[Image above] University of Illinois at Urbana-Champaign professor Shen Dillon, left, and Sandia National Lab researcher Christopher Barr, right, with the new ultrahigh-temperature testing setup. Credit: Shen Dillon
As coronavirus SARS-CoV-2, the infectious agent behind COVID-19, continues to sweep the globe, countries around the world are starting to see real economic impacts, especially the global travel industry. However, there is a surprise silver lining for struggling airlines in the face of this outbreak—jet fuel prices are the lowest they’ve been in two years.
Jet fuel is a huge proportion of an airline’s overall expenditure, accounting for more than 20% of operating costs. There are multiple potential and proven ways to improve fuel efficiency, including burning fuel at hotter temperatures. However, that temperature is limited by the material from which the jet turbine is made.
Many of today’s jet turbines are made from nickel-based alloys, which have melting points of 1,200–1,315°C (2,190–2,400°F). Burning fuel at higher temperatures thus requires either cooling the turbine blades (typically done using air) or reducing the turbine’s thermal conductivity by coating the blades with more temperature-resistant materials, such as ceramics.
Currently, incorporating ceramics in jet turbines is a main area of focus for researchers. And progress has definitely been made—engines containing ultrahigh-temperature (UHT) ceramics are now commercially available. But a big challenge researchers face in bringing more UHT materials to commercialization is properly testing potential materials.
“A decade ago, advancements in aeronautical materials involved testing large, expensive models and years of development,” a University of Illinois at Urbana-Champaign (UIUC) press release explains. “Scientists and engineers now use microscale experimentation to help create new materials and understand the chemical and physical properties that lead to material failure.”
Most UHT materials tend to be brittle and extremely flaw sensitive. So not only is creating small-size samples rather than big pieces for testing easier, micro- and nanoscale testing can provide insight into deformation mechanisms on the atomic level, which translates into successfully creating macroscopic samples for bulk testing later on.
However, there is a hitch to microscale materials testing—researchers struggle to conduct these tests at the extreme temperatures experienced during flight.
“Unfortunately, it’s really difficult to perform experiments with new materials or combinations of existing materials at ultrahigh temperatures above 1,000°C because you run into the problem of destroying the testing mechanisms themselves,” Shen Dillon, professor of materials science and engineering at UIUC, says in the UIUC press release.
Fortunately, Dillon and his colleagues at UIUC, Sandia National Laboratories, and the University of California, Davis, have a potential solution to this problem—combining targeted laser heating and transmission electron microscopy (TEM) to create a new ultrahigh-temperature testing method.
In an email, Dillon explains what gave them the idea to try combining these two common techniques.
“We have worked with Khalid Hattar’s group through CINT (Center for Integrated Nanomaterials) for a number of years. They installed the laser as part of a pump-probe system that they were planning to use for other experiments. He mentioned this to me during their install process because he knew that we were really interested in doing high temperature mechanical experiments,” Dillon says. “We started using it to test metallic samples at much lower temperatures soon after it was installed … [but] we imagined that using samples or sample substrates with lower thermal conductivity, i.e. ceramics, would allow us to access much higher temperatures.”
Unlike other methods for heating materials, lasers are very good at heating a local area to extremely high temperatures while maintaining low temperatures in the neighboring regions. Additionally, by monitoring the experiments using TEM, the researchers could simultaneously observe the deformation mechanisms and determine the temperature at which the experiment took place.
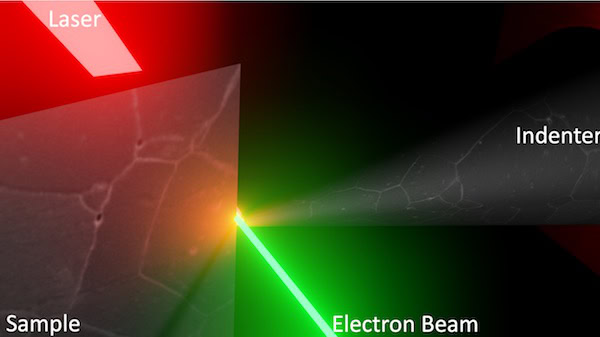
Schematic of the high-temperature experiment in action. Credit: Shen Dillon
Dillon says they were initially concerned about the high temperatures affecting the nanomechanical tester (a Bruker PI-95) even though the heating was localized, but some simple thermal modelling suggested that everything should work, so they went ahead with the experiment.
The researchers decided to test zirconium dioxide, a material often used in fuel cells and thermal barrier coatings, because Dillon’s group was already collaborating with professor Ricardo Castro’s group at UC Davis to characterize deformation of nanograin zirconia. They specifically used nanograined 10 mol% Sc2O3-stabilized ZrO2 (10ScSZ) in this study.
Testing was performed between 25°C and 2,050°C (77°F and 3,722°F), “a temperature well above anything that you could do previously,” Dillon says in the press release. These tests yielded an approximately constant fracture strength of about 0.5 ± 0.1 GPa. Overall, the experiments demonstrated how the laser–TEM technique “enables testing over a broad temperature range extended to the ultrahigh-temperature regime,” the researchers write.
Dillon says they are just finishing another paper related to studying bicrystal Coble creep and sintering in zirconia using similar experimental methodologies. They also have an NSF CER-supported project that extends this approach to systematically investigate the effects of applied electric field on interfacial transport kinetics, thermodynamics, and mechanisms, and they have performed some preliminary experiments characterizing diffusion at heterophase boundaries in ceramic-ceramic composites.
“We envision this methodology impacting a range of applications, varying from the effects of irradiation on interfacial transport to the effects of interfacial creep in the development of metal-oxide scales,” Dillon says.
The paper, published in Nano Letters, is “In situ transmission electron microscopy for ultrahigh temperature mechanical testing of ZrO2” (DOI: 10.1021/acs.nanolett.9b04205).
Author
Lisa McDonald
CTT Categories
- Aeronautics & Space
- Nanomaterials
- Thermal management