reports of Fe:ZnSe transparent ceramics prepared using co-precipitated powders were scarce.) Then, they used scanning electron micrographs to analyze the effects of sintering temperature, pressure, and time on the microstructure.
The researchers determined that Fe:ZnSe transparent ceramics sintered at 900°C under 90 MPa for 120 minutes presented the best transmittance (about 60% at 1.4 μm grain size and 68% at 7.5 μm).
“In conclusion, the transparent ceramic fabrication method (including the coprecipitation of Fe:ZnSe powders) discussed in this paper provided an alternative for creating Fe:ZnSe mid-infrared materials,” they write.
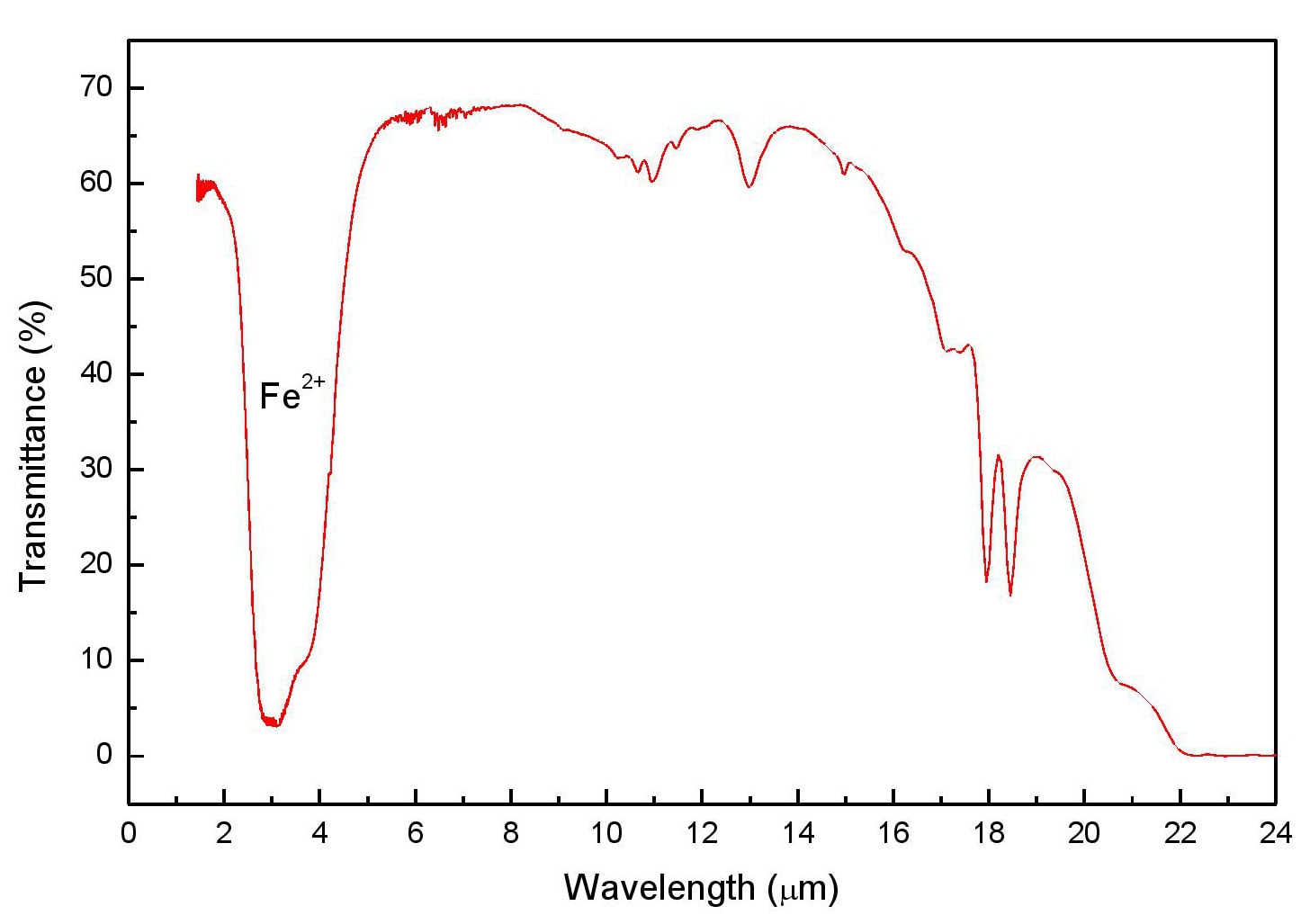
The transmission spectra of Fe:ZnSe transparent ceramic (thickness 3 mm) sintered at 900°C under 90 MPa for 120 minutes. Credit: Yu, Carloni, and Wu; Journal of the American Ceramic Society
To test the potential of their Fe:ZnSe ceramics, Wu’s group contacted professor of physics Sergey Mirov from the University of Alabama at Birmingham. Mirov and his group took the ceramics that Wu’s group created and demonstrated the first room-temperature gain-switched lasing of the material.
“The maximum output energy was measured to be 0.7 mJ. The slope efficiency was measured to be 3.5% and was limited by scattering losses,” they write in conference proceedings for the 2020 CLEO Technical Conference.
(University of Alabama at Birmingham graduate researcher Krishna Karki will present the results at the conference, which will be held in an all-virtual format on May 11–15.)
Although Wu says this output energy—and the efficiency—are low, they plan to increase the output by studying the technique further.
“Purification of synthesized powders and post-sintering processing is planned as an effort to increase the output efficiency,” he says.
The paper, published in Journal of the American Ceramic Society, is “Microstructure development and optical properties of Fe:ZnSe transparent ceramics sintered by spark plasma sintering” (DOI: 10.1111/jace.17144).
Author
Lisa McDonald
CTT Categories
- Material Innovations