[Image above] Physical appearance of frit thermally treated (left) by a conventional industrial process and (right) by using microwaves energy in a pre-industrial process. Credit: Reinosa et al., International Journal of Applied Glass Science
Cutting costs and reducing emissions are the twin challenges for ceramic and glass manufacturers. And while there are various methods to tackle each of these challenges individually, reducing the amount of energy needed to process materials provides one clear path to achieving both goals simultaneously.
When deciding how best to reduce energy needs, many manufacturers look at how to reduce energy during the production of powders and frits, which are among the most energy-intensive steps in ceramic and glass production. While numerous potential methods for reducing the amount of energy needed during powder and frit production have been demonstrated in the laboratory, validating these processes at larger scales is necessary for moving them into production.
In a recent paper published in the International Journal of Applied Glass Science, Julián Jiménez Reinosa and Jose F. Fernández (Spanish National Research Council | CSIC), Beatriz García‐Baños and José Manuel Catalá‐Civera (The Polytechnic University of Valencia), Ángel M. López‐Buendía (InnCEINNMAT, SL), and Luis Guaita (Keraben Systems) looked at how microwave processing may serve as an energy-reduction method that works on a large scale.
Microwave processing uses microwave radiation to heat a material, meaning the method relies on a material’s interaction with the electromagnetic field to work. It will not work for materials like quartz with a low loss factor (capacity to transform energy into heat).
Compositions for glazing frits are typically complex and contain materials with strong dipoles and ionic conductors, which make them favorable to heating via microwaves. Unfortunately, knowledge of these properties is not sufficient to predict the heating profile as the properties change with temperature. So, an important part of the recent study was characterization of microwave dielectric behavior of materials as a function of temperature.
In their study, the researchers prepared glass frit using microwave heating at the 10 kg/hr pre-production (“pre-industrial”) scale. They found that the structure and transition temperatures of their microwave-heated material were similar to those of a commercial frit with similar composition produced in a traditional gas-fired continuous furnace.
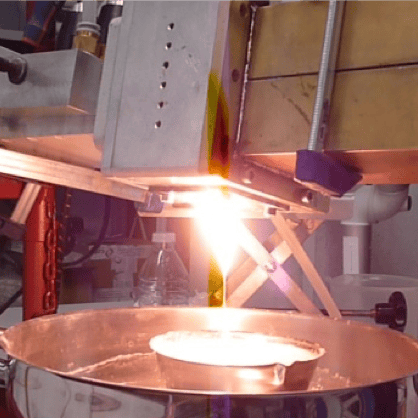
Quenching of frit composition after being heated by microwaves energy (from the article’s supporting information). Credit: Reinosa et al., International Journal of Applied Glass Science
After creating the microwave-produced frit, the researchers applied it as a ceramic glaze in order to test its applicability. They found that glazes made from the microwave-produced frit created a glazed layer that was similar in color, gloss, and hardness to glazes made from commercial frits.
In regard to energy consumption, the researchers found the microwave processing method and the traditional gas-fired continuous furnace diverged dramatically. The researchers estimated that microwave processing used 0.82 kWh/kg of electricity whereas the gas-fired furnace used 2.37 kWh/kg of electricity and natural gas—a 64 percent difference in energy usage! While the researchers estimate the two methods currently produce similar levels of carbon dioxide emissions, as more electricity is generated from renewable resources instead of fossil fuels, the microwave processing method will result in CO2 output reductions as well.
In the conclusion, the researchers note that their study shows the potential of microwave processing to replace conventional methods in some situations, thus opening opportunities to reduce energy requirement and gas emissions.
The paper, published in International Journal of Applied Glass Science, is “Feasible glass‐melting process assisted by microwaves” (DOI: 10.1111/ijag.13093)
Author
Jonathon Foreman
CTT Categories
- Glass
- Manufacturing