[Image above] In-situ sintering of alumina (bright phase) and zirconia (dark phase) particles that happened to be aligned. Note the shrinking of the neck indicated by the red arrow increases the sintering stress and precedes rigid body motion, densification, and particle rotation. Similarly, shrinkage of the alumina grain highlighted by the blue arrow, via coarsening, drives densification of the overall length of the structure. Such effects are not captured in analytical models assuming constant volume grains, which could lead to incorrect predictions of the sintering stress evolution. Credit: Shen Dillon
The notion that sintering is not diffusion rate limited will likely garner some consternation. Ubiquitous diffusion-rate-limited kinetic models have been used to understand, interpret, and engineer sintering for over a half century.
Less controversial would be the suggestion that the models for grain-boundary-mediated creep at low stresses do not conform to existing models. The low-stress, nonlinear creep response has often been attributed to some combination of point defect emission and absorption kinetics, grain boundary sliding, and/or lattice plasticity, but much experimental data does not fit well any existing models.
Sintering of powders larger than about 100 nm typically occurs at average sintering stresses well within the regime associated with nonlinear grain boundary creep, as seen in the schematic below. This disparity between sintering and creep has largely been overlooked within the literature.
There are, furthermore, many persistent questions in the sintering literature related to heating rate effects, field effects, shear stress effects, residual stress evolution, cold sintering, and two-step sintering, among other effects. These unknowns might lead one to question whether the phenomena are being interpreted within the appropriate framework.
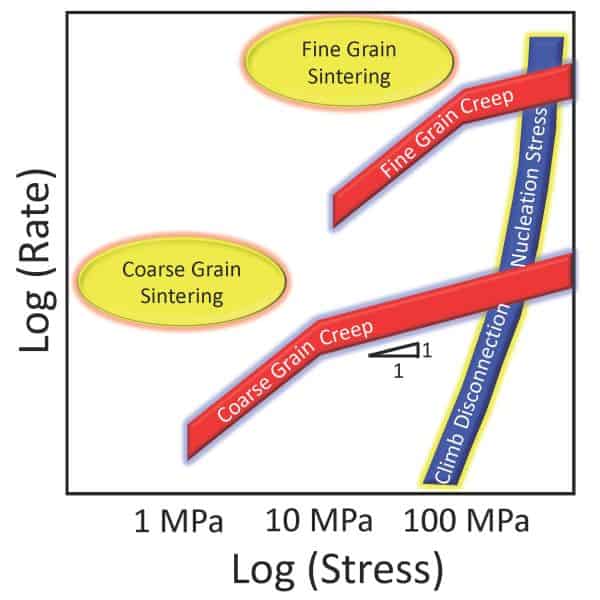
Schematic depicting the relative rates of sintering and creep as a function of the average driving force along with the relative magnitude of the disconnection nucleation stresses. Credit: Shen Dillon
What grain boundary processes are necessary for grain-boundary-mediated sintering and creep?
Densification and grain boundary creep require the removal and/or addition of atomic planes at the boundary. This process necessitates three fundamental components:
- A diffusional flux of point defects to and from sinks and sources,
- The absorption and emission of those point defects at sinks or sources, and
- The presence of or nucleation of sinks and sources that climb in response to the flux.
Disconnections, i.e., line defects with Burgers vector and step character, serve as the primary grain boundary sources or sinks when they have Burgers vectors lying out of the grain boundary plane. Preexisting disconnections can only mediate a limited amount of strain, which is much less than typical of sintering densification. The stresses necessary to nucleate climb-mediating disconnections should be several orders of magnitude larger than the average sintering stresses or applied stresses in which these processes become facile.
What observations motivate the need for a new model?
Small-scale bicrystal creep experiments performed in recent years reveal that the applied and sintering stresses necessary to induce grain boundary strain are, indeed, quite large, consistent with predictions for disconnection nucleation. Such experiments also reveal that grain boundary strain during sintering and creep is intermittent and can induce rotation, consistent with disconnection nucleation phenomena.
A challenge has been rationalizing the discrepancies between bicrystal and polycrystalline sintering and creep, both in terms of the relative magnitudes of the required stresses and the proposed rate limiting mechanisms.
What assumptions in classical sintering models could lead to the wrong conclusions?
Classical sintering models often begin with geometric assumptions of constant volume grains, which makes the analysis mathematically tractable. Such models predict a rapid decay in the sintering stress toward relatively small values (see the schematic below).
When coarsening occurs, however, the sintering stress can increase as some grains shrink. In the limit of no densification, a shrinking particle will de-sinter, at which point the sintering stress reaches the value necessary to overcome the work of adhesion. Coarsening powders can thus access a broad range of sintering stresses between zero and the failure stress, making it possible for the boundary to sample sintering stresses large enough to nucleate disconnections that mediate densification.
A new sintering model was recently developed to account for the way coarsening can drive disconnection nucleation, which facilitates densification. This new model cannot be distinguished from the classical model by considering isothermal sintering power law exponents; however, it does make unique predictions about the temperature dependence of sintering kinetics and residual stress evolution.
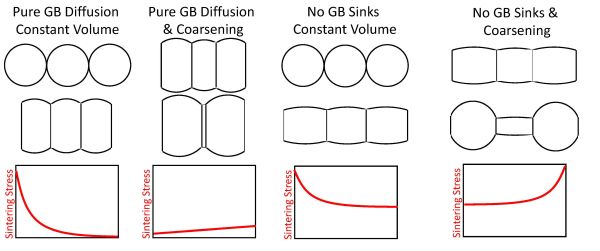
Schematic showing a line of particles before and after a sintering step under conditions where the grain boundaries are either perfect sinks or contain no sinks and the grains are either constant volume or allowed to coarsen. Coarsening enables the sintering stress to increase. Credit: Shen Dillon
What is missing in classical treatments of grain boundary creep?
The discrepancy between applied stress and local stress has already been considered in numerous studies in the context of creep cavitation. These treatments typically assume singularities at triple junctions, second phase particles, or grain boundary steps act as stress concentrators.
A just-published study demonstrates that applying these stress concentration models to disconnection nucleation kinetics do well predicting the stress, temperature, and grain size dependencies of creep for a broad range of systems. The nucleation rate limited sintering and creep models provide good agreement between all four sets of data, i.e., bicrystal and polycrystalline creep and sintering.
Does the model really matter?
Both the classical models and the new proposed models fit isothermal kinetic data well. Such data and their fitting have often been used to infer grain boundary properties, and using the wrong model could lead to the wrong conclusions.
In addition to fitting the experimental data well, the new models make useful predictions and provide new avenues to understand and design materials and processing. For example, the new sintering model naturally predicts that high heating rates favor densification over coarsening, which is observed in practice.
The model also predicts grain size density evolution well for a variety of starting conditions based on a small number of sintering or creep data points. This knowledge can help researchers improve their master sintering curve type approaches, which are typically developed for a single starting particle size.
The new model also predicts residual stress evolution that qualitatively differs from classical models because the nucleation process is discrete and large local stresses can be stabilized below some threshold value. The physical properties of grain boundaries should also depend on their disconnection content, providing a path toward engineering their properties.
The open-access sintering paper, published in Acta Materialia, is “Interface nucleation rate limited densification during sintering” (DOI: 10.1016/j.actamat.2022.118448)
The creep paper, published in Acta Materialia, is “A nucleation rate limited model for grain boundary creep” (DOI: 10.1016/j.actamat.2023.118718).
About the author
Shen Dillon is an ACerS Fellow and professor of materials science and engineering at the University of California, Irvine. His scientific interests relate to understanding the key role played by inorganic interfacial structure–property relationships in affecting the performance of systems in extreme environments.
Author
Shen Dillon
CTT Categories
- Modeling & Simulation