[Image above] Ceramic containers on the macroscale hold coffee—what do ceramic containers on the nanoscale hold? Credit: PIXNIO (CC0)
What do solar energy and ocean-going vessels have in common? Nothing, you say. Well, according to George Kordas, senior researcher at the National Centre of Scientific Research Demokritos Institute for Nanosciences and Nanotechnology in Greece, the efficiency of both can be enhanced by ceramic nanocontainers.
Ceramic nanocontainers, as the name suggests, are nanoscale-sized hollow ceramic spheres. A well-known potential application of ceramic nanocontainers are as drug carriers in medical applications. However, ceramic nanocontainers have many other potential uses as well, as Kordas demonstrates in two recent studies.
In both studies, Kordas produced hollow nanometer-sized spheres of copper oxide (CuO), cerium oxide (CeO2), and cerium molybdate (CeMo) using sol-gel processing. Sol-gel processing uses mixtures of soluble metal salts, water, and organic species (such as solvents, sugars and polymers) that are then put through high-speed centrifugation and thermal treatments to create the nanospheres. Sol-gel processing is relatively inexpensive and scalable as it uses modest equipment and chemicals.
While Kordas used similar sol-gel methods for producing the nanocontainers in his two studies, each study takes advantage of very different nanocontainer functionalities.
From solar to electrical energy: Silica-coated nanocontainers improve conversion efficiency
In the article “Incorporation of spherical shaped CuO@SiO2 light microtraps into CuCoMnOx spinels to enhance solar absorbance,” nanocontainers are fabricated to a very specific size using materials with specific optical properties. The goal is to capture a greater portion of solar irradiance in the visible to near infrared (IR) region of the spectrum, with wavelengths from 400–2,500 nm.
To achieve these goals, the CuO nanocontainers are approximately 700 nm in diameter and the silica-coated spheres are almost 1 micrometer (1,000 nm). These sizes are within the range of IR wavelengths, meaning that waves will be able to pass through into the spheres, much like FM radio waves pass through into buildings.
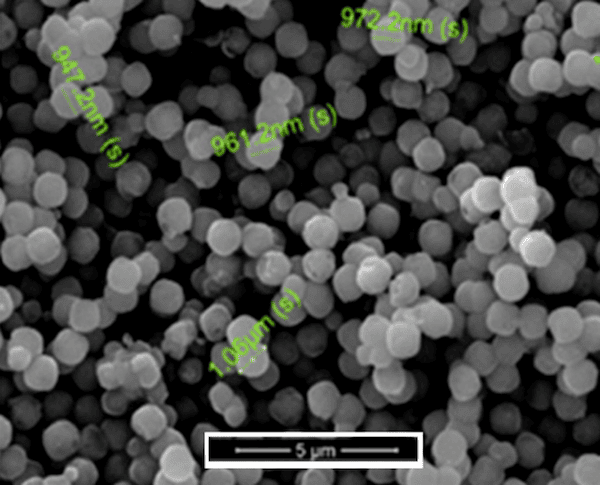
SEM of CuO@SiO2 nanocontainers. Credit: Kordas, Journal of the American Ceramic Society
The silica coating provides the mechanism for trapping the waves inside the spheres. Silica has a refractive index of about 1.5 for near-IR wavelengths, whereas the refractive index value of CuO is between 2 and 2.6 in the same wavelength range. Because the refractive index for the silica is less than that of CuO, some of the light experiences total internal reflection and cannot exit the nanocontainers, which is the same mechanism by which well-cut diamonds appear very bright and fiber optics transmit light over long distances.
The result is an increase in the ratio of energy absorbance to emittance with increasing concentration of CuO@SiO2 in the CuCoMnOx coatings. Kordas showed a doubling of this ratio with a 1% addition of the CuO@SiO2 addition to the coating scheme. This result, in turn, should lead to more efficient conversion of solar energy to electrical energy.
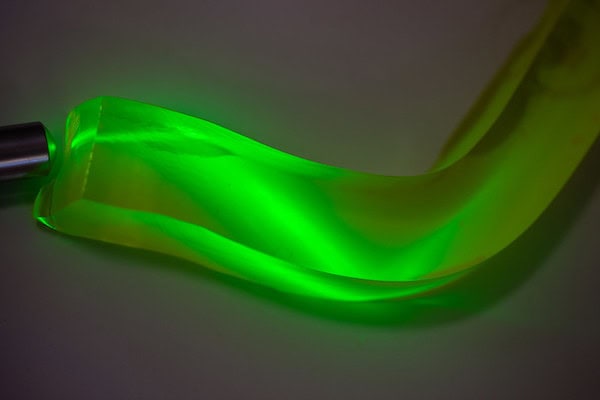
An example of total internal reflection, a mechanism harnessed in diamonds, optical fibers, and now silica-coated nanocontainers! Credit: Michelle Yost, Flickr (CC BY-SA 2.0)
It should be noted that Kordas provides a much lower refractive index for CuO in the article, which is valid for the UV spectral range but not the visible to IR range. Fortunately, this oversight does not affect his analysis and conclusions.
The paper, published in Journal of the American Ceramic Society, is “Incorporation of spherical shaped CuO@SiO2 light microtraps into CuCoMnOx spinels to enhance solar absorbance” (DOI: 10.1111/jace.16851).
Increasing up-time of ships: Nanocontainers provide corrosion resistance
The shipping application of ceramic nanocontainers takes advantage of the nanocontainers’ porous nature. Similar to nanoparticles being used for drug delivery (examples here and here), the nanocontainers are fabricated to contain environmentally friendly antifouling substances.
The accumulation of sea life on the hulls of watercraft creates two issues for ship owners. The initial micro-organisms lead to corrosion of the metal, which in turn creates even more surface area for colonization. Then the subsequent larger sea life (e.g., barnacles) create substantial drag in the water, which leads to substantially higher fuel use (up to 80% more than for a clean hull).
The most common preventative measures entail coating ship hulls with paints containing relatively large amounts of toxic biocides and copper oxide (CuO). Unfortunately, as these substances leach from the paint, they can negatively affect marine habitats. When prevention stops working and biofouling occurs, ships must be taken out of service, scraped, and repainted.
In the article “CuO (Bromosphaerol) and CeMo (8 Hydroxyquinoline) microcontainers incorporated into commercial marine paints,” Kordas filled nanocontainers of CuO and CeMo with biocides and anticorrosion agents, including hydroxyquinoline. These nanocontainers were then mixed into commercial marine coatings and applied to steel samples. One challenge encountered and solved was keeping the CeMo containers in suspension prior to mixing with the paints.
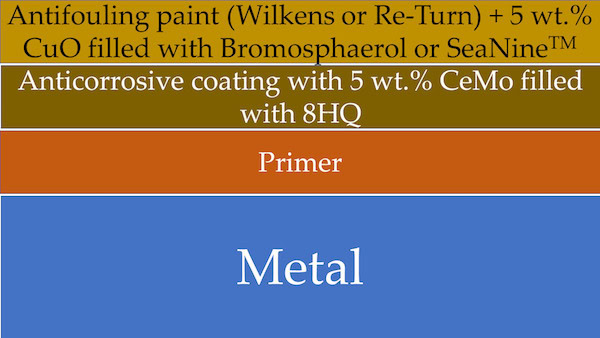
Illustration showing the three layers that were loaded with CeMo (8HQ) and CuO (Bromosphaerol and SeaNine 211). Credit: Kordas, Journal of the American Ceramic Society
The coatings were highly successful. First, the coated steels showed minimal signs of corrosion, much less than the unmodified paints. Second, the samples showed very limited amounts of biofouling—algae and some tube worms and nothing larger—after being immersed in seawater for nearly three years. The coatings have since been applied to ocean-going vessels and the results are yet to be seen.
The key environmental achievement for the nanocontainers was improving performance while using a substantially smaller amount of toxic chemicals in the paints. For example, typical commercial paints contain between 40% and 76% copper by weight. In this study, the CuO loading was 5% by weight. The reduced level of chemicals and improved performance have the potential to reduce expenses for ship owners with lower cost paints, lower operating costs due to reduced drag, and longer up-time between hull servicing.
The paper, published in Journal of the American Ceramic Society, is “CuO (Bromosphaerol) and CeMo (8 Hydroxyquinoline) microcontainers incorporated into commercial marine paints” (DOI: 10.1111/jace.16917).
Author
Jonathon Foreman
CTT Categories
- Energy
- Environment
- Nanomaterials