[Image above] Andrew Sherman. Credit: ACerS.
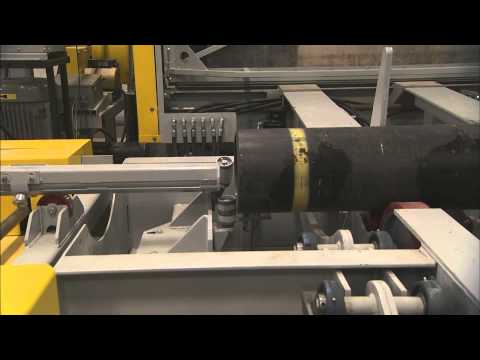
This video shows the process developed by MesoCoat (Euclid, Ohio) to clad the interior surface of carbon steel pipe with a corrosion-resistant stainless steel layer. The company celebrated a “grand opening” last week. Credit: Nanotech Surfacing; YouTube.
The “Rust Belt” is going to need a new moniker if new work by entrepreneurs and researchers in the Great Lakes region is any indicator. One way the region is rejuvenating itself is, ironically, by fighting rust.
Corrosion is very expensive-its relentless gnawing costs the US about $7 billion per year. Also, new applications, especially in the oil and gas industry, are known to be highly corrosive environments.
Andrew Sherman, a Cleveland-area engineer and serial entrepreneur, got to thinking about what it would take to get the performance of a stainless steel in the guise of a carbon steel, the latter, of course, being much less costly than the former. He realized that what really mattered was that the “business” surface of a pipeline needs to look and act like a stainless steel; it matters less what the rest of the object is.
The idea is not new; corrosion protection coatings and claddings have been used for a long time, extending back into the BC era. In modern industrial times, weld overlay claddings are the state-of-the-art technology for corrosion protection of pipeline. However, the weld overlay process is slow because it lays down the coating one line at a time.
Sherman licensed a high-intensity plasma arc lamp technology developed at Oak Ridge National Laboratory, hired a few sharp metallurgists from Case Western Reserve University, and developed a new process for rapidly applying rugged, corrosion-resistant claddings on carbon steel pipe. When it looked like the new coating technology would be effective, Sherman started up a new company, MesoCoat, which is a spin-off from his other company, Powdermet. The company and its technology picked up some plum accolades last year when the Wall Street Journal gave it top honors in the manufacturing technology category of the publication’s Technology Innovation Awards. Earlier, in 2011, Forbes listed MesoCoat as one of the top 100 most promising domestic companies.
About three years ago I was at the groundbreaking ceremony for MesoCoat’s new manufacturing facility in Euclid, Ohio, and last Friday I was invited back to the facility’s grand opening. (See pictures below.)
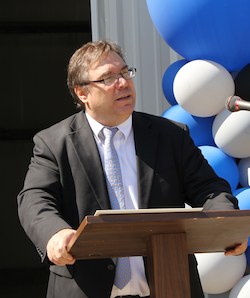
Andrew Sherman welcomes guests to the grand opening of MesoCoat’s new production facility in Euclid, Ohio. Credit: ACerS.
In his welcoming remarks, Sherman said, “Corrosion is preventable through good policy and good science. Very few of our corrosion problems cannot be solved in terms of technology, but [many current solutions] are not economically feasible.”
The MesoCoat–Powdermet campus occupies about 13 acres of facilities that used to be home to TRW during its military-industrial heyday. As you can imagine, the local dignitaries were delighted to be at a grand opening of a new research and manufacturing plant. Besides city and state politicians, representatives from Case Western Reserve University, the University of Akron, ASM International, suppliers, contractors, and local industry were also there.
Sherman, who is CEO of the company, said in his remarks that three years ago MesoCoat had one employee—now it employs about 60. The largest market for the clad pipe is the oil and gas industry, “The markets are unbelievable,” he says. According to a cleveland.com article, MesoCoat’s business model expects to achieve revenues of $400–500 million in three years.
Because of its weight and shipping costs, it is most economical to produce pipe somewhat close to where it will be used. MesoCoat and its parent company, Abakan, are working on getting production facilities up and running in Brazil and Canada, too, even while they continue to work out the manufacturing details in Ohio.
Meanwhile, the June-July issue of the ACerS Bulletin will feature an article by the University of Buffalo group led by Sarbajit Banerjee on their work on nanocomposite corrosion prevention coatings. The group reports that their graphene/polymer and graphene/carbon nanotube/polymer coatings on steel can reduce corrosion rates by several orders of magnitude compared to galvanized steels. The idea behind the research is to discover and develop new coating materials with superior functionality that can be applied using existing manufacturing processes.
So, if the “Rust Belt” is no longer descriptive of the Great Lakes region, what is? Any ideas?
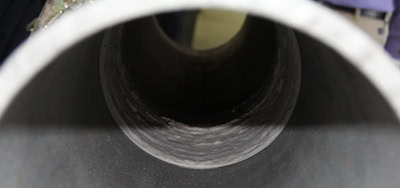
A slurry of cladding particles is deposited inside the pipe after it goes through a grit blasting and cleaning process. Credit: ACerS.
Author
Eileen De Guire
CTT Categories
- Energy
- Manufacturing