[Image above] Credit: Toyota UK; Flickr Creative Commons License.
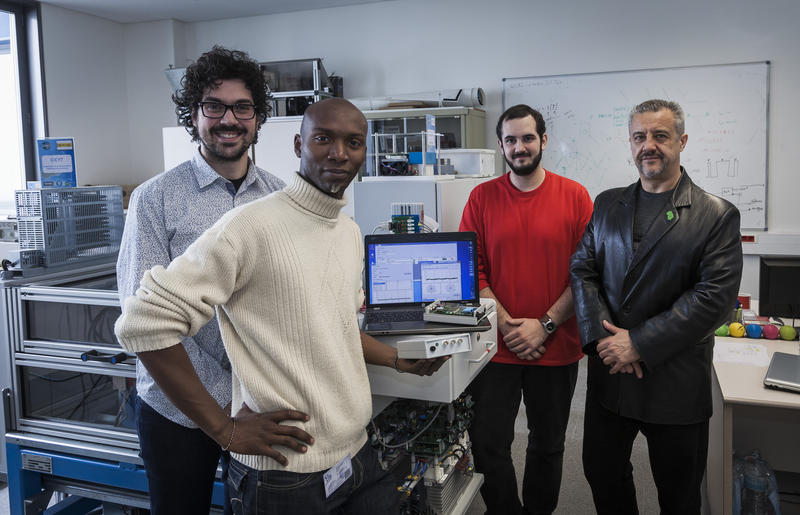
Luis Romeral (far right) and his team of researchers, along with researchers at other institutes and companies in Europe, have developed an ultrasonic sensor to detect faults in industrial machines. Credit: Ramón Fornell; UPC; SINC.
It’s often said that a business is only as good as its workers. And in many businesses, those that perform the work are both humans and machines. So in addition to employee safety, protecting machines from breakdown is critical to maintain productivity and reduce operating costs.
New research lead by Spain’s Polytechnic University of Catalonia (UPC) may help companies do just that, with the help an ultrasonic sensor that can diagnose faults in machinery before a major malfunction occurs.
The research is part of a larger-scale European project called Mosycousis, which received €1.7 million over two years to study wireless acoustic sensors for detecting industrial machine failure. In addition to UPC, several companies and institutes from Ireland, Estonia, Poland, and Romania collaborated on the project. According to the Mosycousis funding award summary, “Unexpected failure in an industrial production chain not only involves the costs of failed parts replacement and the associated man-hour labor, but downtime costs also have to be considered. To keep a machine functioning well, it is a must to have good predictive maintenance, as it helps to reduce operating risks, avoid plant failures, provide reliable equipment, reduce operating costs, eliminate defects in operating plants, and maximize production.”
Current technologies exist to monitor machine function, but these rely on the detection of vibrations to signal when attention or repair is needed. But, “the problem is that vibrations often appear when the machine already has a serious breakdown,” lead researcher and Mosycousis coordinator Luis Romeral says in an news release from Spain’s Information and Scientific News Service (SINC).
“Often, mechanical wear manifests initially as an internal fracture or fissure in the metal,” he says. “When this crack appears, the material begins to emit ultrasonic waves, which are high-frequency, low-amplitude sounds. These emissions are the ones we capture with the sensor head, and we separate those that reflect the normal operative state from those caused by an internal fracture problem.”
The new sensors, which detect ultrasound in the structural fault “sweet spot” of 50–300 kHz, can detect a potential problem more quickly than vibrational sensors to prevent a problem from becoming a failure. The device is a stand-alone sensor “that feeds off the energy in the environment (from heat, mechanical, or vibration sources)” and can wirelessly transmit the data it collects.
According to an article in Industry Week, overall equipment effectiveness (OEE) rates—a measure of the productiveness of manufacturing operations—are often around only 50 percent. That leaves a lot of room for improvement, and keeping machines running smoothly is a key variable in that equation.
These new sensors could help factories and businesses adopt a more proactive approach to machine maintenance strategies. This approach leads right into a concept called lean maintenance, one part of a larger thought process for maximizing efficiency called lean manufacturing. Both “lean” strategies aim to maximize efficiency by reducing waste and enhancing flexibility, among others.
The sensors could find use in a wide range of applications and environments. According to the SINC news release, the sensors have applications in rotating machinery, systems with gears, gearboxes, compressors, pumps, engines, and ventilators. “They could be used in production companies, metal manufacture, packaging chains and food packaging, the pharmaceutical industry, etc.,” Romeral says.
In addition, the authors particularly note the sensors’ utility in locations that are difficult to access, and in the maintenance of things like wind turbines and railway systems. And even, perhaps, to detect breaks in bone.
“For this reason, we have begun a new line of work and initiated contacts, as yet confidential, in this field,” Romeral adds in the news release.
The team presented their findings late last year at the 2013 9th IEEE International Symposium on Diagnostics for Electric Machines, Power Electronics and Drives (SDEMPED).
Author
April Gocha
CTT Categories
- Manufacturing