[Image above] Scanning electron micrograph of soda–lime–silica glass powder particles. Credit: Datsiou et al., Journal of the American Ceramic Society (CC BY 4.0)
During Ceramics Expo 2019, which took place last week in Cleveland, Ohio, a frequent topic of discussion both days was additive manufacturing (AM). Many industry experts agreed that AM will noticeably affect the manufacturing industry someday, but whether that day is right around the corner or far in the future was up for debate.
If the experts had been debating glass AM rather than ceramic AM, there would have been no question that noticeable effects—if any—would be far in the future. As we wrote in a CTT article just over a month ago, glass AM is still a long way from industrial capacity.
As we explained in that article, research on glass AM has not significantly advanced since Israeli startup Micron3DP and the Massachusetts Institute of Technology’s Mediated Matter group revealed their glass 3D-printing methods in 2015.
Since that CTT came out, two new papers have been published detailing further advances in glass 3D printing.
Glass AM using laser powder bed fusion
In general terms, additive manufacturing is a process in which materials are joined (usually layer upon layer) to make objects from 3D model data. However, AM does not refer to a single technique, but rather various methods.
Some AM methods are more difficult to use with glass than others. For example, fused filament fabrication, a method that requires melting the starting material, is more difficult to use with glass than binder jetting, a method in which binder solution joins together a material in powder form.
In a new paper published in the Journal of the American Ceramic Society, researchers from the University of Nottingham and a colleague from Glass Technology Services Ltd. (Sheffield, UK) developed a laser powder bed fusion approach to glass AM.
Powder bed fusion AM techniques use energy sources like lasers and electron beams to heat a bed of powdered material until it softens or melts. As the material cools, it solidifies (fuses) to the preceding layer.
In the JACerS paper, the researchers used the powder bed fusion technique of selective laser melting to melt soda–lime–silica glass powder and resolidify it on high-purity alumina disk substrates. They found they could successfully produce cubic structures using energy densities of 80–110 J/mm3, a range that holds regardless of particle size.
“Changes in particle size of the feedstock material will not change the required energy densities for material consolidation even when different combinations of parameters will have to be selected to accommodate the new layer thickness,” they explain. “However, different feedstock compositions and, therefore, material properties will lead to changes in the required energy density.”
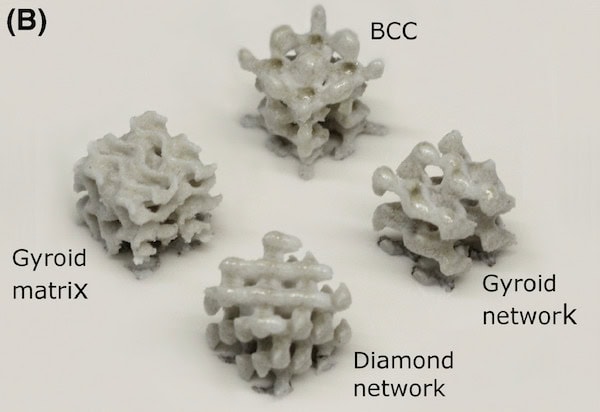
Various 10 × 10 × 10 mm3 lattice structures (2 cells/axis) created with selective laser melting. Credit: Datsiou et al., Journal of the American Ceramic Society (CC BY 4.0)
The open-access paper, published in Journal of the American Ceramic Society, is “Additive manufacturing of glass with laser powder bed fusion” (DOI: 10.1111/jace.16440).
Glass AM using fused filament fabrication
In Canada, researchers from the Centre d’Optique, Photonique et Laser (COPL) at Laval University, including ACerS member Younès Messaddeq, took a different approach to glass AM—fused filament fabrication.
As mentioned before, fused filament fabrication (FFF; trademarked term is fused deposition modeling) is more difficult than other AM techniques for 3D printing glass, because most glasses have high melting temperatures. However, the researchers performed FFF using chalcogenide glass.
Chalcogenide glass contains one or more of the chalcogen elements sulfur, selenium, and tellurium, and it softens at relatively low temperatures compared to other glasses. For the FFF study, the researchers used the chalcogenide glass arsenic sulfide (As40S60).
The researchers increased the maximum extruding temperature of a commercial 3D printer from about 260°C to 330°C. Then, they used it to produce arsenic sulfide glass filaments with dimensions similar to commercial plastic filaments.
As Yannick Ledemi, COPL postdoctoral fellow, explains in an OSA press release, chalcogenide-based components would be useful as infrared thermal imaging devices for defense and security applications. So, “This new method could potentially result in a breakthrough for efficient manufacturing of infrared optical components at a low cost,” Ledemi says.
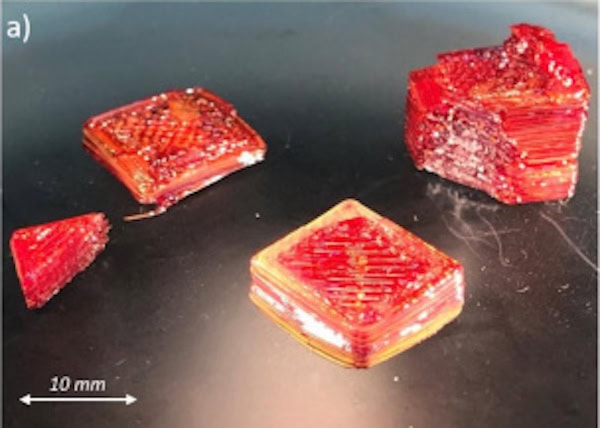
Arsenic sulfide (As40S60) printed glass samples with 100% density infill. Sample on left and right sides were fractured intentionally after processing for better observation. Credit: Baudet et al., Optical Materials Express (CC BY 4.0)
The open-access paper, published in Optical Materials Express, is “3D-printing of arsenic sulfide chalcogenide glasses” (DOI: 10.1364/OME.9.002307).
Update 05/10/2019 – The third element in the list of chalcogen elements was corrected to tellurium
Author
Lisa McDonald
CTT Categories
- Glass
- Manufacturing
- Material Innovations